TVME d’Hénin-Beaumont, valorisation unique de déchets ménagers résiduels en biométhane et CSR
Article paru dans le Bioénergie International n°53 de janvier-février 2018
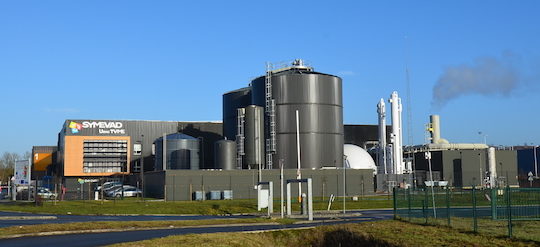
L’entrée de l’usine de TVME d’Hénin-Beaumont avec vue sur les deux digesteurs et la gazomètre à biogaz, photo Frédéric Douard
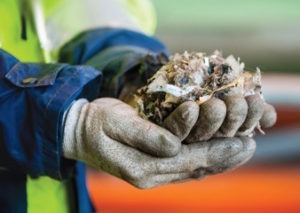
Echantillon de CSR, photo Tiru
À Hénin-Beaumont dans le Pas-de-Calais, une unité unique en France de tri et de valorisation des déchets non recyclables des particuliers fonctionne depuis plus de deux ans. Son originalité tient tout d’abord à son niveau particulièrement élevé de valorisation avec l’objectif de passer la part de déchets non valorisés à moins de 15% du tonnage entrant. Ensuite, outre la récupération des matériaux recyclables, le TVME (Tri Valorisation Matière et Energie) produit également deux combustibles : du Combustible Solide de Récupération (CSR) et du biométhane. Son originalité tient à la qualité des conditions de travail et à celle de ses émissions olfactives, infiniment réduites en comparaison avec bien d’autres centres de tri mécano-biologique (TMB).
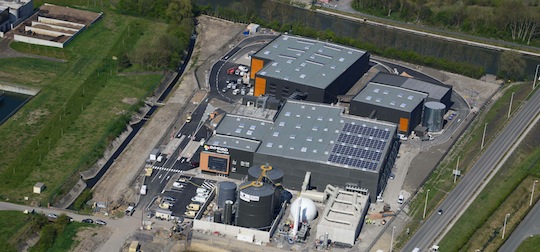
Vue globale du TVME d’Hénin-Beaumont, photo TIRU – ALTIMAGE
La deuxième installation de ce type dans le Monde
Cette unité, créée par le SYMEVAD, SYndicat Mixte d’Élimination et de Valorisation des Déchets, valorise les ordures ménagères résiduelles (OMR) de 325 000 habitants des Communautés d’Agglomération du Douaisis et d’Hénin-Carvin, ainsi que de la Communauté de Communes OSARTIS Marquion. La construction du TVME a duré d’octobre 2013 à avril 2015 et a été suivie d’une année de tests et de montée en régime des installations. L’unité a été inauguré le 9 décembre 2016.
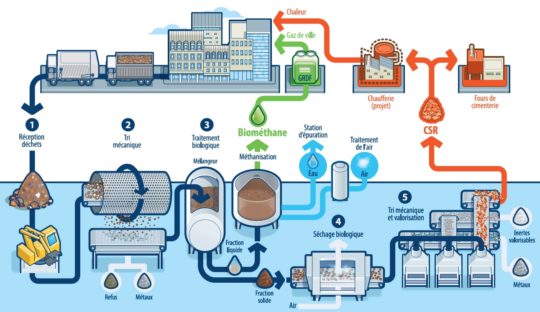
Schéma de principe du TVME d’Hénin-Beaumont, source Symevad. Cliquer sur le schéma pour l’agrandir.
Inspirée du procédé MYT (Maximum Yield Technology signifiant technologie à rendement maximal), développé en Allemagne par le Syndicat de traitement des déchets de Kahlenberg à Ringsheim, c’est aussi la première unité de valorisation en France à associer sur un même site la production de biométhane et de CSR.
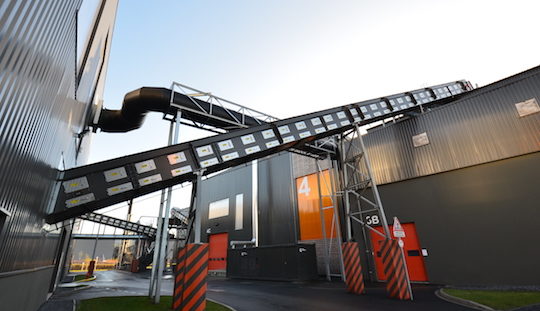
Chaque hall est numéroté selon l’ordre des modules du processus, photo Frédéric Douard
Le TVME a été dimensionné pour recevoir 100 000 tonnes par an dont 76 000 tonnes d’OMR, 20 000 tonnes d’encombrants et 4 000 tonnes de refus de tri de collecte sélective. Piloté par une équipe de 28 personnes, il permettra la production de 32 000 tonnes de CSR par an, soit 136 GWh valorisés en cimenterie, de 2,4 millions de m³/an de biométhane injectés dans le réseau GrDF soit 24 GWh, et évitera l’émission de 9 300 tonnes de CO2 par an.
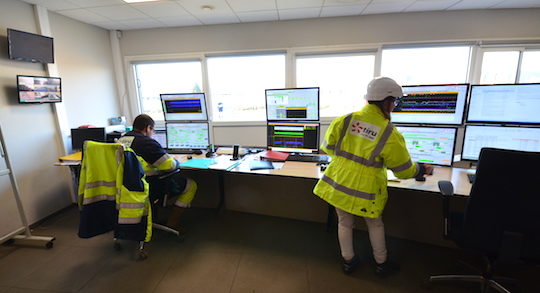
La salle de commandes du TVME, photo Frédéric Douard
L’investissement se monte à 54 millions € pour un coût de traitement objectif d’environ 100 €/tonne entrante. Sa conception, sa construction ainsi que son exploitation ont été confiées à TIRU, filiale de Dalkia au sein du Groupe EDF, en partenariat avec le groupe local Ramery et la société d’architecture Scénario-Ara.
Un seul objectif : le sans-faute
Le processus MYT, dont le TVME est la deuxième expérience, n’a à ce jour jamais rencontré de problème technique ou environnemental, contrairement à de nombreux TMB mal maîtrisés. Il se caractérise par un système de captation et de gestion des odeurs très élaboré, par une rigueur d’exploitation garantissant ainsi une propreté permanente et par une automatisation importante assurant de bonnes conditions de travail pour le personnel.
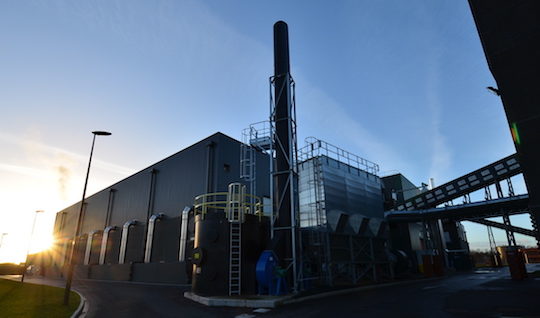
L’ensemble de l’air de travail du TVME est aspiré et traité avant rejet, photo Frédéric Douard
Depuis sa mise en service en janvier 2016, les performances du TVME n’ont cessé de progresser. L’unité a rapidement atteint son régime de croisière avec un taux de traitement de 100 % du tonnage entrant. Néanmoins, le SYMEVAD et son exploitant TIRU travaille encore à une amélioration des performances et engagent régulièrement des études et des travaux d’optimisation de la fiabilité ou d’amélioration des performances. C’est notamment le cas en ce qui concerne le traitement des effluents.
Les étapes des processus
Le principe du procédé MYT est de préparer mécaniquement les OMR, d’homogénéiser un mélange déchets / eau permettant de solubiliser la matière organique, de presser ce mélange pour en extraire un jus qui servira à la production de biogaz, puis de sécher le reste pour en faire un CSR à haut pouvoir calorifique.
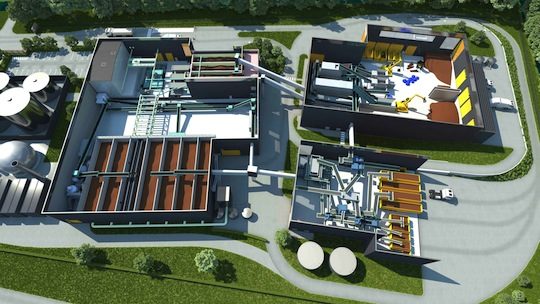
Synoptique du centre de TVME d’Hénin-Beaumont
Module 1 – Réception des déchets
Les camions de collecte déversent les déchets collectés, auprès des habitants du territoire du SYMEVAD, sur la dalle de réception au sein d’un hall fermé et en dépression permettant ainsi de capter les poussières et de maîtriser les odeurs. Des pelles électriques à grappin opèrent un premier tri visuel des déchets en retirant les plus gros éléments ne pouvant être traités par le processus, et alimentent une trémie transférant les déchets à traiter vers le module 2.
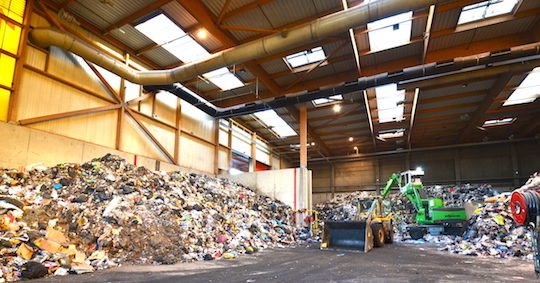
Le hall de réception des déchets avec aspiration de l’air vicié, photo Frédéric Douard
Module 2 – Tri mécanique
Depuis le module 1, les déchets sont transportés par convoyeurs capotés (bande transporteuse) et alimentent un crible rotatif permettant une séparation des déchets par granulométrie.
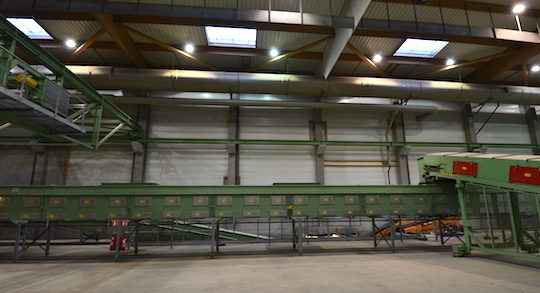
Tous les convoyeurs de matières sont étanches à l’air, photo Frédéric Douard
La fraction inférieure à 100 mm constituée majoritairement de matière et organique passe au travers des mailles du cribles et est envoyée vers le module 3. La fraction supérieure à 100 mm essentiellement composée de fractions sèches, métaux ferreux, plastiques et inertes, subie des traitements complémentaires avant d’être, en partie, transférée vers le module 5.
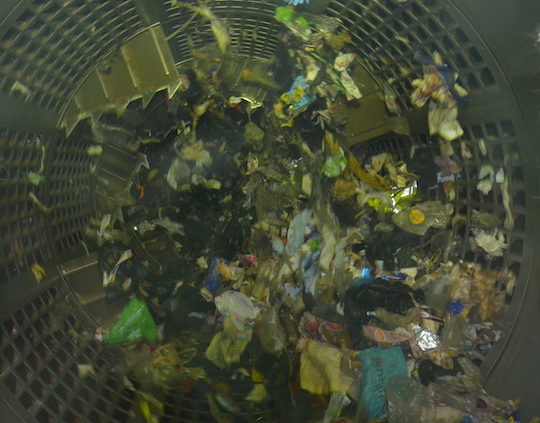
Préparation des CSR au TVME d’Hénin-Beaumont, photo Frédéric Douard
Module 3 – Traitement biologique Procédé DAMP
Le procédé DAMP (Definierter Aerober MischProzess) malaxe pendant 2 à 3 jours les déchets fermentescibles avec de l’eau issue de la station d’épuration voisine dans trois mélangeurs de 450 m³ et 4 m de diamètre appelés les MZR.
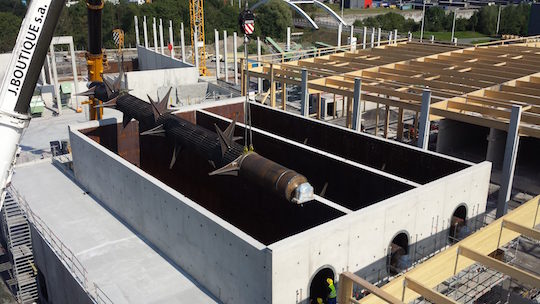
Pose de la vis d’agitation de l’un des trois MZR lors de la construction, photo Optyma
Ensuite, après une première déshydratation dans trois presses à vis, les résidus solides (à 58 % d’eau) sont envoyés vers le module 4 et les résidus liquides rejoignent l’unité de méthanisation. C’est le cœur du procédé garant d’un rendement de production de CSR maximisé, de la qualité des CSR (chlore réduit, homogénéité des produits…) et de l’efficacité de l’étape de séchage.
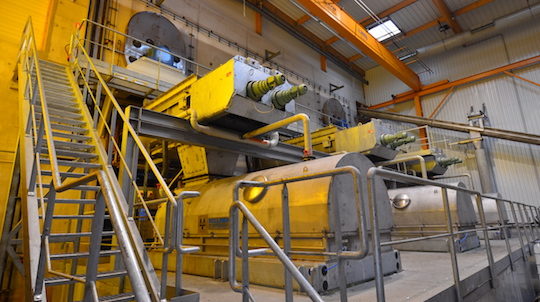
Les trois presses à vis en sortie des trois auges de malaxage dites MZR, photo Frédéric Douard
Module 4 – Séchage biologique
Le séchage biologique des produits solides est réalisé dans des tunnels entièrement automatisés. Cette opération est menée sans apport d’énergie thermique. La dégradation de la matière organique par les bactéries présentent dans les déchets génère une réaction exothermique et donc le séchage du CSR. Le TVME est équipé de huit tunnels de 150 m², remplis automatiquement par des convoyeurs, et vidés automatiquement par un dispositif à fonds mouvants et par une émotteuse mise au point par l’entreprise Eggersmann. Quatre d’entre eux fonctionnent en mode séchage avec ventilation forcée et montent à 60 °C durant quatre jours, pendant que les quatre autres assurent quatre jours de stabilisation. Durant cette phase l’humidité tombe à 10 %. Reste une matière homogène et friable composée à 78 % de matière organique.
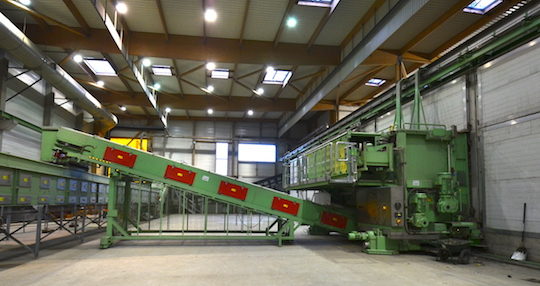
L’emotteuse de vidage étanche des tunnels de compostage, photo Frédéric Douard
Module 5 – Tri et affinage des solides
La matière issue des modules 2 et 4 est triée automatiquement pour en retirer les indésirables comme le PVC et pour en extraire les derniers métaux ferreux et non ferreux, ainsi que les inertes valorisables. Reste à la fin les produits légers qui constituent le CSR qui est ici préparé en deux qualités à ce jour (0 à 20 mm et 0 à 30 mm) pour une valorisation (aujourd’hui à coût négatif) dans les fours des cimenteries locales.
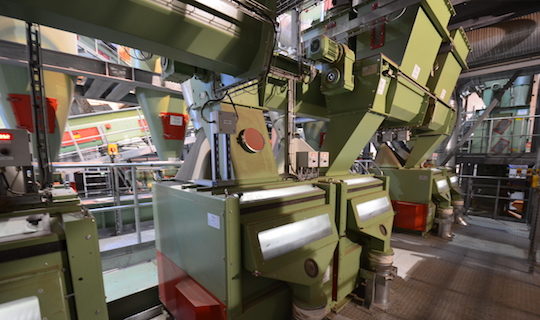
Les chaines d’affinage du CSR, photo Frédéric Douard
Module 6 – Méthanisation
La fraction liquide, après diverses étapes de filtration, passe dans une cuve tampon de 380 m³ qui alimente elle-même deux digesteurs de 2 450 m³ chacun. Le digestat est centrifugé. L’eau repart vers la station d’épuration tandis que le solide rejoint les tunnels de séchage pour devenir du CSR.
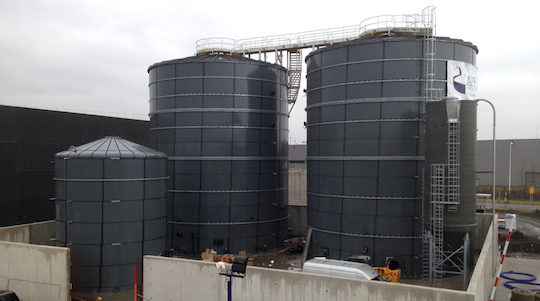
Les trois cuves de méthanisation fournies par APRO INDUSTRIE, ici en cours de montage, photo AI
Module 7 – Épuration et injection du biogaz
Le biogaz est stocké dans un gazomètre afin de réguler la quantité et la pression avant de rejoindre l’épurateur. Celui-ci épure le biogaz et le transforme en biométhane en enlevant l’eau, le soufre et le CO2. Le biométhane est ensuite analysé au niveau du poste d’injection de GRDF qui le rend conforme aux exigences du réseau urbain (odorisation, pression).
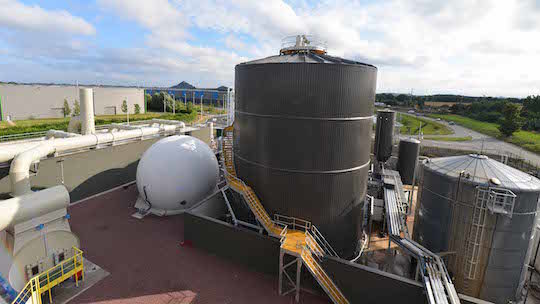
Les installations de méthanisation du TVME à Hénin-Beaumont, photo TIRU – P. Gonzales
Module 8 – Traitement des rejets
Les rejets liquides sont traités dans la station d’épuration voisine. L’air est capté au plus près des sources d’émission, notamment dans tous les locaux, et traité en fonction de sa composition par des laveurs physico-chimiques, dépoussiéreurs, filtres à charbon actif et biofiltres.
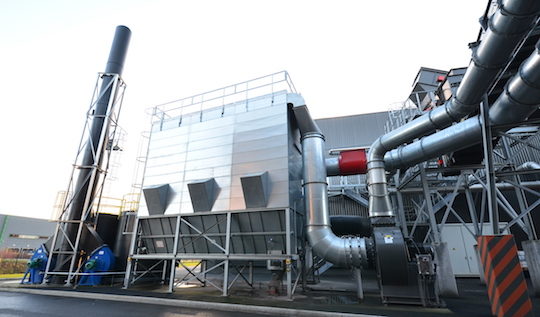
Filtre à manches du module 5, photo Frédéric Douard
Perspectives
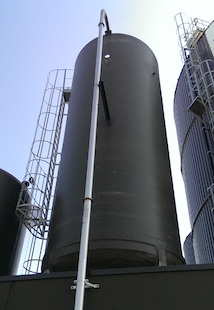
Stockage de réactif pour abattre le H2S du biogaz, photo OVIVE
Le TVME est le premier site français producteur de biométhane avec réinjection dans le réseau public et offre de belles perspectives en matière de production de CSR. Les combustibles produits sont de très bonne qualité et si leur usage reste pour l’instant cantonné aux industries cimentières, des projets de chaufferies à CSR de qualité devraient voir le jour.
Ces perspectives, associées au succès technologique de cet outil s’il se confirme, font du TVME une solution satisfaisante pour la valorisation des déchets non recyclables comme matériau, et en font un exemple à suivre.
Notons enfin parmi les pistes de travail, que TIRU travaille parallèlement sur la gazéification des CSR dans le cadre d’un projet de recherche soutenu par l’ADEME, en partenariat avec EDF et des partenaires institutionnels, académiques et industriels comme les laboratoires LRGP et LERMAB de l’Université de Lorraine et EQTEC.
Quelques contacts :
- Le syndicat : www.symevad.org
- L’exploitant : TIRU – Marine Criado, directrice du site – +33 391 84 29 30 – www.groupe-tiru.com
- Procédé MYT : www.zak-ringsheim.de
- MYT en France : www.optyma.fr
- AMO : www.naldeo.com
- Presses à vis : www.bellmer.de
- Séchage biologique : www.eggersmann-recyclingtechnology.com
- Tri des solides : www.trennso-technik.de
- Broyeur Lindner : www.l-rt.com
- Digesteurs : aproindustrie.com
- Gazomètre : www.special-textile.fr
- Traitement biogaz : www.ovive.fr – www.prodeval.eu
- Epuration biométhane : www.greenlanebiogas.com
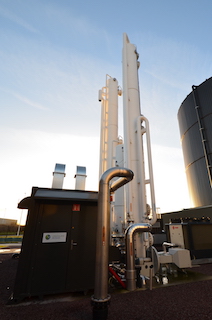
Les équipements de purification du biométhane, photo Frédéric Douard
Frédéric Douard, en reportage à Hénin-Beaumont
ℹ️ Le magazine Bioénergie International est disponible :
- Au détail
- Dans le cadre d'un abonnement