Celticoat, producteur de granulés de bois social, solidaire et ultra-moderne
Article paru dans le Bioénergie International n°51 de septembre-octobre 2017
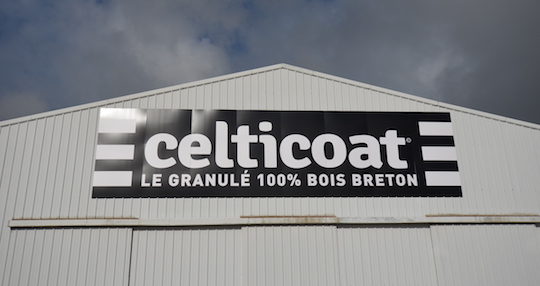
Fronton de l’entreprise Celticoat à Rostrenen, photo Frédéric Douard
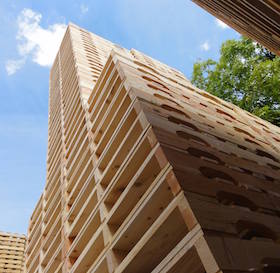
La production de palettes est à la base de toute l’activité d’Aprobois, photo Aprobois
Créée en 1988 à Carhaix au cœur de l’Argoat, le centre de la Bretagne, dans un secteur où la forêt a largement colonisé les terres agricoles les plus rudes, Aprobois, avec ses 105 salariés, transforme près de 250 m³ de bois résineux par jour et plus de 60 000 m³ à l’année. La scierie est spécialisée dans le sciage d’épicéa de Sitka, un arbre originaire de la côte nord-ouest d’Amérique du Nord. Elle produit en base 550 000 palettes par an et a aussi développé une offre de sciages pour la construction et une offre en plaquettes de scierie pour le chauffage des collectivités. Aujourd’hui, elle vient de se lancer dans la production de granulés de bois.
Une industrie sociale et solidaire
L’Argoat est à la Bretagne, ce que le Morvan est à la Bourgogne, c’est-à-dire une région au climat rude et aux sols pauvres. L’activité économique y a toujours été difficile et c’est précisément à la confluence de cette difficulté à maintenir du travail dans cette région et de la difficulté pour les personnes handicapées à trouver un emploi, que Désiré Mahé, ancien instituteur, a décidé en 1988 de relever ce double défi : créer une activité pour les personnes en situation de handicap dans la montagne bretonne.
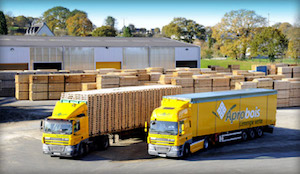
La scierie Aprobois à Carhaix, photo Aprobois
Pris au départ pour un doux rêveur, il s’est entouré, s’est fait conseiller, a appris le métier en marchant, mais toujours avec deux lignes directrices : que cela profite aux personnes handicapées et que cela se fasse de manière moderne et performante. Ainsi depuis 30 années désormais, Aprobois a toujours cherché à concilier performance économique et performance sociale en déployant des pratiques respectueuses de l’environnement.
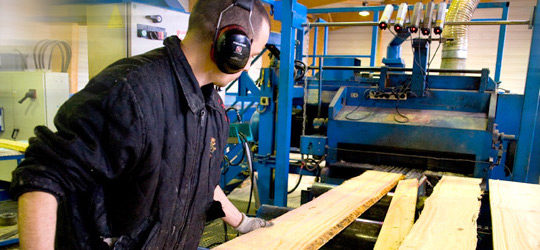
Depuis son origine Aprobois est une entreprise adaptée, photo Aprobois
Selon cette vision des choses, en 2007, Aprobois a fait évoluer ses statuts vers une SA de type SCOP, une Société Coopérative de Production gérée par ses salariés, associés majoritaires dans l’entreprise. Depuis son origine Aprobois est une entreprise « adaptée », c’est-à-dire une entreprise qui emploie majoritairement des personnes en situation de handicap. Les pouvoirs publics lui ont à ce titre attribué le label d’Entreprise Solidaire, un statut qui permet à ses clients de bénéficier d’une réduction de leur contribution AGEFIPH pour l’emploi des travailleurs handicapés.
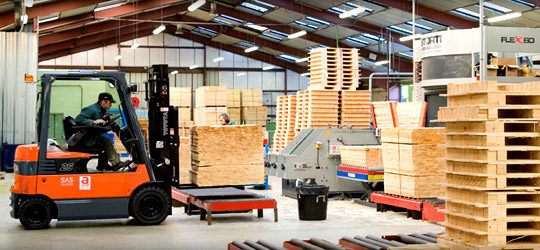
L’entreprise emploie majoritairement des personnes en situation de handicap, photo Aprobois
Autre particularité de l’entreprise : Aprobois a mobilisé des capacités d’investissement ambitieuses en émettant des titres participatifs destinés notamment aux propriétaires forestiers de la région pour pouvoir investir dans des outils de dernière génération afin de rendre l’entreprise performante, rentable et donc pérenne Ces efforts ont permis de placer Aprobois parmi les scieries les plus modernes de Bretagne.
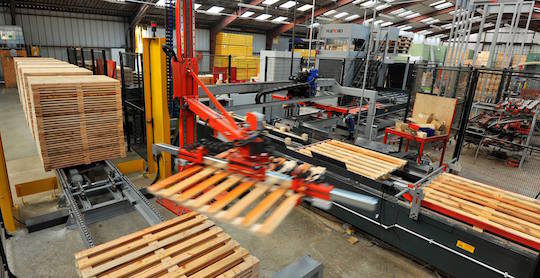
La scierie Aprobois de Carhaix a bénéficié d’investissements importants, photo Aprobois
Et plus encore aujourd’hui, 30 ans après ses débuts dans la filière bois, l’entreprise, forte de sa pertinence et de sa solidité vient d’investir sept millions d’euros supplémentaires dans une usine de granulation de bois toute neuve, à Rostrenen à 250 mètres d’altitude au cœur du massif résineux breton ! Le montage financier a été réalisé avec des banques locales et des aides financières du FEDER, de l’Etat, de l’ADEME et de la région Bretagne.
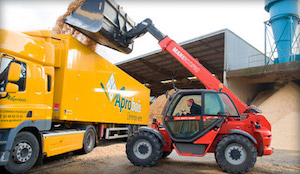
Aprobois a commencé à valoriser ses chutes de sciage en plaquettes de bois-énergie, photo Aprobois
Alors cette usine n’est pas arrivée-là par simple opportunisme mais est le résultat d’un souci permanent à valoriser l’ensemble des sous-produits de l’activité principale. Dès 1990, c’est sous forme de plaquettes forestières qu’Aprobois a commencé à valoriser ses chutes de sciage, et ses écorces vers le bois-énergie. Le premier client fut la piscine de Carhaix en 1990.
Puis l’activité principale croissant, en particulier depuis 2012 avec la mise en place d’une nouvelle ligne de sciages de petits bois, le volume des sous-produits a augmenté en proportion et il était devenu intéressant, et voire crucial, de trouver une plus-value plus importante aux sous-produits qu’au simple travers des plaquettes. Et comme le marché du chauffage à granulés, comme partout en France, s’est bien développé en Bretagne, il devenait aussi très pertinent de produire à la pointe bretonne, des granulés qui sinon devaient fatalement venir de loin.
Une bonne dynamique familiale
C’est Karine, la fille de Désiré, qui joue aujourd’hui le rôle principal dans la continuité du projet social et économique Aprobois. Car pour Désiré, dans sa soixante-huitième année en 2017, le projet Celticoat a mobilisé beaucoup d’énergie et de temps ces dernières années et c’est l’une des raisons pour laquelle il a petit à petit passé les rênes de l’entreprise à sa fille Karine.
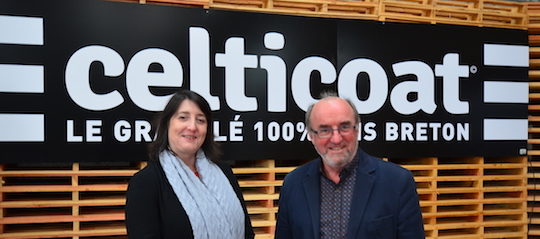
Karine et Désiré Mahé le jour de l’inauguration de Celticaot le 16 septembre 2017, photo F. Douard
Entrée dans l’entreprise en 1997 pour en assurer la gestion financière, après en poche un diplôme de l’École Supérieure de Commerce de Rennes et un MBA (Master of Business Administration) en Finlande, Karine est passée directrice adjointe en 2002, alors que Désiré venait d’être élu président de l’UNEA (Union Nationale des Entreprises Adaptées). Ensuite Karine endossa les responsabilités de directrice générale en 2010 puis de présidente directrice générale en 2015 au lancement effectif du projet Celticoat alors que Désiré concentrait tous ses efforts sur le projet.

Le local de broyage de la matière humide chez Celticoat, et plus bas le stockage, photo F. Douard
Et dans la famille Mahé, il y a aussi le fils, Christophe, qui engagé initialement dans d’autres activités, a créé Espace Bois (commerce de bois) en 2005 à Carhaix et va désormais ajouter le magasin d’usine Celticoat à ses activités.
La valorisation des produits connexes de sciage
Les 60 000 m³ de bois rond, transformés chaque année par Aprobois, génèrent environ 24 000 tonnes de produits connexes. Les billons non conformes au cahier des charges de la scierie sont transformés en plaquettes et fournissent, avec les écorces, la chaufferie de Celticoat. Sur le site de la scierie, une plateforme de stockage couverte de 1 000 m² permet de conserver ces combustibles dans de bonnes conditions.
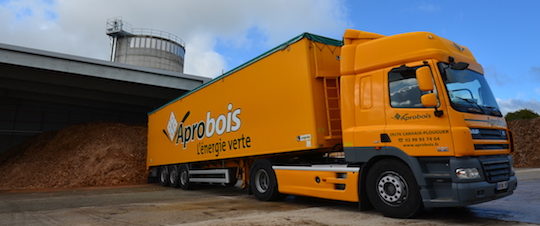
Livraison de combustible en provenance de la scierie de Carhaix, photo Frédéric Douard
Les plaquettes et les sciures issues des deux lignes de sciage sont quant à elles désormais destinées à la production de granulés de bois sur le site de Rostrenen.
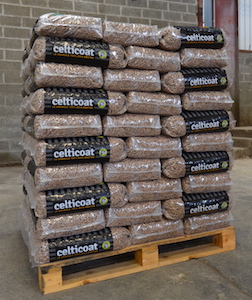
Granulés Celticoat, photo Frédéric Douard
L’usine Celticoat est une succursale à part entière d’Aprobois et du côté marchés, les granulés sont commercialisés via trois circuits :
- Les granulés ensachés sous la marque Celticoat (bois celte en breton) vers les circuits de distribution indépendants (poêliers, chauffagistes, distributeurs d’énergie),
- Les granulés ensachés sous la marque Koadenn (petits morceaux de bois en breton) vers la grande distribution,
- Les granulés en vrac ou en big-bags vers les distributeurs locaux équipés de camions souffleurs notamment.
Dans le prévisionnel de l’entreprise, les granulés ensachés devraient représenter les deux tiers du marché et l’ensemble de la production est d’ores et déjà certifiée Din+.
Celticoat, usine de taille intermédiaire à la pointe de la technique
La recherche d’un site pour y installer l’unité de granulation, celui de la scierie ne suffisant pas, a mobilisé Désiré Mahé dès 2013. Le choix s’est porté sur un ancien site industriel de 5 ha, avec 5 000 m² de bâtiments existants, à proximité de la route nationale 164 qui parcourt le centre de la Bretagne depuis Rennes.
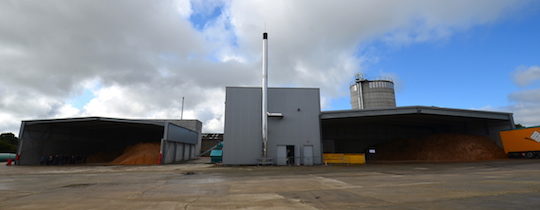
Depuis la gauche le stockage de matière humide, la chaufferie, le stockage de combustible et derrière le silo à matière sèche, photo Frédéric Douard
L’usine a été dimensionnée pour une production de 25 000 tonnes de granulés par an, avec un objectif à 15 000 tonnes dès la première année. À terme, pour alimenter la nouvelle unité en bois, combustible et matière première, la scierie de Carhaix ne suffira plus et un complément est envisagé chez d’autres scieurs des environs.
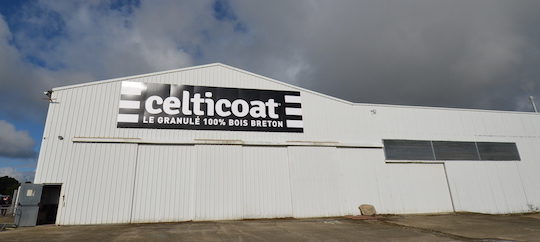
Le bâtiment de stockage des palettes de granulés de Celticoat, photo Frédéric Douard
Les investissements se répartissent en 2,2 M€ pour la chaufferie et 4,8 M€ pour l’usine de granulation. Le projet a été réalisé en un temps record de douze mois entre le premier coup de pioche et la mise en service intervenue en juillet 2017. Le module de granulation a par exemple été installé en seulement trois jours !
L’usine se compose des éléments suivants | |
---|---|
Un hangar neuf de 800 m² pour stocker le bois combustible, dont un silo actif réalisé par Polytechnik pour l’alimentation de la chaudière.
![]() Le silo à combustible de la chaudière POLYTECHNIK, photo Frédéric Douard |
|
Une chaufferie neuve de 300 m² équipée d’une chaudière Polytechnik de 2,5 MW avec électrofiltre et condenseur de fumées Scheuch de 700 kW. Elle a été retenue en 2014 pour une aide du Fonds Chaleur.
![]() La chaufferie de Celticoat et son hangar à combustible, photo Frédéric Douard |
|
Un hangar neuf de 800 m³ pour stocker la matière à granuler, dont un silo actif réalisé par Knoblinger pour l’alimentation de la ligne de broyage humide.
![]() Patrick Magne dans le stockage de matière humide de Celticoat, photo Frédéric Douard |
|
Une ligne de broyage de la matière première humide Knoblinger dans un local neuf, attenant du hangar de stockage et équipée d’un broyeur à marteaux Zesor.
![]() Le broyeur humide ZESOR à Rostrenen, photo Frédéric Douard |
|
Un séchoir à basse température Stela Laxhuber de 2,5 tonnes d’évaporation par heure.
![]() La ligne de séchage STELA-VBI, avec à droite le convoyeur provenant du broyeur et à gauche le silo à sciure sèche et à gauche le silo de matière séchée réalisé par Cousté, photo Frédéric Douard |
|
Un silo vertical en béton Wolf de 1 500 m³ (12 m de diamètre et 23 m de haut) pour stocker la matière sèche avant affinage et granulation. Il est équipé d’un filtre à poussières Scheuch et d’évents anti-explosion.
![]() Le silo à sciure sèche Cousté – WOLF avec son filtre à poussières SCHEUCH, photo Frédéric Douard |
|
Un hangar existant de 1 000 m² pour héberger les postes de granulation, l’ensachage, la palettisation, le houssage des palettes et le laboratoire.
![]() Four du laboratoire pour mesurer le taux de cendres des granulés, photo Frédéric Douard |
|
Un module d’affinage et de granulation Knoblinger de 5 tonnes/heure de capacité.
![]() Le Pellets Cube KNOBLINGER chez Celticoat, photo Frédéric Douard |
|
Un silo vertical en métal Privé de 1 500 m³ pour stocker les granulés en vrac avant ensachage. Il est équipé d’un portique avec boisseau de chargement pour les camions souffleurs ou à benne.
![]() Le silo PRIVE avec son boisseau de chargement des camions, photo Frédéric Douard |
|
Une ligne d’ensachage, palettisation et houssage Boga, suivie et mise en service par France Biomasse.
![]() La ligne d’ensachage et de palettisation BOGA chez Celticoat, photo Frédéric Douard |
|
Plusieurs hangars existants et accolés sur 4 000 m² pour stocker les palettes de sacs.
![]() Stock de granulés marqués Koadenn pour le marché des grandes surfaces, photo Frédéric Douard |
Une chaufferie de dernière génération avec condensation des fumées
Le choix du chaudiériste s’est porté vers un constructeur capable de garantir une combustion parfaite avec un large spectre de combustibles mélangés : plaquettes, écorces, sciures, copeaux voire granulés impropres. Suite à une consultation internationale, les critères de choix ont privilégié un constructeur historique en Autriche, l’entreprise Polytechnik, implantée en France depuis de nombreuses années.
Polytechnik a ainsi fourni les équipements de convoyage du combustible du silo à la chaudière, et bien entendu le générateur jusqu’au bac à cendres.
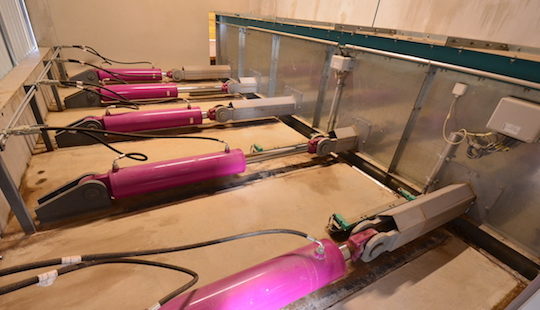
Le local des vérins extracteurs de combustible POLYTECHNIK pour l’alimentation de la chaudière, photo Frédéric Douard
Pour l’alimentation en bois, Polytechnik a privilégié un système entièrement hydraulique, de l’extraction du silo au convoyage dans la chaudière. L’introduction dans le foyer se fait par le bas, un système robuste, parfaitement étanche et donc sans risque de remontée de feu.
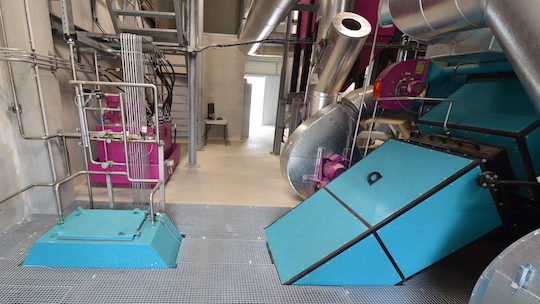
L’introduction du bois dans la chaudière POLYTECHNIK se fait pas un système hydraulique robuste et parfaitement étanche, photo Frédéric Douard
La combustion est réalisée sur à un foyer à grille mobile largement dimensionné en surface et équipé d’un préchauffage de l’air primaire pour accepter des humidités élevées.
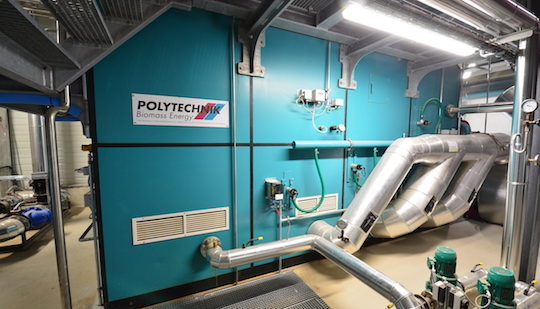
Le foyer POLYTECHNIK a été conçu d’origine avec recyclage de gaz de combustion dans le foyer ici visible à droite de la chaudière, photo Frédéric Douard
L’air secondaire est quant à lui prélevé sous le toit de la chaufferie pour y récupérer les calories perdues. Le foyer a été équipé d’emblée d’un recyclage des gaz de combustion permettant à la fois de bien contrôler la température de flamme, et donc de préserver la chaudière, et de maîtriser les émissions d’oxydes d’azote.
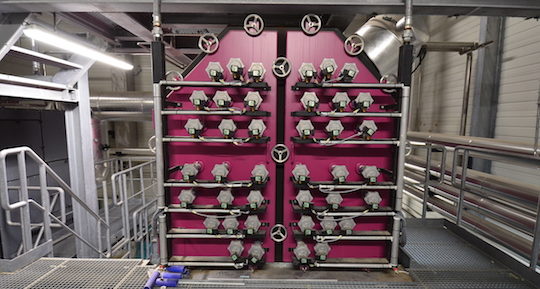
La partie échangeur thermique de la chaudière POLYTECHNIK avec ses ramoneurs pneumatiques, photo Frédéric Douard
Pour le traitement des particules fines, la chaudière est équipée d’un séparateur cyclonique Polytechnik qui abat le taux de grosses particules (PM10) et d’un électrofiltre Scheuch pour abattre le taux de fines particules (PM<2,5) à hauteur de moins de 45 mg/Nm³ à 6 % d’oxygène tel que demandé dans le dossier BCIAT.
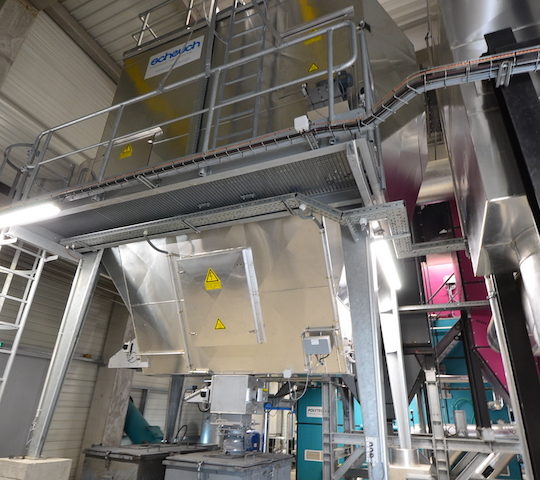
L’électrofiltre Scheuch, photo Frédéric Douard
Et comme l’énergie est destinée à alimenter un séchoir à basse température, avec des retours de fluide à très basse température vers la chaudière, Polytechnik a préconisé d’adjoindre un condenseur Scheuch qui permet de récupérer 700 kW supplémentaires sur les fumées ici très humides.
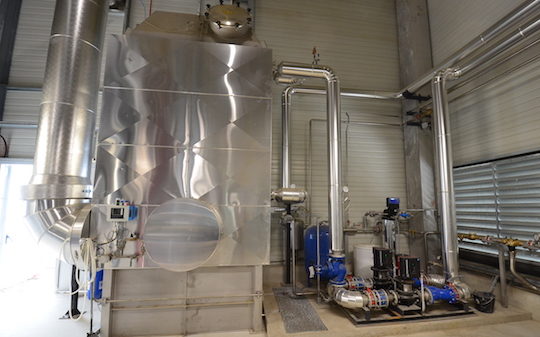
Le condenseur de fumées SCHEUCH fait gagner 700 kW de puissance à la chaufferie, photo FD
Les atouts du condenseur Scheuch | |
---|---|
Un rendement élevé, grâce au transfert direct de chaleur des fumées vers la boucle du sécheur à bande | |
Une consommation électrique induite très basse grâce aux pertes de charge du système limitées | |
Des coûts d’exploitation faibles | |
Un effet auto-nettoyant des tubes limitant le fonctionnement de la pompe de rinçage | |
De grandes portes pour faciliter les inspections | |
Une construction compacte | |
Une bonne tenue mécanique via l’utilisation d’acier INOX de nuance élevée |
Un sécheur à bande à basse température
Le séchoir Stela de type BTL 1/3000-16 a été conseillé et fourni par Vincent Bleesz des Ets VBI à Barr en Alsace agent commercial de STELA. Il a été entièrement réalisé en acier inox et permet de ramener la matière première réduite en sciure de 50 à 10 % d’humidité en moins de 30 minutes. Sa capacité lui permet de passer 5,6 tonnes de matière humide à l’heure et de produire 3,1 tonnes de matière séchée à l’heure.
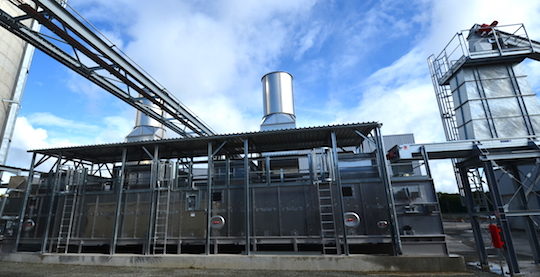
Le séchoir à bande STELA chez Aprobois, photo Frédéric Douard
Le séchoir est assemblé avec des vis et le montage ne nécessite donc aucun point de soudure. Il peut être modifié à tout moment et notamment être rallongé pour augmenter sa capacité.
La bande transporteuse est en plastique avec des perforations étudiées pour un séchage maximal et un dégagement minimal de poussière. La température de travail est régulée en permanence. La chaleur est transmise par des échangeurs à eau à lamelles en alliage d’aluminium, faciles à nettoyer.
Caractéristiques principales du séchoir Stela | |
---|---|
Dispositif de retournement de produit pour une humidité finale homogène et une aération du produit tout en économisant de l’énergie | |
Mécanique et électronique de guidage du tapis | |
Système Multivent avec plusieurs ventilateurs radiaux à couplage direct pour une distribution d’air continue avec pertes de pression et émissions de bruit minimales | |
Garantie d’émission de poussière à moins de 10 mg/Nm³ | |
Grandes portes pour une maintenance facile et corps de séchoir isolé | |
Construction fermée permettant un fonctionnement à l’extérieur jusqu’à -40 °C |
Le PelletsCUBE de Celticoat, une première mondiale
Le PelletsCUBE est une unité de granulation modulaire préfabriquée construite par le constructeur autrichien Knoblinger. Le Pellets Cube installé à Rostrenen est la toute première réalisation de ce produit par Knoblinger dans le monde, car l’entreprise était jusque-là habituée à réaliser des installations sur mesure.
C’est Patrick Magne, représentation de la société suisse ZM Technique, concepteur et installateur d’usines de granulation de bois modulaires clé en main, mais aussi représentant de matériel de scierie, qui a présenté l’idée du CUBE à Désiré. Patrick ayant en effet déjà fourni à Aprobois sa dernière ligne de sciage ultra-moderne, une relation de confiance s’est établie avec Désiré, très satisfait de cette installation et du suivi assuré par Patrick.
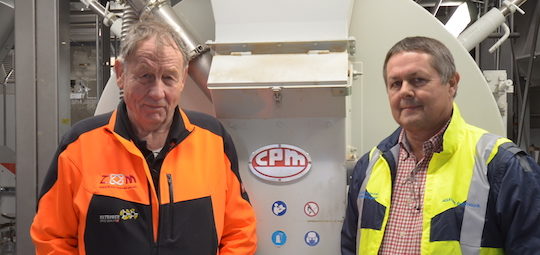
Anton Zimmerman à gauche, fondateur de ZM Technik, et Patrick Magne, représentant pour la France de ZM et Knoblinger, photo Frédéric Douard
Pour le projet de granulation, Patrick a travaillé avec Anton Zimmermann, le fondateur de ZM Technique, une entreprise qui a réalisé de nombreuses unités modulaires de granulation en Suisse et en France depuis 10 ans. Et pour ce projet, Anton et Patrick ont fait appel à Knoblinger en lui demandant de réaliser son premier Pellets Cube en Bretagne.
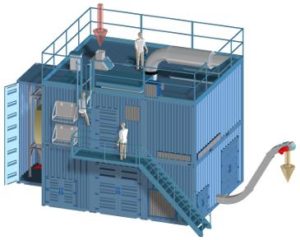
Le PelletsCube peut être placé indifféremment en intérieur ou extérieur
Le PelletsCUBE peut être indifféremment positionné à l’intérieur ou à l’extérieur d’un bâtiment. L’unité est préalablement et entièrement testée et éprouvée en usine. Les capacités de production disponibles sont de 2,5, 4 et 5 tonnes par heure.
Le PelletsCUBE d’Aprobois est constitué de six conteneurs préfabriqués, arrivés sur six camions d’Autriche après un périple de 1 500 km. Haut de 5,8 mètres, sa mise en place n’a nécessité que la préparation d’un socle en béton de 7,32 x 6 mètres et d’une alimentation électrique. L’unité intégrait déjà à son arrivée la commande complète de production, l’installation électrique, l’alimentation en air comprimé, les groupes de refroidissement et les dispositifs de sécurité.
L’ensemble est conçu pour apporter la plus grande facilité possible de conduite, d’entretien et de maintenance avec accès facile à tous les organes dont notamment les pièces d’usure comme la matrice de granulation, les rouleaux de compression ou le filtre à huile qui est accessible depuis le toit.
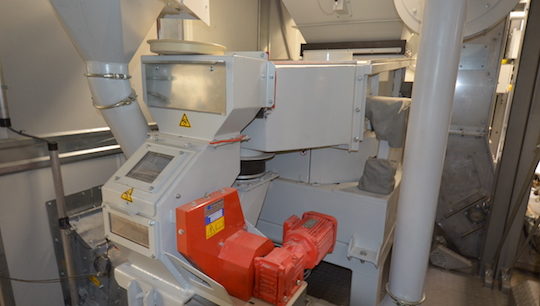
Le refroidisseur et le calibreur de granulés KNOBLINGER dans le niveau 1 du Pellets Cube, photo Frédéric Douard
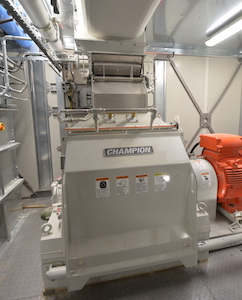
Broyeur affineur CHAMPION CPM pour la matière première sèche à granuler, photo Frédéric Douard
Au niveau 1 (trois conteneurs juxtaposés), on trouve une presse CPM de 5 tonnes/heure avec refroidissement à huile, et le tamis à granulés, le système GreCon, les armoires de distribution électrique.
Le transport et le refroidissement des granulés ont été conçus pour ne pas abîmer le produit et pour éviter tout risque d’explosion. La taille des granulés est garantie par un calibreur très spécial à rainures de conception Knoblinger.
Au niveau 2 (les trois autres conteneurs), on trouve un broyeur Champion (CPM), l’aspiration des poussières d’affinage et la trémie d’alimentation de la presse, le refroidisseur avec son filtre.
L’ensemble des organes en mouvement ou étant parcourus par de la matière sèche (broyeur sec Champion, convoyeurs, refroidisseur) y sont protégés contre l’explosion et l’incendie par l’entreprise GreCon.
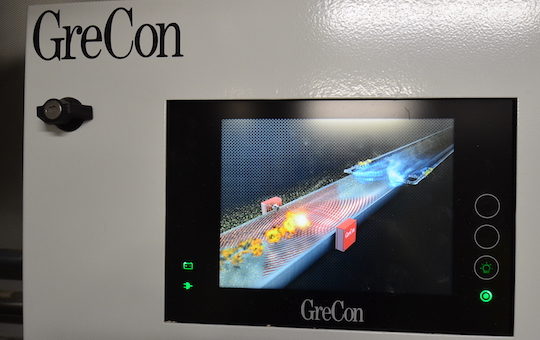
GreCon protège la zone ATEX de l’installation contre les risques d’explosion et d’incendie, photo Frédéric Douard
Des organes de régulation de la granulation d’une très grande précision
Les deux éléments fondamentaux de régulation de la qualité des granulés sont l’humidité et la masse volumique de la matière entrante dans la presse : leurs valeurs doivent être très précises et très régulières.
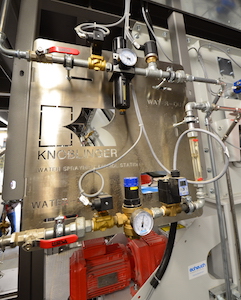
Le système de régulation de l’humidité de la matière à granuler dans le PelletsCube, photo Frédéric Douard
Dans le PelletsCUBE, la régulation de l’humidité est assurée par des capteurs de capacité à haute fréquence qui mesurent en continue le flux de matière à granuler. Ces capteurs en céramique, fournis par la société ACO, émettent des fréquences de 27 000 Hz et fournissent des valeurs précises à +/- 0,1 % dans toute la gamme des humidités possibles. Ces performances sont garanties dans un champ de températures variant de 4 à 70 °C. Ces mesures vont ensuite commander l’ajout d’eau pour corriger une humidité qui doit par défaut être trop faible au sortir de l’affineur.
La régulation de la masse volumique est assurée par une vis de dosage qui compacte la matière jusqu’à la valeur souhaitée, ceci compensant les variations du produit en provenance du broyeur. La masse volumique est mesurée en continue et compensée en permanence par l’action régulée de la vis. Pour des raisons élémentaires de physique, ce compactage n’est pas réalisé directement par la vis d’introduction, mais par une vis de dérivation placée dans un canal de chute de la matière, et qui restitue la matière préparée dans le processus normal d’introduction. La régularité de la masse volumique entrante permet d’une part d’assurer une mesure d’humidité ultra-précise et de toujours fournir à la presse la même quantité de matière sèche.
Contacts pour en savoir plus :
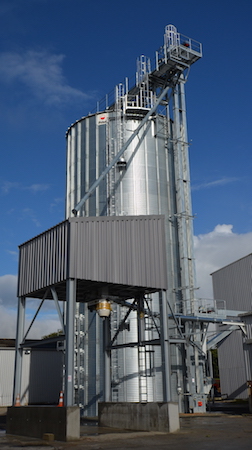
Le silo PRIVE pour le stockage des granulés en vrac chez Celticoat, photo Frédéric Douard
- Aprobois-Celticoat : Karine et Désiré Mahé ZAE de Kervoasdoué – 29270 Carhaix-Plouguer – +33 298 93 74 04 – contact@aprobois.fr – www.aprobois.fr
- La chaudière : Ets Polytechnick – 27190 Portes – Olivier Jacky – o.jacky@polytechnik.fr – +33 621 98 46 05 – www.polytechnik.fr
- L’électrofiltre, le condenseur de fumée, le filtre à manches en toiture de silos, les écluses rotatives : Ets Scheuch – Abdelaziz Berkoune – a.berkoune@wanadoo.fr – www.scheuch.com
- La cheminée : Beirens – 36500 Buzançais – www.beirens.fr
- La ligne de broyage humide : ZM & Knoblinger – Patrick Magne – magne-patrick@wanadoo.fr – + 33 610 46 29 57 – www.zmtechnik.ch – www.zesor.ch
- Le séchoir à bande : VBI – 67140 Barr – agent commercial STELA – Vincent Bleesz – +33 688 67 79 68 – vincent.bleesz@vbi-bois.fr – www.vbi-bois.fr – www.stela.de
Le silo à matière sèche : Cousté – 22130 Plancoët – www.couste.com - Le module de granulation : ZM & Knoblinger – Patrick Magne – magne-patrick@wanadoo.fr – + 33 610 46 29 57 – www.zmtechnik.ch – www.knoblinger.com
- La mesure en continue de l’humidité et de la masse volumique à l’entrée de la presse : www.acoweb.de
- La presse à granuler et le broyeur de bois sec : CPM aux Pays-Bas – Paul Alderliefste – paul.alderliefste@cpmeurope.nl – www.cpmeurope.nl
- Le silo à granulés : Ets Privé 51000 Châlons-en-Champagne – www.prive.fr
- La sécurité anti-incendie : GreCon – 67960 Entzheim – Yannick Provo +33 628 56 10 75 – yannick.provo@grecon.fr – www.fagus-grecon.com
- L’ensachage, la palettisation et le houssage : www.bogatecnica.com – www.pkt.it – www.bocedisrl.com – www.marfilpaletizadores.com
- Four à calcination pour mesure du taux de cendres : www.carbolite-gero.fr
Frédéric Douard, en reportage à Rostrenen
ℹ️ Le magazine Bioénergie International est disponible :
- Au détail
- Dans le cadre d'un abonnement
Bonjour
Super article !
BRAVO