La nouvelle chaudière à marc de café de l’usine Nestlé de Dieppe
Article paru dans le Bioénergie International n°53 de janvier-février 2018
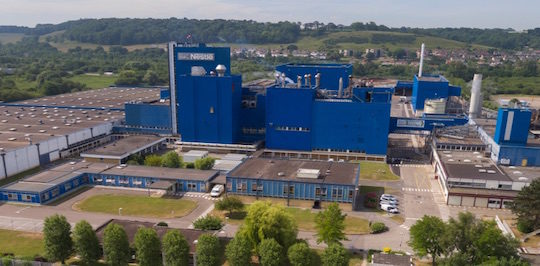
Usine Nestlé de Rouxmesnil-Bouteilles près de Dieppe, photo Nestlé
L’usine de Rouxmesnil-Bouteilles près de Dieppe est l’une des six usines européennes du géant helvétique de l’agroalimentaire à produire l’emblématique Nescafé dont l’entreprise aime à dire qu’il s’en boit 5 500 tasses chaque seconde dans le monde. L’usine, forte de ses 365 salariés, fabrique toute la gamme Nescafé à partir de cafés verts, mais aussi le Ricoré et plusieurs poudres chocolatées. 40 % de cette production de 25 000 tonnes par an alimente le marché français et le reste est exporté vers 55 autres pays. Installée depuis 1970 dans l’estuaire de Arques, fleuve côtier se jetant dans la Manche à Dieppe, cette usine a été pionnière dans la biomasse, hors industrie du bois, pour avoir installé dès 1982 une chaudière fonctionnant en grande partie au marc de café, le sous-produit majoritaire de l’usine.
Une politique volontariste
En 2017, le groupe Nestlé a réinvesti 16,5 millions d’euros pour remplacer la chaudière devenue obsolète, une Babcock de 40 MW qui fonctionnait en co-combustion charbon et marc de café, et qui assurait les besoins en vapeur du site à hauteur de 30 à 45 tonnes par heure.
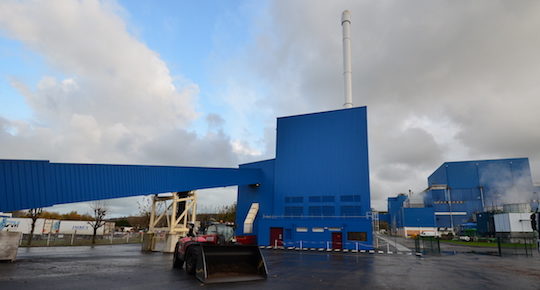
La nouvelle chaufferie biomasse à l’usine Nestlé de Dieppe, photo Frédéric Douard
Cette opération de modernisation a été réalisée dans le cadre du Plan Nescafé visant à réduire l’impact environnemental de la production de Nescafé. Ce plan prévoit de valoriser 100 % du marc de café comme énergie renouvelable, ce qui était déjà le cas à Dieppe, de contribuer à maintenir la qualité de l’air en filtrant 95 % des poussières émises, et de 2010 à 2020, de baisser de 20 % les consommations d’eau et de 30 % d’énergie et de 100 % l’enfouissement de ses déchets. Dès 2018, la nouvelle chaufferie permettra ainsi une réduction de 60 % des rejets de gaz à effet de serre, soit 27 000 tonnes de CO2 par an.
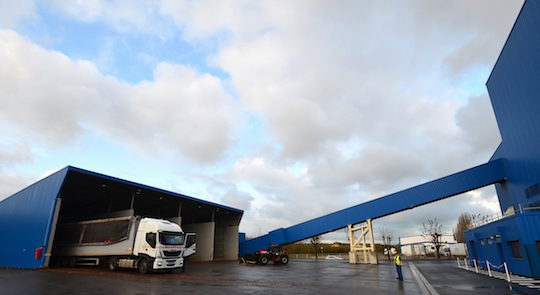
Les silos carrossables à bois et leur convoyeur à bande SERA conduisant à la chaufferie, photo Frédéric Douard
Dieppe n’est pas la seule usine de Nestlé à avoir bénéficié d’un tel équipement puisque depuis 2011 le Groupe a également investi dans trois autres chaudières à biomasse en France : 7 MW en 2011 à la Laiterie de Challerange dans les Ardennes, 5 MW en 2012 à l’usine Herta de Saint-Pol-sur-Ternoise dans le Pas-de-Calais et 20 MW en 2013 à l’usine SITPA-Mousline de Rosières-en-Santerre dans la Somme.
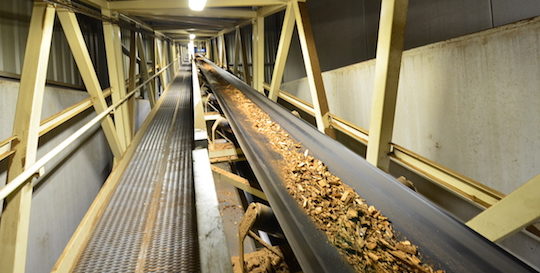
L’une des convoyeurs de bois à bande SERA à la chaufferie Nestlé de Dieppe, photro Frédéric Douard
Cette politique volontariste place aujourd’hui Nestlé France comme leader du Groupe au niveau mondial pour le recours aux énergies renouvelables. Il est à souligner que cet engagement, rendu possible par un contexte politique favorable, notamment celui du Fonds Chaleur Renouvelable, a été décidé en dehors de toute considération de temps de retour sur investissement, et a même été maintenu pendant les périodes où une exploitation au gaz naturel seul aurait été plus économique pour l’entreprise.
Une chaudière mixte bois & marc de café
Le nouveau projet a permis de redimensionner la nouvelle chaudière à 24 MW pour fournir 28 tonnes de vapeur par heure sachant que les besoins moyens sont de 35. Cette réduction de puissance tient compte des gains d’efficacité qui ont été et vont être réalisés sur tous les processus de l’usine.
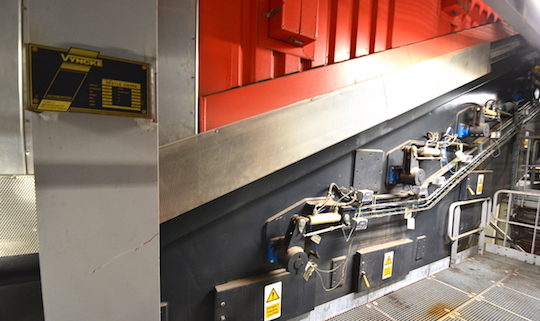
La base du foyer Vyncke avec ses vérins de mouvement des grilles, photo Frédéric Douard
En attendant l’appoint reste assuré par deux chaudières à gaz naturel de 27 t/h chacune. Parmi les principaux processus alimentés en vapeur notons les deux lignes de production du café demandant chacune de 12 à 16 t de vapeur/h pour le coulage du café, son séchage ou sa lyophilisation.
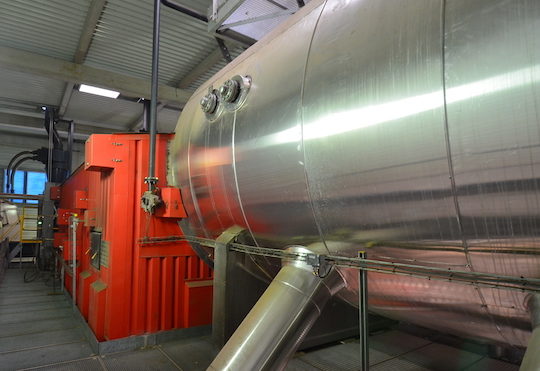
Le ballon de vapeur et au fond le haut de la chaudière VYNCKE, photo Frédéric Douard
C’est le chaudiériste spécialisé VYNCKE qui a été sélectionné pour réaliser l’équipement. Depuis plus de cent ans, le constructeur belge est spécialisé dans la combustion des sous-produits agricoles. Son immense expérience, acquise sur toute la planète, le place aujourd’hui comme leader mondial dans cette catégorie des chaudières à biomasses spéciales, toujours réalisées sur mesure, pour des combustibles et des applications bien précises.
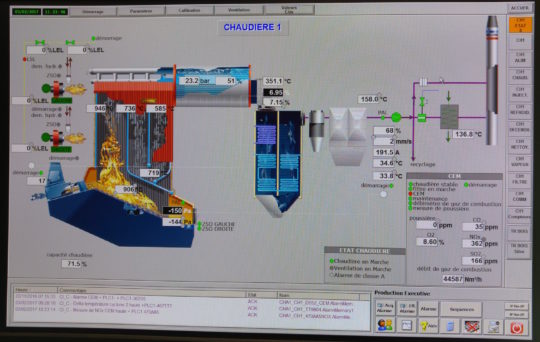
Ecran de supervision de la chaufferie Nestlé de Dieppe, photo Vyncke. Cliquer sur l’image pour l’agrandir.
Car le cahier des charges de Nestlé Dieppe pour cette chaudière était très large. L’industriel demandait en effet aux chaudiéristes souhaitant répondre à son appel d’offre de pouvoir fournir de la vapeur sèche à 24 bar et 224 °C à partir d’un mix de combustibles pouvant varier de 100 % de marc de café mouillé à 100 % de bois déchiqueté en passant par des pourcentages intermédiaires de 50/50, 25/75 ou 75/25, et cela bien sûr de manière performante et écologique. La réalisation du projet a demandé deux ans d’études à VYNCKE puis deux ans de travaux avant une mise en service industrielle en juin 2016.
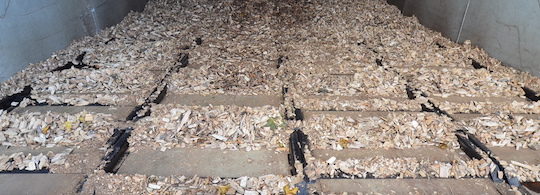
Les silos à bois disposent tous d’extracteurs carrossables SERA, photo Frédéric Douard
L’objectif de Nestlé est ici d’écouler en priorité le marc ressuyé qu’il produit à l’année, et de faire le plus possible le complément avec une énergie renouvelable d’appoint, le bois, en fonction de la disponibilité du marc et des besoins des processus. Notons que le marc est partiellement déshydraté par pressage pour permettre sa combustion et que ce marc ressuyé est stocké dans des silos aériens cylindriques fournis par les Ets SERMIA et équipés d’extracteurs à vis des Ets Morillon.
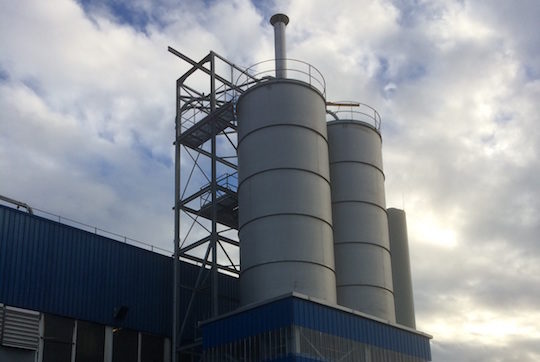
Les nouveaux silos à marc de café fournis par SERMIA, photo Sermia
Le bois est quant à lui composé de 66 % de plaquettes forestières locales fournies par ONF Energie et par 34 % de plaquettes dites urbaines, provenant de travaux d’élagage, fournies depuis la plateforme Ecosys de Criquebeuf-sur-Seine. Il est fourni en granulométrie P100, à une humidité de 35 à 55 % et taux de cendre A2 (moins de 2 % sur sec). Il est livré à côté de la nouvelle chaufferie dans quatre silos de plain-pied, carrossables par des semi-remorques et d’un volume unitaire de 300 m³, le tout procurant une autonomie de fonctionnement de trois jours.
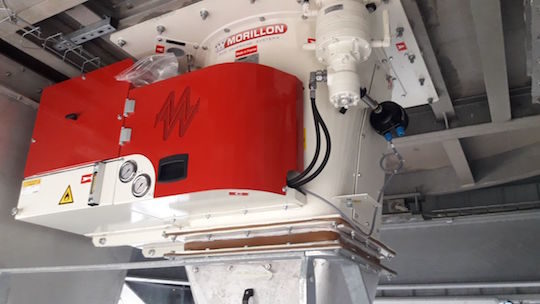
Extracteur MORILLON de l’un des silos à marc de café, photo Sermia
Depuis les silos, le bois est extrait par des échelles hydrauliques et transporté jusqu’à la chaudière par quatre convoyeurs à bande successifs d’une longueur totale de plus de 150 mètres. Ces équipements, ainsi qu’un déferrailleur et un crible à disque pour éliminer les surlongueurs, ont été fournis et installés par les Ets Sera Biomass Handling, constructeur implanté dans la région.
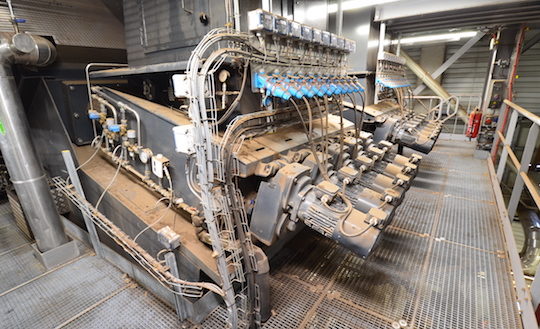
Les dix vis de dosage des combustibles des deux trémies de chargement de la chaudière, photo Frédéric Douard
Arrivé dans la chaufferie, le bois est stocké dans deux trémies de dosage qui reçoivent également le marc de café. De là, les deux combustibles sont introduits ensemble sur les deux grilles du foyer par deux dispositifs à cinq vis d’Archimède juxtaposées. Car la particularité de cette installation est de disposer de deux grilles mobiles parallèles !
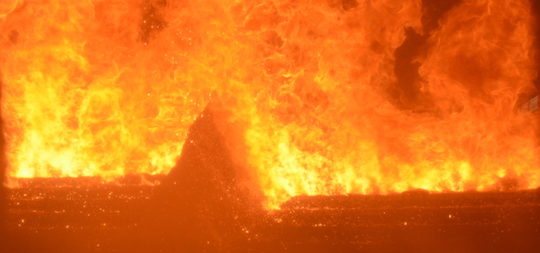
La gazéification sur les deux grilles jumelées VYNCKE, photo Frédéric Douard
Dès 2018, la consommation annuelle de bois sera de 14 000 tonnes. La conduite et la maintenance de la chaufferie est assurée en interne par une équipe de douze personnes qui s’occupe aussi de tous les auxiliaires de l’usine (presses à marc, centrifugeuses, fourniture de vapeur, air comprimé, etc.).
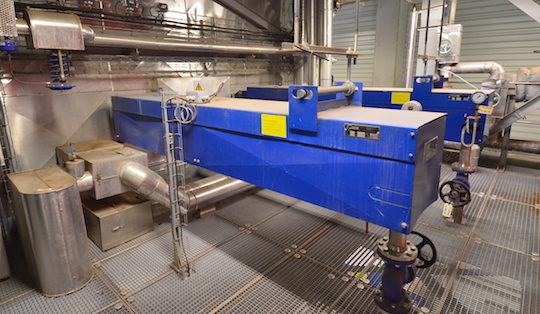
Ramoneurs vapeur de l’économiseur de la chaudière, photo Frédéric Douard
Les dispositifs de maîtrise des émissions
Les cendres foyères sont récupérées en voie humide et valorisées en agriculture dans le cadre d’un plan d’épandage. Du côté des particules fines, les cendres volantes résiduelles sont récupérées pour les plus grosses par un double filtre cyclonique en aval des échangeurs et par un filtre à manches pour les plus fines.
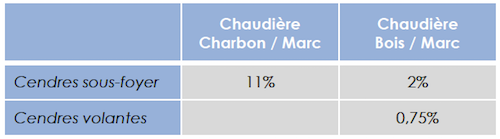
Impact de la nouvelle chaudière sur la production de cendres de l’usine Nestlé de Dieppe, source Nestlé
Par ailleurs, étant donné la teneur en soufre et en azote naturellement élevée dans le marc de café, deux systèmes de traitement secondaire des fumées ont dû être mis en place dès la conception de la chaudière pour maintenir les limites d’émissions imposées par Nestlé au constructeur : un abattement des NOx par l’injection d’urée dans le foyer (SNCR) et un abattement des SOx par injection de chaux en amont du filtre à manches de marque Lühr.
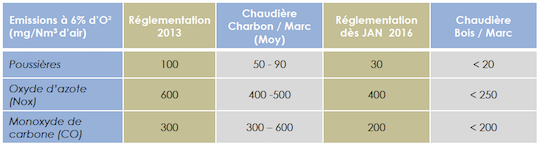
Impact de la nouvelle chaudière sur les émissions de l’usine Nestlé de Dieppe, source Nestlé
L’ensemble du suivi de ces émissions est réalisé en continue par une baie d’analyse Siemens.
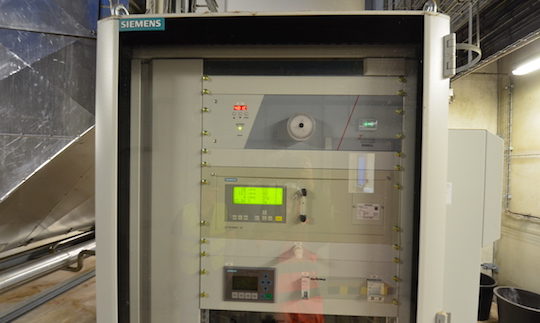
Baie de contrôle en continu des émissions, photo Frédéric Douard
Optimisation d’une co-combustion complexe
La co-combustion de deux combustibles très différents, introduits dans des pourcentages variés n’est pas aisée, même si ici les deux produits ont des pouvoirs calorifiques proches (2,7 MWh/tonne de marc et de 2 à 3 MWh/tonne de bois). Par exemple sur la question de la granulométrie, le marc est beaucoup plus fin que le bois et présente donc une dynamique de combustion plus rapide et plus volatile. La maîtrise de la volatilité du marc est un point crucial en matière de qualité de combustion et il faut signaler ici qu’à ce jour toutes les grandes chaudières récentes à marc de café dans le monde sont des chaudières à lit fluidisé. Or, c’est vers une technologie à grilles que Nestlé s’est tourné !
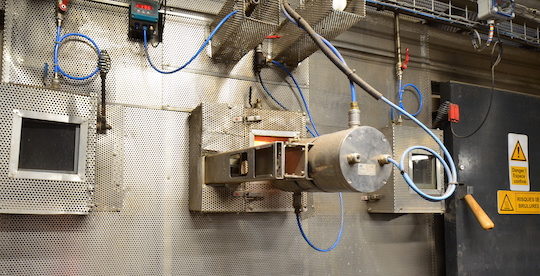
La caméra de contrôle visuel en continu du foyer, photo Frédéric Douard
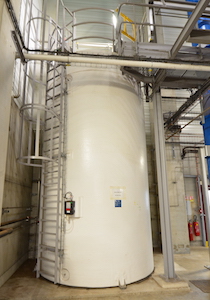
La réserve d’urée pour le traitement des oxydes d’azote, photo Frédéric Douard
La solution à grilles a été retenue pour deux raisons principales : le niveau plus faible d’investissement et la plus grande simplicité de conduite. Mais derrière ces avantages, pour gérer les problèmes inhérents à la finesse du marc par exemple, dès la conception, le constructeur de la chaudière a dû mettre en place certaines mesures. Il a notamment prévu des grilles à chevauchement latéral pour éviter que le marc ne passe à travers.
Par ailleurs, le marc étant très humide à l’introduction en foyer, mais présentant de par sa granulométrie une combustion très vive une fois sec, le choix du constructeur s’est porté sur les grilles refroidies à l’air tout en conservant la totalité des équipements spéciaux de sa chaudière de base, comme les collecteurs et supports de barreaux des grilles fixes refroidis à l’eau, et tout ceci afin de protéger les équipements et d’éviter la mâcheférisation.
Il a aussi mis en place une recirculation partielle des cendres pour optimiser la combustion des fines particules de marc. Ces cendres sont récupérées dans des cônes sous les zones de sédimentation de la chaudière et transportées par un convoyeur tubulaire à chaîne robuste vers un système de réintroduction dans le foyer.
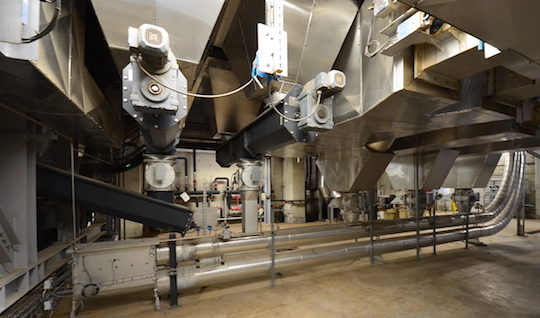
Circuit de collecte des cendres pour réinjection dans le foyer, photo Frédéric Douard
Par ailleurs, les responsables de l’usine ont souhaité élargir le cahier des charges de la co-combustion à d’autres sous-produits de leurs processus : les pellicules, les sédiments et les concentrâts. Les pellicules sont des produits fins et secs récupérés en sortie de torréfaction des grains de café.
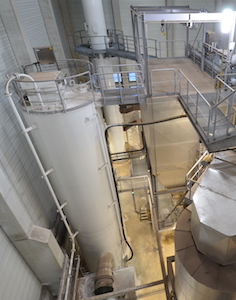
Le filtre à manches LÜHR et son réservoir de chaux, photo Frédéric Douard
Les deux autres sous-produits proviennent des processus de déshydratation partielle du marc en vue de sa combustion. Ainsi, après passage dans les « cafetières géantes » de l’usine, le marc est pressé, ce qui produit un premier jus chargé en particules. Ce jus est ensuite centrifugé en deux nouveaux éléments : des sédiments et un second jus. Ce dernier est enfin concentré par évaporation et se transforme en concentrât, sous forme d’une boue.
Si les pellicules ne posent aucun problème à la combustion, la nature et composition des concentrâts entraînent diverses difficultés d’exploitation : encrassement important de l’installation, augmentation importante des fines générées dans le filtre à manches, réactions chimiques dans le foyer, etc.
Pour traiter la question de l’encrassement, Vyncke procède actuellement à un test, sur la base de sa collaboration réussie sur plusieurs de ses chaudières en exploitation, avec EcoSoftec, inventeur et développeur de la technologie FireCube. Vyncke a ainsi fait installer à la fin de l’année 2017 la dernière génération de FireCube EDNC à Dieppe. Celui-ci injecte dans la zone de combustion un catalyseur porteur d’oxydes de manganèse qui facilite et complète les réactions chimiques de l’oxydation thermique.
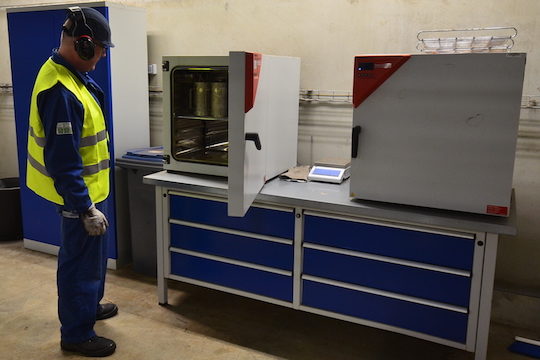
Contrôle de l’humidité du bois dans deux études Binder, photo Frédéric Douard
Il est important de noter que l’introduction de cette chimie ne génère aucune charge supplémentaire dans les fumées, puisque le dosage reste homéopathique et que les oxydes de manganèse sont essentiellement piégés dans les cendres. Sur ce point, EcoSoftec garantit le respect de la réglementation incinérateur, beaucoup plus sévère que ce qu’imposent à ce jour les normes ICPE pour la combustion des biomasses vierges.
À l’heure de la mise sous presse de cet article, après un mois de fonctionnement du FireCube, les résultats sont encourageants, montrant une tendance à l’auto-nettoyage des zones encrassées.
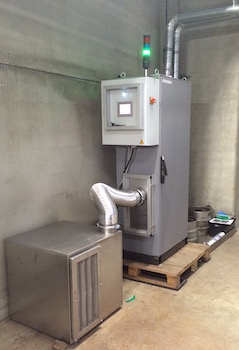
Dispositif Firecube d’injection de catalyseur de combustion, photo Ecosoftec
Contacts :
- Nestlé : Minh Hiep Nguyen – +33 160 53 13 85 – Minh-Hiep.Nguyen@fr.nestle.com
- Vyncke : Jérôme Béarelle / +33 970 444 630 / +33 619 88 33 53 – jbe@vyncke.com – www.vyncke.com
- Sera Biomass Handling : www.sera-energie.com
- Pesée du bois en continu : www.preciamolen.com
- Mesure de l’humidité du bois : www.binder-world.com
- Extracteurs des silos à marc : +33 241 56 50 14 – contact@morillon.eu – www.morillonsystems.com
- Silos à marc : www.sermia.eu
- Filtre à manches avec traitement à la chaux : www.luehr-filter.com
- Baie d’analyse des gaz en continu : www.siemens.com
- Ecosoftec : Jean-Pierre RAVIX – contact@ecosoftec.eu +33 479 33 20 55 – www.firecube-eco-combustion.com
Frédéric Douard, en reportage à Rouxmesnil-Bouteilles
ℹ️ Le magazine Bioénergie International est disponible :
- Au détail
- Dans le cadre d'un abonnement