Le Gaec Schneider resigne avec Tedom-Schnell pour la cogénération biogaz et huile de colza
Article paru dans le Bioénergie International n°69 de novembre 2020
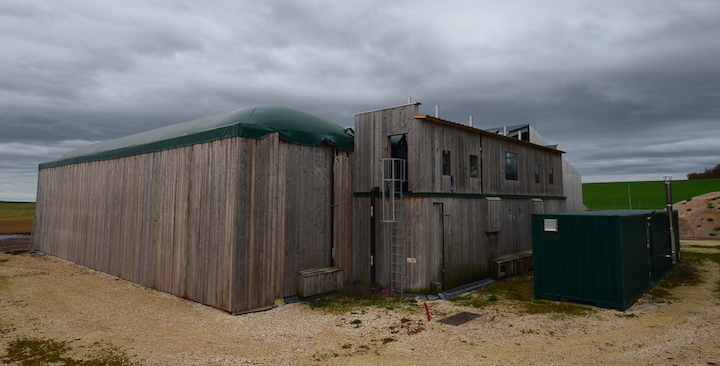
Les digesteurs du Gaec Schneider vue par la partie gestion des flux, photo Frédéric Douard

La chaufferie biomasse de Valduc, photo ADEME
La production d’énergie renouvelable est une histoire de famille chez les Schneider. Déjà en 2006, le grand-père Jacques et le père Charles avaient mis en service une chaudière à bois et paille de 6 MW au sein de la société Agro Énergie pour chauffer le centre de recherche du Commissariat à l’énergie atomique de Valduc, situé près de chez eux à Salives en Côte-d’Or (Voir la fiche de ce projet). Parallèlement, ils avaient équipé plusieurs toits en photovoltaïque. À peine dix ans plus tard, Charles relançait un nouveau projet de bioénergie agricole avec son fils Victor : la première unité de méthanisation en voie sèche discontinue de Bourgogne-Franche-Comté.
Petit historique
C’est pour poursuivre la diversification de son activité agricole vers l’énergie, que la famille Schneider a pensé ce projet, et en partie en relation avec le premier projet de chaufferie. Car parfois confronté aux questions d’humidité du bois pour leur chaufferie, les énergiculteurs ont pensé sécher du bois déchiqueté à partir d’une unité de cogénération au biogaz.
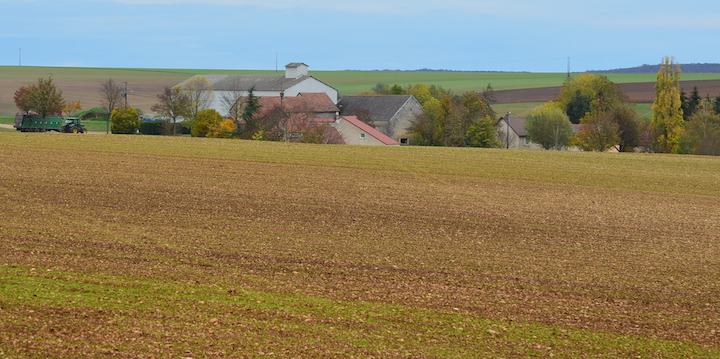
La ferme du Gaec Schneider à Salives, photo Frédéric Douard
Dès juin 2013, une étude de faisabilité était réalisée en voie sèche pour mettre à profit leur principale ressource, du fumier pailleux bovin. Fin 2013, le projet est dimensionné par l’entreprise Méthajade avec qui le Gaec Schneider signe en début d’année 2014 pour un projet à 1 640 000 €. Puis survient la cessation de paiement de Méthajade, puis son rachat par Naskéo en avril 2014 et les travaux commencent dans la foulée. Les premiers digesteurs sont remplis en mai 2015 et en juin 2015 les premiers kWh sont vendus.
L’exploitation agricole
Le Gaec Schneider est une exploitation en polyculture – élevage sur 585 hectares et qui depuis 2012 pratique l’engraissement de 300 taurillons de Charolais et d’Aubrac. L’exploitation comporte également 55 vaches allaitantes au pré. Le Gaec emploie quatre salariés et Victor qui est responsable de l’atelier méthanisation.
Les cultures se répartissent entre blé, orge et colza pour la vente, plus 30 ha de maïs ensilage pour l’élevage et la méthanisation, ainsi que 35 ha de luzerne à foin pour les bêtes et 20 ha de CIVE d’hiver (Seigle) pour la méthanisation. Une soixantaine d’hectares en herbe accueillent les bovins en pâturage l’été.
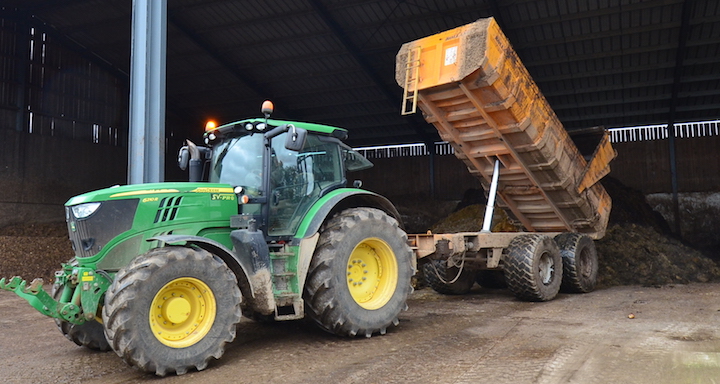
Livraison de fumier frais dans la fumière couverte de l’unité de méthanisation, photo Frédéric Douard
Les substrats utilisés en méthanisation étaient en 2020 : 4 000 tonnes de fumier de bovin du Gaec Schneider, 1 200 tonnes de fumier du Gaec voisin de l’Étang, 1 000 tonnes de matières stercoraires, 2 500 tonnes d’ensilage de maïs, de CIVE et de légumes divers, 500 tonnes de lisier bovin du Gaec de l’Étang et 700 tonnes de jus de cour, soit au total 9 900 tonnes par an.
La méthanisation
L’unité est composée de quatre digesteurs de 123 m² chargés à 3,5 mètres de hauteur et pouvant chacun contenir 300 tonnes de produits. Chaque digesteur est vidé à tour de rôle puis rempli par 150 tonnes de matières fraîches et 150 tonnes de digestat, afin de garantir la production de biogaz la plus constante possible.
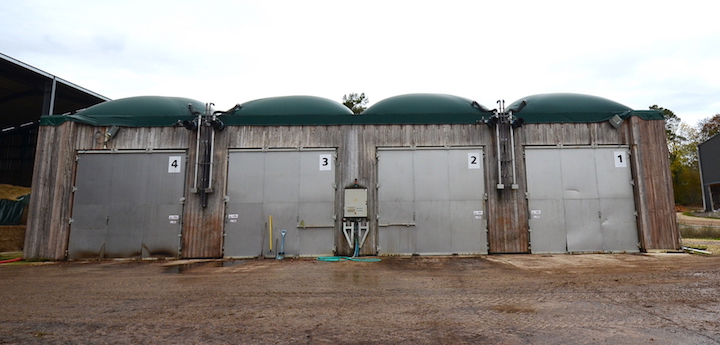
Les digesteurs du Gaec Schneider côté manutention des intrants, photo Frédéric Douard
Trois jours avant le chargement, les matières sont mélangées et broyées à l’aide d’un épandeur à fumier. Cela provoque une fermentation aérobie qui élève la température du tas parfois à plus de 50 °C. Ensuite une fois le digesteur chargé, les portes refermées, la fermentation anaérobie s’engage et la production de gaz commence. L’installation de cogénération maintient la température des digesteurs entre 38 et 42 °C. Les jus qui percolent des digesteurs sont récupérés, mélangés avec le lisier frais et les jus de cour, chauffées dans deux cuves de 50 m³, puis servent à arroser les tas selon une méthode précise.
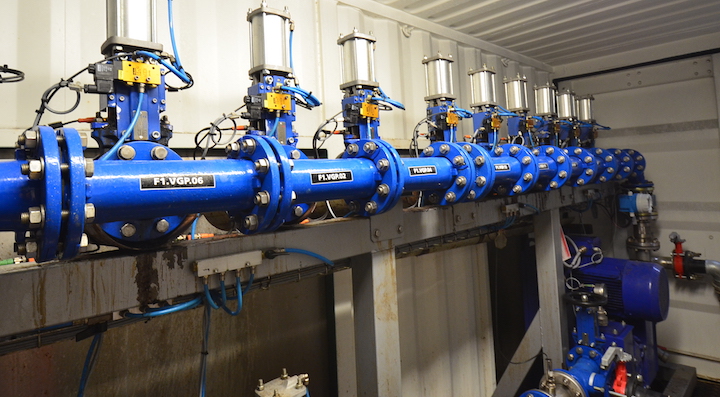
Les vannes de régulation de l’aspersion des digesteurs, photo Frédéric Douard
L’automate Naskéo régule en effet l’arrosage de manière à maintenir un taux d’humidité de 80 % durant la totalité du cycle, et n’injecte au maximum que 70 m³ d’eau par garage. Passé cette quantité, l’arrosage n’est permis que si du jus percole et ruisselle du digesteur. La quantité de percolât est mesurée par un débitmètre et ce n’est que cette même quantité qui peut être réinjectée.
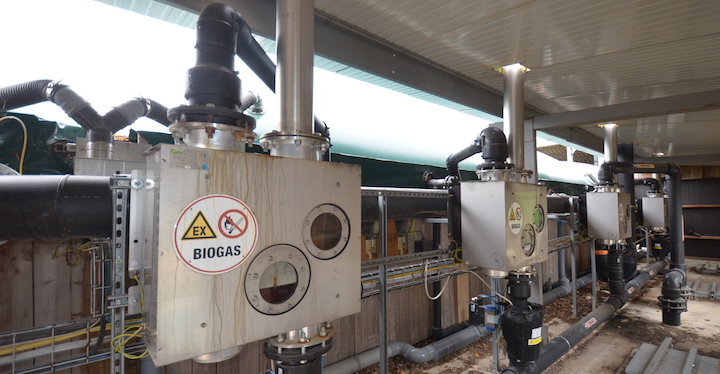
Les collecteurs de biogaz et dispositifs de sécurité sur les digesteurs, photo Frédéric Douard
Aujourd’hui Victor parvient à produire un biogaz riche de 57 à 58 % de méthane et en quantité suffisante pour lui permettre d’augmenter sa production électrique de 170 à 250 kW. Pour cela, il a agi sur deux paramètres. Premièrement, il a raccourci les cycles de digestion : de 56 jours, il les a ramenés à 28 jours. Ensuite, il a abandonné certains intrants peu méthanogènes au profit d’ensilage.
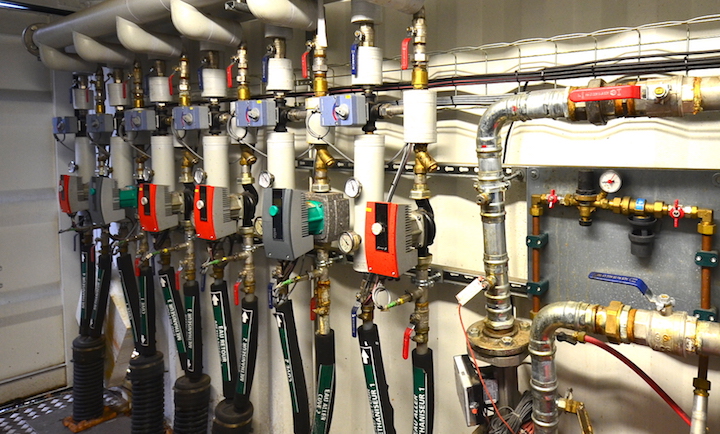
Les départs chaleur depuis l’un des modules de cogénération, photo Frédéric Douard
Victor Schneider, photo Frédéric Douard
Et Victor de préciser : « Juste avec du fumier, ce n’est pas très rentable, il faut donner un peu plus d’énergie aux bactéries pour un résultat bien satisfaisant. Alors, certes, tout le potentiel méthanogène n’est pas exploité et il faut plus d’intrants, mais l’outil produit presque 50 % d’énergie en plus et il est donc bien plus rentabilisé. Et puis, le digestat est plus riche en matière organique, ce qui est plutôt bien pour les sols. »
Le vidage et remplissage d’un digesteur demande cinq heures de travail. Le vidage consiste à ouvrir la porte après inertage, à enlever la pré-porte, à sortir le digestat et à nettoyer les caniveaux de drainage et les rampes d’aspersion à haute pression. Le remplissage demande à pailler généreusement la surface des caniveaux d’écoulement du percolât pour éviter leur colmatage pendant le cycle, à charger les matières et à refermer la porte après positionnement de la pré-porte de protection.
Pour compenser le déficit de fumier d’été, de par le pâturage, les stabulations ne sont pas totalement curées l’hiver et servent de stockage pour l’été. Notons aussi que l’échange de fumier contre digestat avec le Gaec voisin, inclut le curage et le transport par le Gaec Schneider. Les 8 000 tonnes de digestat méthanisation sont épandues des GAEC Schneider et de l’Étang à raison de 12 tonnes par ha et par an en moyenne.
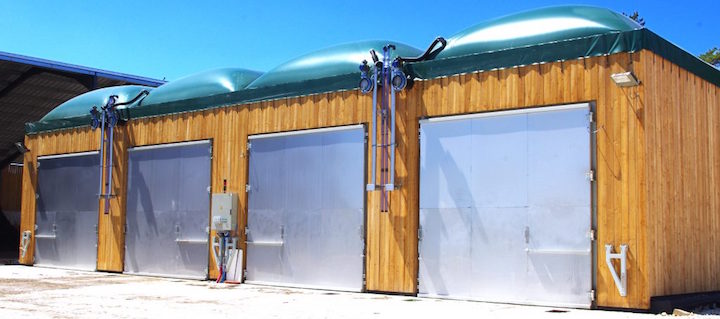
L’unité de méthanisation de Salives à sa mise en service, photo Naskeo
Les unités de méthanisation en voie sèche discontinue sont adaptées à des tonnages compris entre 5 000 et 30 000 tonnes/an et présentent de nombreux avantages : faible dépendance aux équipements mécaniques, aucune sensibilité aux indésirables, consommation de liquide réduite, coûts de maintenance réduits, faible consommation énergétique, facilité d’exploitation par la conduite en lots, compartimentation des risques due au nombre de digesteurs et digestat épandable sans traitement spécifique.
Une cogénération plus souple avec deux carburants
Depuis la mise en service de l’installation, le biogaz du Gaec a été valorisé dans un moteur générant 170 kW électriques. Le tarif de vente est aujourd’hui de 21,577 c€/kWh avec la prime aux effluents d’élevages.
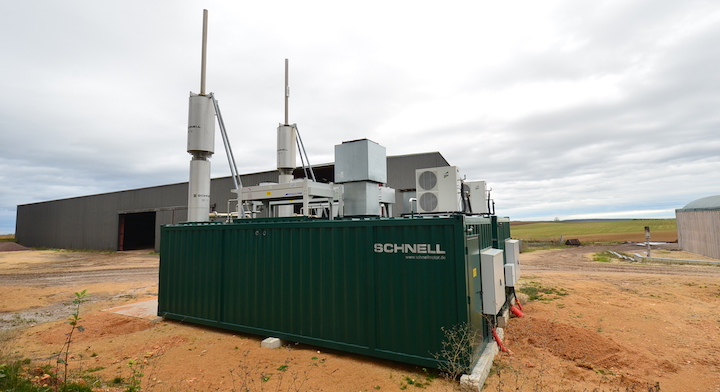
Les deux modules de cogénération Tedom-Schnell au Geac Schneider, photo Frédéric Douard
La production électrique annuelle était de 1,2 GWhé. La chaleur disponible était valorisée dans le processus pour environ 125 MWh/an et le reste pour le séchage de bois-énergie pour le chauffage de Valduc jusqu’au printemps 2018. Par contre à cette date, le centre de recherche, n’ayant pas reconduit le contrat d’achat de chaleur à la fin du contrat de douze ans, et ce débouché s’est tari. Victor travaille aujourd’hui à relancer une activité de séchage à façon de bois de chauffage avec un producteur local, et de continuer à proposer le séchage à façon de bois déchiqueté.
En 2020, après avoir adapté son processus de méthanisation pour produire plus de biogaz, Victor a pu modifier son contrat de vente par un avenant pour une puissance d’injection de 250 kWé. En août 2020, il a donc mis en service un deuxième moteur de cette puissance à côté du premier qui venait d’avoir 45 000 heures. Le premier moteur qui n’est pas hors service est conservé en secours et fonctionne durant les maintenances de l’autre.
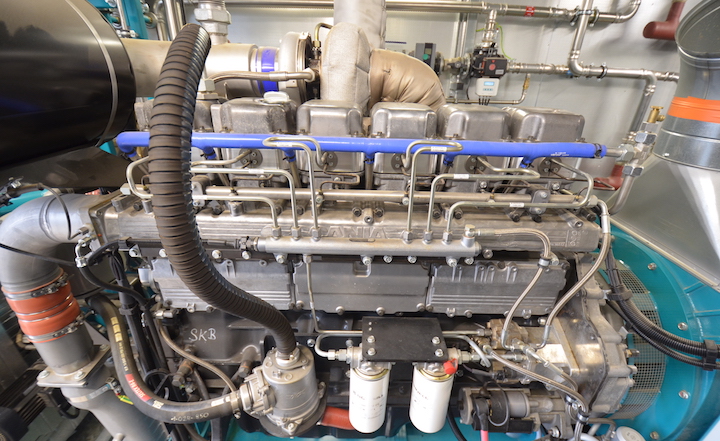
Gros plan sur le moteur Scania de la nouvelle cogénératrice Tedom-Schnell du Gaec Schneider, photo Frédéric Douard
La technologie retenue par le Gaec Schneider auprès du motoriste Tedom-Schnell est un moteur à injection pilote. Sur le principe de certains moteurs à gaz qui fonctionnement avec un allumage au fioul, ici l’allumage est réalisé à l’huile de colza pressée à la ferme.
Le principe de ces moteurs dit dual fuel en anglais, à deux carburants, est l’injection d’une petite quantité de carburant liquide (2 à 5 % de l’énergie consommée), afin d’enflammer le mélange air & biogaz. Ce type de moteur est un peu plus coûteux que les moteurs à gaz pur, mais affiche un meilleur rendement électrique (40-42 % en moyenne), surtout pour les petites puissances. Ce type d’allumage permet en effet d’augmenter les pressions de combustion et donc le rendement.
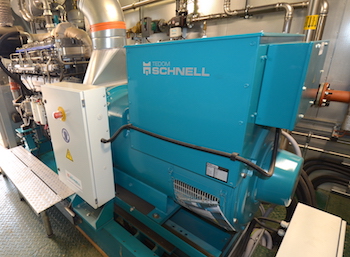
Le nouveau moteur de cogénération dual fuel Tedom-Schnell de 265 kW du Gaec Schneider, photo Frédéric Douard
Dans le premier moteur du Gaec, la combustion du biogaz était complétée par 2,5 litres d’huile de colza par heure. Outre leur meilleur rendement, les moteurs dual fuel présentent d’autres avantages comme l’absence de problèmes de démarrage car pas de bougies, une meilleure durabilité et une meilleure stabilité de la puissance, car le combustible pilote, ici l’huile de colza, complète automatiquement les déficits éventuels de biogaz, et le moteur peut même dans l’absolu fonctionner momentanément sans biogaz, ce qui peut être utile en cas d’incident ou pour chauffer les digesteurs lors d’une mise ou remise en service.
En résumé, les moteurs dual fuel apportent du confort aux conditions d’exploitation et comme l’a illustré Victor avec son deuxième moteur, ceux qui y goûtent, ne souhaitent plus s’en passer !
La production d’huile
Le Gaec Schneider a commencé la production d’huile avec son propre colza dès 2015 pour alimenter son moteur, à raison de 15 tonnes par an. Il a pour cela acheté une première presse à huile et les filtres qui vont avec. Puis, dès 2017, il a aussi fourni 15 tonnes d’huile par an au Gaec Asdrubal situé non loin de là, pour une unité de méthanisation très semblable. Une deuxième presse à huile a alors été acquise.
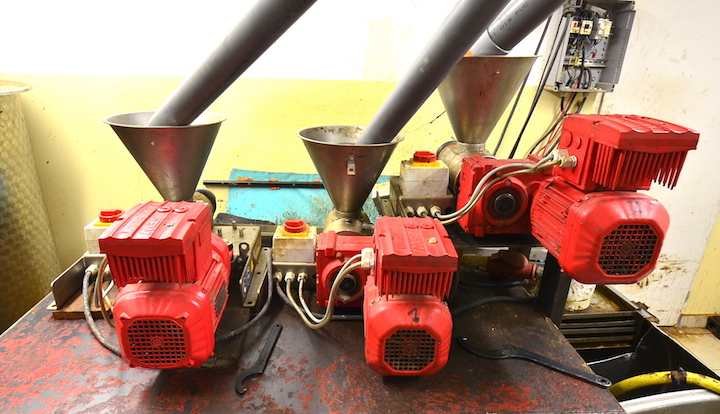
Les trois presses à huile du Gaec Schneider, photo Frédéric Douard
Et en 2020, le Gaec a produit 100 tonnes d’huile, sur 110 ha de culture, avec cette fois trois presses. Avec cela, il alimente les moteurs des deux Gaec et a aussi entre temps trouvé un débouché agro-alimentaire pour l’huile. Les tourteaux sont quant à eux valorisés en alimentation pour le troupeau.
Un moteur dual-fuel à injection pilote en 2021 chez Tedom-Schnell
Fort de son expérience, Tedom-Schnell annonce qu’il va commercialiser en 2021 un nouveau cogénérateur sur base Scania 12,7 litres à injection pilote développant jusqu’à 265 kWé.
Ce cogénérateur sera basé sur la nouvelle série de moteurs Scania disposant de la technologie injecteur-pompe extrêmement robuste, d’un bon rendement électrique, et d’un haut rendement thermique. Les échanges moteur seront moins chers qu’avec l’ancienne série Scania. Sa consommation de biogaz sera de 101 m³/h avec 60 % de méthane ou de 121 m³/h avec 50 % de méthane. La consommation de combustible pilote reste la même à 2,5 kg/h.
Retour d’expérience
Lors de notre visite, Victor insiste pour nous dire que, « comme dans tous les élevages en quelque sorte, la méthanisation n’est pas un long fleuve tranquille, qu’il faut sans cesse rester attentif, qu’il faut souvent réapprécier ses procédures et qu’il survient régulièrement des imprévus, et ça il ne faut pas le cacher ».
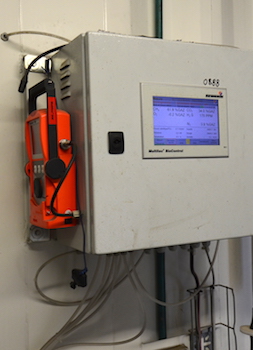
Le terminal de mesure du biogaz du Multitec BioControl de chez Sewerin reposé sur sa base fixe, photo Frédéric Douard
Le plus gros imprévu qu’ait connu le Gaec Schneider est un écartement du haut des parois externes à chaque bout du bloc de digesteurs en 2016, soit juste un an après la mise en service. Ce problème, qui a sur le moment généré des fuites et a fait perdre beaucoup de temps et d’énergie à Victor, a trouvé une solution amiable assurantielle auprès des deux constructeurs Wolf et Naskeo, alors que Naskeo venait tout juste de reprendre Méthajade. Dès lors, les murs extérieurs ont été renforcés et Victor est aujourd’hui parfaitement satisfait de son installation !
Contacts :
- Gaec Schneider : Victor Schneider / +33 380 756 286
- Méthanisation : info@naskeo.com / +33 157 213 470 – www.naskeo.com
- Cogénération : Bernhard Pfefferle - b.pfefferle@tedom-schnell.fr - www.tedom-schnell.de/fr/
- Presses à huile : www.anton-fries.de
Frédéric Douard, en reportage à Salives
ℹ️ Le magazine Bioénergie International est disponible :
- Au détail
- Dans le cadre d'un abonnement