Le lycée agricole d’Obernai enseigne la méthanisation en conditions réelles
Article paru dans le Bioénergie International n°44 de juin-juillet 2016
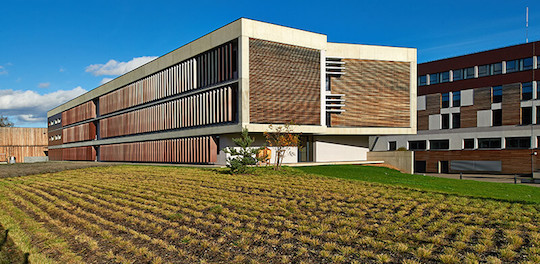
Le Lycée agricole d’Obernai, photo Seltz Constructions
L’EPLEFPA du Bas-Rhin (Lycée Agricole d’Obernai), en Alsace dispose d’une exploitation agricole et depuis début 2013 de son unité de méthanisation. Freddy Merkling, le directeur d’exploitation, travaillait depuis 2006 sur ce dernier projet car il voulait présenter un cas d’école exemplaire. Côté énergie renouvelable, l’exploitation exploite également une toiture photovoltaïque de 615 m² et 84 kWc sur le bâtiment d’élevage et l’EPLEFPA possède une chaudière à plaquettes de bois de 960 kW.
Une structure pédagogique qui se doit d’être rentable
L’exploitation agricole, adossée à l’EPLEFPA , fonctionne comme une entreprise, au sein d’un établissement public. Elle emploie trois salariés permanents et deux apprentis qui sont formés à la conduite d’une unité de méthanisation.
L’exploitation est composée de 65 ha de cultures (houblon bio, betterave et céréales), et d’un atelier d’engraissement de 204 taurillons. Outre son aspect pédagogique, l’exploitation se doit de trouver une rentabilité financière dans tout ce qu’elle entreprend.
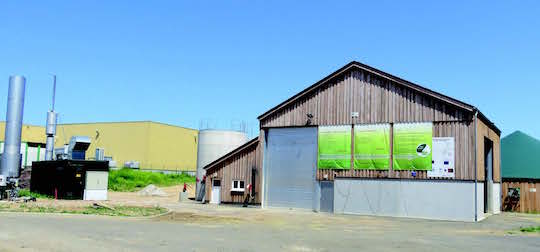
Expoitation agricole du Lycée d’Obernai, photo EPLEFPA du Bas-Rhin
Le fonctionnement de la ferme est aussi circulaire que possible, indique Freddy Merkling. Il améliore le processus global de son fonctionnement en privilégiant la production locale et en se détachant des fluctuations des approvisionnements. Les bovins sont nourris à base des cultures produites par l’exploitation (maïs ensilage, céréales) et de sous-produits achetés aux entreprises locales, (pulpes de betterave, corn-feed, okara), et de cultures avoisinantes (luzerne). Le lisier et les fumiers produits par les bovins sont récupérés et valorisés grâce à l’unité de méthanisation. Le biogaz est transformé sur le site en électricité et en chaleur. L’électricité est revendue et injectée dans le réseau du fournisseur local, Électricité de Strasbourg.
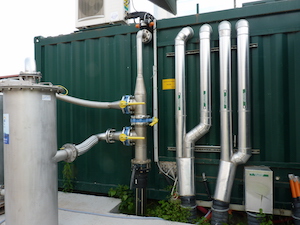
Arrivee de biogaz et départ réseau de chaleur du module de cogénération, photo François Bornschein
La chaleur est valorisée de trois façons : elle maintient les 39 degrés requis à l’intérieur du digesteur, elle permet d’hygiéniser certains intrants de l’unité, comme les déchets de cantines, et la plus grande partie est vendue au site industriel voisin, la charcuterie industrielle Stoeffler.
Pour terminer ce cercle vertueux, le plan d’épandage du digestat mobilise 500 ha chez des agriculteurs voisins, en substitution d’engrais chimiques et permet un retour d’azote pour les fermes spécialisées en productions végétales. Les revenus provenant de la vente d’électricité, de chaleur et le digestat une fois valorisé permettent une production agricole continue sans pression environnementale.
Quelques chiffres sur l’unité
Le digesteur de 1 500 m³ est alimenté par 6 000 tonnes de matières organiques dont 1 450 t de fumier, 700 t de lisier, 700 t de marc de raisin, 1500 t d’ensilage de cultures dérobées, 500 t de tontes de gazon, 500 t d’issues de tri de pommes de terre, 750 t de graisse de Best Food et divers. Le projet initial prévoyait la consommation de 8 000 t de matières entrantes. Le potentiel de 2000 t, non exploité, permet d’envisager un projet d’augmenter la puissance de l’installation. Ce projet est actuellement à l’étude.
L’installation de cogénération fournit 1 100 MWh de chaleur et 2 000 MWh d’électricité par an. La puissance initiale du cogénérateur Schnell dual-fuel était de 180 kWé, mais elle a rapidement été augmentée à 240 kWé maximum.
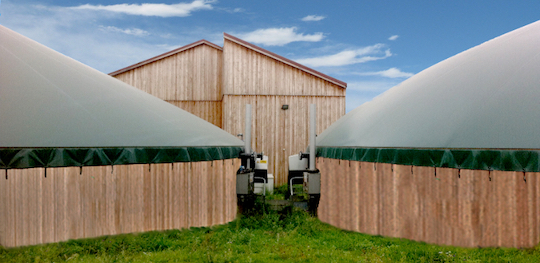
Les digesteurs du Lycée d’Obernai, photo Naskéo
L’investissement global a été de 2,2 millions d’€. Le site a bénéficié d’aides publiques octroyées par l’État, l’Union Européenne, la Ville d’Obernai et la Communauté de Communes du Pays de Sainte-Odile, à hauteur de 825 613 €. Les ventes d’électricité et de chaleur et la prestation de traitement de déchets engendrent des recettes à hauteur de 400 000 €/an.
La valorisation des 4 500 t de digestat représente également une économie sur les achats d’engrais agricoles de synthèse. La conception, le suivi et la mise en route du site ont été effectués par Naskéo Environnement.
Une unité de méthanisation discrète
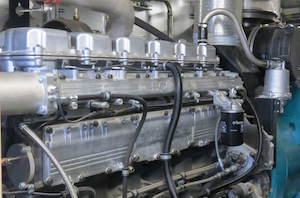
Le moteur de cogénération Schnell est placé dans un conteneur insonorisé
Avec son digesteur de 1500 m³ et son post-digesteur de 3300 m³, partiellement enterrés, avec une emprise au sol d’à peine 60 ares, l’installation ne dépasse aucun des bâtiments alentours en raison du plan d’urbanisme d’une part mais aussi pour limiter la consommation des surfaces agricoles de l’exploitation.
Le bâtiment de stockage et d’hygiénisation des déchets de catégorie 3, est un bâtiment fermé dont l’air est filtré afin d’éviter toute nuisance olfactive. L’installation de méthanisation a donc permis une nette amélioration de la situation antérieure.
Côté sonore, seul le fonctionnement 24h/24 du moteur pourrait être source de nuisance, mais le confinement en conteneur isolé réduit efficacement la pression acoustique : de 99dB(A) à l’intérieur du caisson moteur, il ne subsiste que 69dB(A) à 5m à l’extérieur.
Une alimentation du digesteur copiée de la zootechnie
Le ratio C/N correspond à la part de carbone sur l’azote dans la matière organique. Et la maîtrise de ce rapport fait partie des bases de l’agriculture, qu’il s’agisse d’engraisser des bovins de pratiquer des cultures ou d’épandre du lisier sur ses sols. C’est donc l’unité de base qu’utilise Freddy Merkling pour déterminer la ration envoyée quotidiennement dans le digesteur à partir des matières dont il dispose.
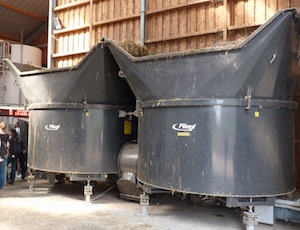
Les deux incorporateurs-melangeurs Fliegl, photo François Bornschein
Le site collecte en plus de ses propres lisiers, fumiers, pailles et résidus de pulpes de betteraves, des substrats d’autres exploitations comme des pommes de terre en fin de vie, et des déchets de l’industrie agroalimentaire comme les graisses de flottaison de son voisin Stoeffler et les déchets des restaurants et supermarchés des alentours.
Selon les saisons, ce mix doit être adapté afin de garder un rapport C/N équilibré et ne pas risquer un emballement de la biologie interne du digesteur, qui aurait un impact sur la quantité et la qualité du biogaz produit.
Les différentes matières solides sont introduites toutes les heures par l’intermédiaire de deux grands bols mélangeurs de marque Fliegl, le reste, en voie liquide, est géré automatiquement par les pompes au niveau de la cuve de l’hygiénisateur et de celle des lisiers. Deux agitateurs Suma maintiennent les éléments en suspension dans le digesteur.
La maintenance préventive, gage de performance
Partant du constat que lorsque le moteur de cogénération ne tourne pas, c’est toute la rentabilité du site qui en pâtit, Freddy Merkling a préféré prévenir plutôt que devoir guérir son installation. Ainsi, pour améliorer la production électrique de quelques heures supplémentaires par an, la vidange des 68 litres de lubrifiant du moteur n’est plus manuelle, mais se fait à l’aide une pompe électrique lors des deux arrêts annuels toutes les 3 600 heures, et l’ensemble des équipements critiques est assuré en bris de machines.
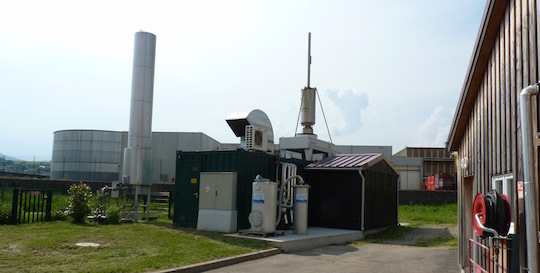
Le module de cogénération Schnell, photo François Bornschein
Le laboratoire du motoriste Schnell est chargé de l’analyse très poussée des huiles après chaque vidange pour identifier tout début d’usure anormale. L’installation dispose aussi d’un stock de toutes les pièces nécessaires pour parer à une panne de pompes, et parfois voire en double et même triple exemplaire.

L’échappement du cogénérateur Schnell avec récupération de chaleur, photo F. Bornschein
Pour faire souffrir le moins possible le moteur, le biogaz doit comporter le moins possible d’H2S. Pour cela le module de cogénération comporte des filtres à charbon actif. Mais c’est un consommable coûteux et il a été décidé de les neutraliser en ajoutant en amont de l’arrivée de biométhane un autre filtre, à base d’hydroxyde de fer, conçu par la société Ovive, et qui se fait sur la base d’une location de 60 mois. Les résultats sont concluants puisque en sortie de ce filtre la concentration d’H2S est proche voire égale à zéro. Ceci économise le poste charbon actif, dont le renouvellement est moins fréquent, sans compter les problèmes évités sur les injecteurs, pistons et segments du moteur.
Concernant les effets climatiques qui agissent sur les conditions d’exploitation, en été par exemple, le seigle sec présente la particularité de s’expanser dans le digesteur : pour l’éviter, le niveau de celui-ci est baissé préventivement de 30 cm afin que rien ne vienne obstruer les canalisations de biogaz en cas de débordement par les conduites de collecte situées en partie haute.
Autre sage précaution, la mesure régulière des ampérages des trois phases d’alimentation des moteurs des agitateurs : cela permet de déceler le niveau d’usure des pales qui ont une durée de vie limitée compte-tenu de l’abrasion avec les matières pâteuses en suspension dans le digesteur.
Enfin pour garder la mémoire de la résolution des différentes pannes ou incidents rencontrés, un cahier de procédures a été constitué.
C’est la somme de toutes ces précautions qui vaut aujourd’hui à cette installation de pouvoir afficher un taux de disponibilité de sa cogénération de 98% sur l’année 2015.
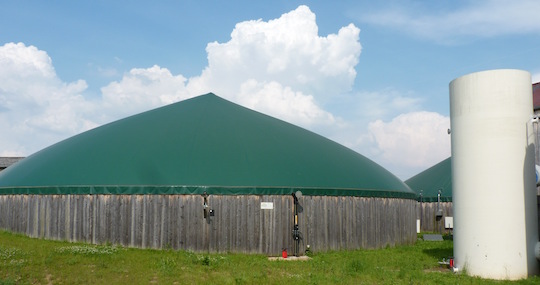
Le post-digesteur-enterrée Wolf-Systeme et cuve d’intrants liquides, photo François Bornschein
Le fonctionnement global étant désormais bien maîtrisé, et devant la fiabilité du motoriste, le projet d’un second moteur Schnell est envisagé, pour porter la production électrique à 480 kWé. Et cerise sur le gâteau, la génération suivante des moteurs Schnell ne serait plus dual-fuel, donc sans injection de gazole non routier GNR. Car le détail a son importance, mais la génération dual-fuel nécessitait un minimum de GNR, environ 2,5kg/h à Obernai afin d’assurer l’auto-inflammation du biogaz (méthane + CO2) et par la même occasion le graissage des injecteurs.
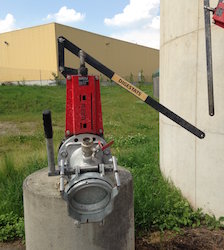
Vanne de vidange du digestats, photo-Biogaz Vallée
Contacts
- Lycée Agricole d’Obernai : Freddy Merkling – +33 388 49 99 49 – +33 6 08 92 74 61 – freddy.merkling@educagri.fr – www.eplea-obernai-erstein.epl67.fr
- Motoriste : Schnell, Pfefferle Bernhard – Tél.: +49 7520 9661-818 – Mobile : +33 625 35 15 20 – b.pfefferle@schnellmotor.fr – www.schnellmotor.de
- Ingéniérie : Naskeo, Marc Bauzet – marc.bauzet@naskeo.com – www.naskeo.com
- Incorporateur : Fliegl, Denis Houdart – denis.houdart@fliegl-france.com – www.fliegl-france.com
- Traitement H2S : Ovive, Audrey Constantin aconstantin@ovive.fr – www.ovive.fr
- Agitateurs : Suma Rührtechnik GmbH – www.suma.de
François Bornschein, en reportage à Obernai
ℹ️ Le magazine Bioénergie International est disponible :
- Au détail
- Dans le cadre d'un abonnement