À la briqueterie de La Séguinière, Bouyer-Leroux s’approche de la décarbonation totale avec sa chaudière à bois de recyclage
Article paru dans le Bioénergie International n°92 de l’été 2024
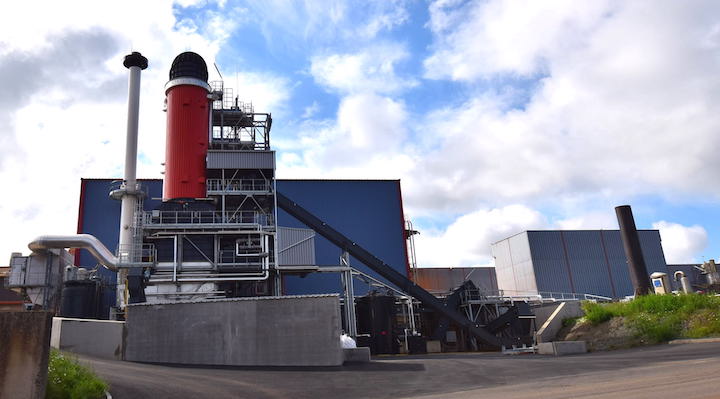
La nouvelle chaudière biomasse de La Séguinière, photo Frédéric Douard
Avec ses 162 M€ de chiffre d’affaires en 2022-23, la société coopérative Bouyer-Leroux est leader en France sur le segment des briques extrudées isolantes, briques de séparation et éléments de grande longueur en terre cuite. Fondée en 1959 à La Séguinière, dans le département de Maine-et-Loire, aujourd’hui principal site de production, l’entreprise emploie 530 collaborateurs sur son activité terre cuite répartie sur sept sites de production. Au printemps 2024, elle a mis en service un nouveau foyer biomasse de 10 MW sur son site historique de la Séguinière, qui va permettre de monter le niveau de décarbonation de l’activité de cette usine à hauteur de 85 %.
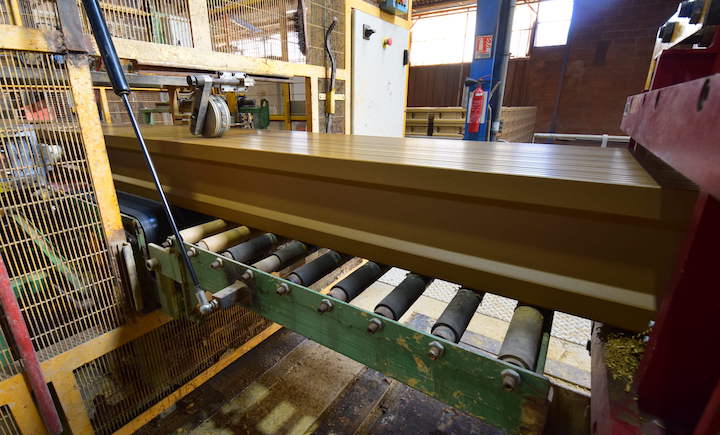
L’extrusion des briques à La Séguinière, photo Frédéric Douard
La Séguinière, un site déjà décarboné à 50 %
Le site de La Séguinière est le plus grand site de production de briques extrudées de France. Sa production de 300 000 tonnes par an correspond à la construction de 18 000 maisons par an. Jusqu’à début 2024, cette production affichait un taux moyen de décarbonation de 50 % de ses besoins thermiques qui se montent à 170 GWh/an. En 2023, son mix énergétique était le suivant : 10 % biogaz, 40 % sciure de bois et 50 % de gaz fossile.
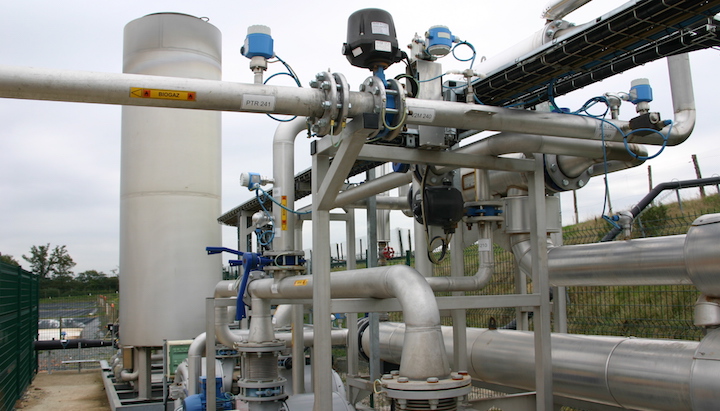
Poste d’extraction et de désulfuration du biogaz du CET de La Ségunière, photo BL
Le processus de production de l’argile cuite suit un long enchaînement d’ateliers : extraction de la terre sur le site même de production, préparation de la terre (broyage, homogénéisation et malaxage), extrusion, découpe, séchage et cuisson. Tout au long de cette chaîne, l’usine de la Séguinière utilisait déjà la biomasse à trois niveaux.
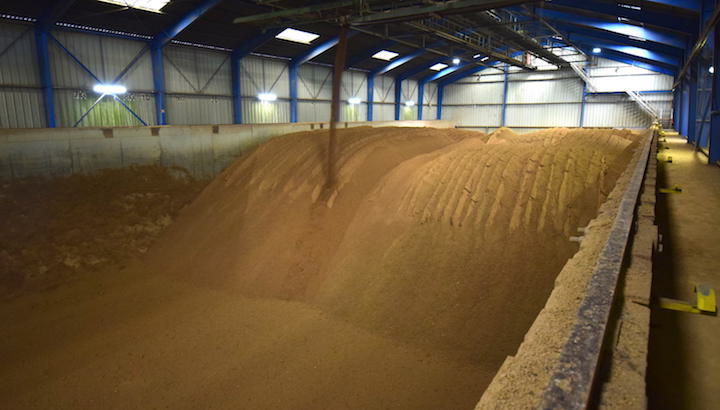
La cave à terre crue à la briqueterie de La Séguinière, photo Frédéric Douard
L’addition de biocombustibles : pour rendre les briques plus légères et plus isolantes, de fines particules de combustibles solides, sont incluses à l’argile lors du malaxage. Lors de la cuisson, l’auto-combustion de ces combustibles dans la masse produit de micro-alvéoles de gaz dans les parois, ce qui baisse la masse volumique des produits, améliore leur performance isolante, et participe en même temps à l’apport thermique de cuisson. Le charbon fossile, jadis utilisé, a été remplacé par de la biomasse agricole ou forestière, comme de la sciure ou des coques de tournesol. C’est cette incorporation dans l’argile qui a prévalu à la création de la marque Bio’bric du fabricant.
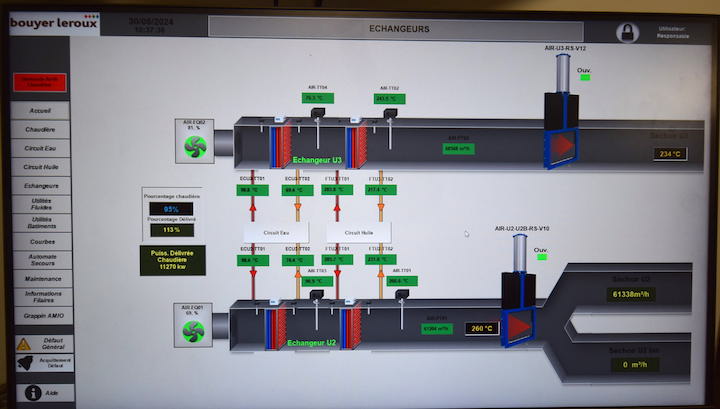
Synoptique du réseau d’air chaud de La Séguinière pour le séchage des briques, photo Frédéric Douard
Le séchage des briques, au départ en argile crue, est réalisé sur chaque ligne sur la base de l’air de refroidissement des briques à la sortie de chaque four, un air à relative basse température, et qui est désormais complété par un air à haute température obtenu par la nouvelle chaudière à CSR.
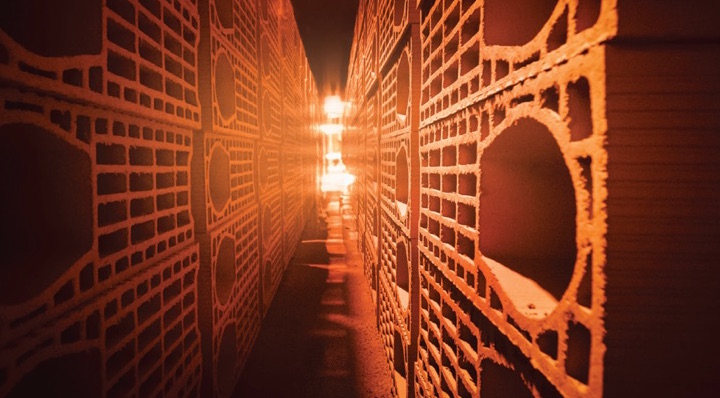
Briques dans le tunnel de cuisson, photo Bouyer-Leroux
La cuisson est l’opération qui va demander le plus de chaleur. Elle se réalise dans des fours-tunnels de 120 mètres de long. Des wagons chargés chacun de treize tonnes de briques y progressent en continu, le four pouvant en contenir trente à la fois. La cuisson y dure quatorze heures et passe par une montée en charge bien précise et ensuite par un refroidissement contrôlé. Pour cela, les apports thermiques allant jusqu’à 920 °C, se doivent d’être parfaitement régulés et au bon endroit. Ils sont réalisés par des brûleurs situés sur les côtés et sur le toit du tunnel et sont alimentés actuellement pour moitié par du gaz naturel et pour l’autre moitié par de la sciure de bois.
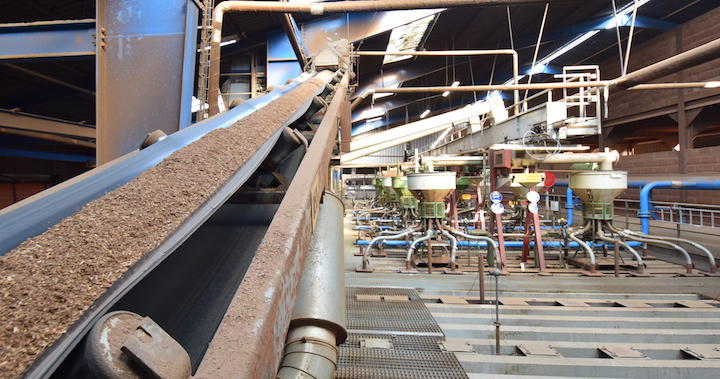
Les brûleurs de cuisson de La Séguinière alimentés en sciure et copeaux de bois, photo Frédéric Douard
Les brûleurs à sciure, en place depuis 1983, ne sont pas disposés dans la partie de montée en température du tunnel, car la biomasse solide demande une température minimale pour s’auto-enflammer. À la Séguinière, les brûleurs à gaz dans la partie dite de l’avant-feu, sont alimentés prioritairement par du biogaz produit sur le site, et sont complétés par du gaz naturel si besoin. L’usine de la Séguinière dispose en effet, en partenariat avec Veolia, d’un centre d’enfouissement de déchets, installé sur une partie épuisée de son site d’extraction d’argile, et qui génère un peu plus de 15 GWh de biogaz par an, autoconsommé à 100 %.
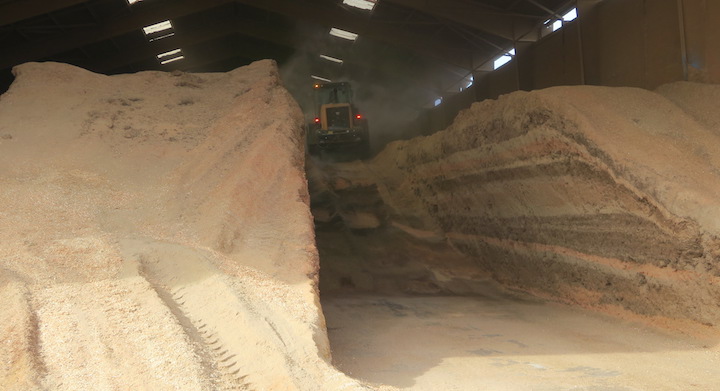
Le stockage de sciures et copeaux de bois à La Séguiniere pour l’alimentation des brûleurs de cuisson, photo BL
Un investissement à 13,2 M€
L’objet de la nouvelle chaudière à biomasse de la Séguinière est de remplacer le séchage au gaz naturel par un séchage complet à la biomasse. Les travaux de construction ont démarré au premier trimestre 2022 pour s’achever en février 2024.
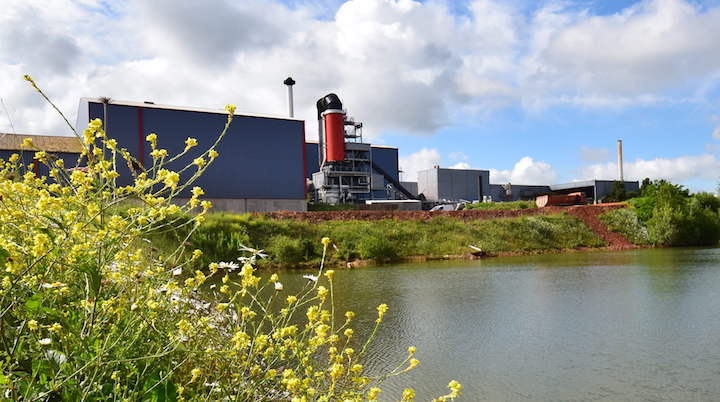
La nouvelle chaufferie biomasse de La Séguinière, photo Frédéric Douard
La fourniture de cet équipement thermique, qui fonctionne avec du bois-déchet, aussi appelé communément bois B, a été confiée au constructeur belge Vyncke. Ce constructeur bénéficie d’une longue expérience en la matière après avoir équipé de nombreux sites industriels utilisant ce type de déchets, en Belgique, en France, en Europe et dans le Monde.
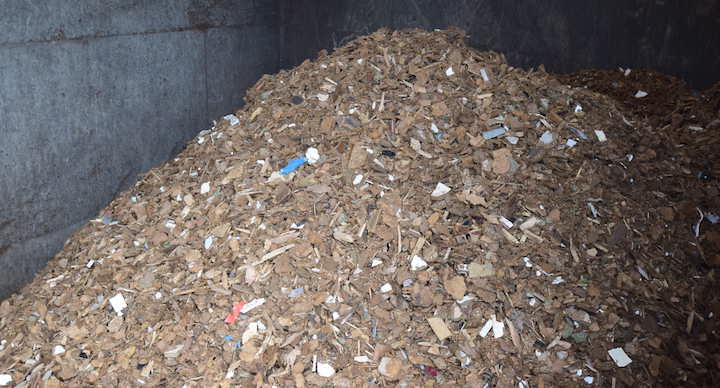
Le combustible CSR de la nouvelle chaudière de La Séguinière, photo Frédéric Douard
D’une puissance de 10 MW utiles, cette chaudière est alimentée en bois via le dispositif éco-mobilier par la société Brangeon, implantée localement depuis 1919. Cette société collecte, prépare et valorise les déchets de bois déposés par les particuliers et les entreprises dans les déchèteries de la région. Ce combustible est classifié comme un Déchets d’Eléments d’Ameublement et entre dans la famille des combustibles solides de récupération, les CSR.
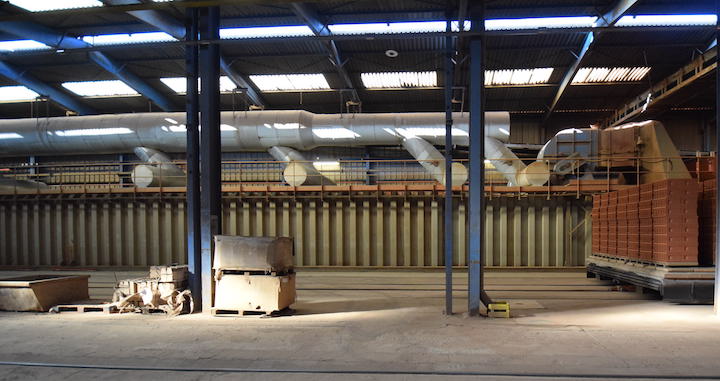
L’un des deux fours de séchage des briques à La Séguinière, photo Frédéric Douard
Cet investissement de 13,2 millions € permet d’alimenter en air chaud les trois séchoirs-tunnels du site. En fonctionnement durant 46 semaines par an, il consommera jusqu’à 15 000 tonnes de bois de recyclage à l’année. La phase de séchage, qui consomme 50 GWh par an en plus de la chaleur récupérée sur le refroidissement des briques en sortie de fours, est donc dorénavant décarbonée à 100 %. Ceci amène un niveau de décarbonation global du site à 85 %, selon le mix suivant : 15 % de gaz fossile, 10 % de biogaz, 40 % de sciure de bois et 35 % de bois écomobilier.
Du lourd pour la nouvelle installation biomasse
Le constructeur Vyncke a été chargé de fournir l’ensemble des équipements permettant de produire 140 000 m³ /h d’air à 250 °C en entrée des tunnels de séchage qui sont au nombre de trois. Sa prestation débute par la fourniture des échelles extractrices de bois dans le silo, jusqu’au traitement des gaz de combustion.
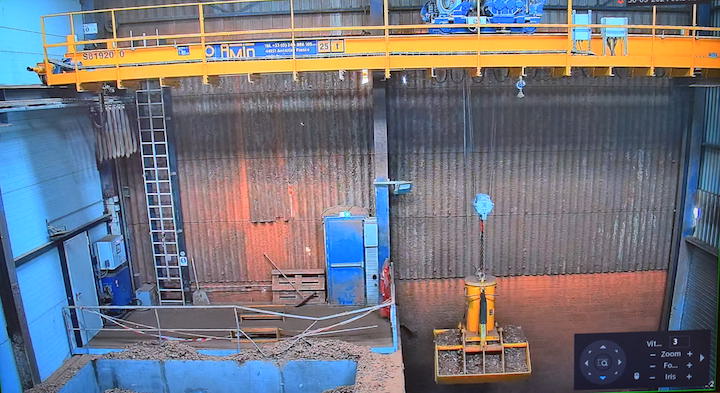
Ecran vidéo du silo à combustible de la nouvelle chaudière, photo Frédéric Douard
La partie manutention au grappin dans le silo à combustible a quant à elle été confiée par le maître d’ouvrage à une entreprise régionale pour privilégier un service après-vente et une maintenance de proximité, un choix stratégique pour un équipement bardé de capteurs et de systèmes de communication. C’est la société Amio, basée à Ancenis, qui a donc réalisé l’installation, une entreprise spécialisée dans le domaine depuis 30 ans et forte de 20 collaborateurs. Pour la partie automatismes, Amio travaille en synergie avec l’entreprise 2Adis, également basée à Ancenis.
L’un des premiers convoyeurs dit de type « winchester » sur le territoire français
Dans un convoyeur à chaînes classique, les raclettes vont et reviennent dans un même compartiment, le plus fréquemment en « transport pas le bas », c’est-à-dire transport sur la tôle de fond et retour des racleurs en partie haute. Les inconvénients de ce schéma de fonctionnement est que l’aller et le retour se croisent et que cela peut engendrer des désordres lorsque de gros paquets de combustibles chutent des extracteurs sur les chaînes, ou lorsque le combustible contient des dimensions hors normes voire des corps étrangers. En effet, les surcharges ou les surdimensions sur les chaînes de convoyage peuvent occasionner un effet de cisaillement et un blocage voire une casse du convoyeur.
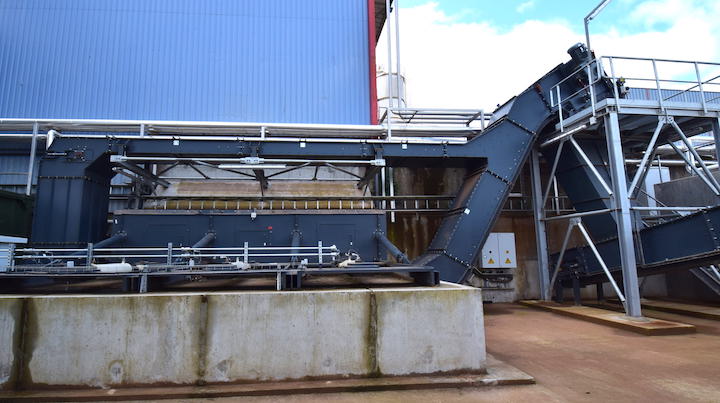
Le nouveau système de convoyeur Winchester en sortie de silo à La Séguinière, photo Frédéric Douard
Il est aussi possible d’utiliser des convoyeurs en « transport par le haut » (l’aller et le retour sont séparés par une tôle, sur laquelle s’effectue le transport « aller » ; le retour se faisant alors par le dessous du convoyeur. Si cette solution résout la plupart des problèmes décrit ci-avant, elle présente un inconvénient de taille : l’accessibilité à la chaîne de retour est plus compliquée pour la maintenance puisqu’il faut nécessairement démonter cette tôle intermédiaire pour accéder à la partie basse du convoyeur et au retour de chaîne.
Sur des installations où le 100 % de disponibilité est requis, pour ne pas interrompre un processus de production qui engage un volume très important de produit, et où un arrêt représenterait une perte sèche énorme, le risque même minime d’un incident sur le convoyeur n’est pas une option.
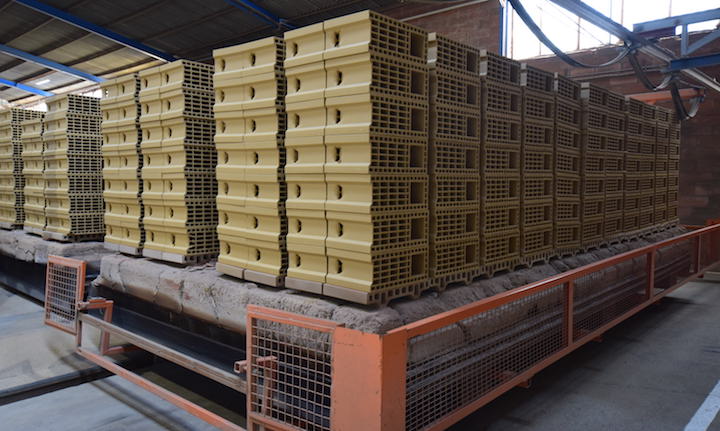
Chariots de briques en sorte de four à la Séguinière, photo Frédéric Douard
Le principe du convoyeur « winchester » est que l’aller et le retour des chaînes de convoyage à raclettes ne se font pas par le même chemin. Chaque parcours se fait dans un compartiment séparé de sorte que les risques évoqués ne puissent quasiment pas se produire tout en garantissant un accès aisé à l’ensemble des éléments du convoyeur pour sa bonne maintenance.
Une grille de combustion très polyvalente
Dans la phase de démarrage du projet, le combustible choisi est un bois sec à haut pouvoir calorifique et le raisonnement du planificateur pourrait être de profiter de cette qualité pour choisir une chaudière capable de brûler ce type de bois. Mais une chaudière à biomasse, quelle qu’elle soit, est faite pour fonctionner au moins 25 ans, alors comment savoir quel type de bois sera le plus intéressant à brûler dans 5, 10 ou 20 ans ? Pour ne pas obérer des opportunités économiques futures par changement de combustible, Vyncke a proposé son foyer à grille DWS-Hybride.
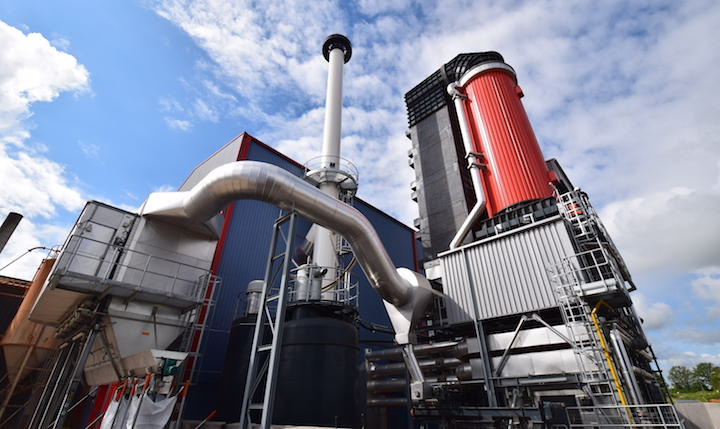
Le chaudière Vyncke et son filtre à manches, photo Frédéric Douard
Cette grille, qui est ici composée de deux zones refroidies par eau en partie haute, et deux zones refroidies par air en partie basse, permet de brûler, soit des combustibles très secs, soit des combustibles très humides, ou les deux mélangés, le tout sans faire de mâchefer et en préservant le niveau de performances de la combustion. En cas d’utilisation de bois sec, la combustion s’opère rapidement sur les zones du haut, sans encombre car refroidies assez fortement par l’eau. En cas d’utilisation de bois humide, la combustion se décompose sur l’ensemble des quatre zones. Et les deux combustibles peuvent aussi être mélangés et conduire au même résultat. Cette technologie très aboutie procure une immense souplesse d’exploitation dans le temps long, mais aussi au jour le jour.
Rappelons aussi que les foyers Vyncke sont tous refroidis par eau, ce qui évite les surchauffes autour de la grille, et ce qui limite fortement les risques de dégradation de l’équipement, de production de mâchefers et d’oxydes d’azote.
Un équipement de combustion à hautes performances
La chaudière installée à La Séguinière génère 10 MWth de chaleur en huile thermique et en eau chaude. Sa mission est de chauffer de l’air ambiant en deux étapes : un échange eau chaude / air ambiant en préchauffage, puis huile thermique à 280 °C / air préchauffé pour monter l’air à 250 °C minimum. Notons que les installations en huile thermique sont soumises aux normes de sécurité de la rubrique ICPE 2915, pour les systèmes de chauffage utilisant comme fluide caloporteur des corps organiques combustibles.
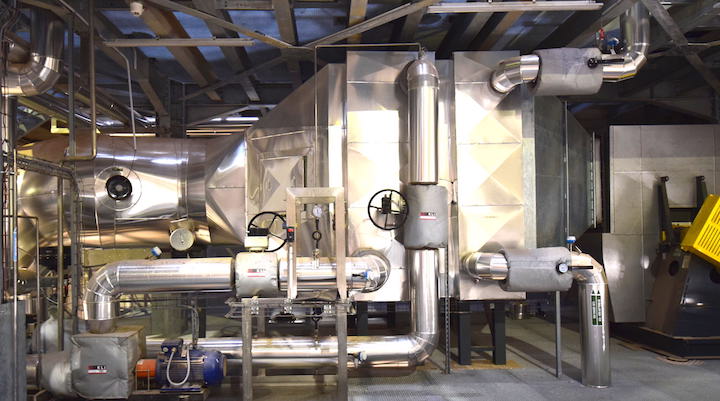
L’échangeur huile thermique air pour le chauffage des séchoirs, photo Frédéric Douard
La chaudière bénéficie d’un économiseur en fin de parcours des gaz, et qui produit l’eau chaude. L’eau chaude est également produite par les circuits de refroidissement de la grille, du poussoir d‘introduction du bois, de la porte du brûleur, des vis de décendrage et du foyer. Vyncke garantit un rendement global de 87 %.
Des émissions maitrisées et contrôlées
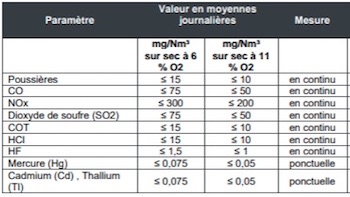
Valeurs limites d’émissions atmosphériques pour la chaudière à CSR de La Séguinière
La conception même de la grille et du foyer sont de base en mesure de garantir la meilleure combustion possible. La combustion y est de plus optimisée en permanence par le contrôle de l’humidité du bois dans la trémie d’alimentation. Mais comme dans toutes les chaudières biomasse de puissances importantes, ces mesures ne suffisent seules à respecter les normes sévères d’émissions atmosphériques, en particulier sur les poussières et dans les grandes puissances sur le NOx. La chaudière est donc équipée d’une unité de traitement des oxydes d’azote par injection d’urée, et pour les poussières d’un filtre cyclonique suivi d’un filtre à manches.
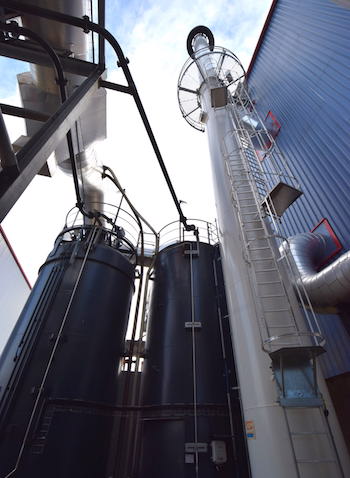
Les cuves de charbon actif et de bicarbonate pour les traitements dans le filtre à manches, photo Frédéric Douard
En France, l’installation répond à la classification ICPE 2971 sur les installations de production de chaleur ou d’électricité à partir de déchets non dangereux préparés sous forme de combustibles solides de récupération. Ceci implique de traiter les gaz de combustion aux charbons actifs et avec une base, ici du bicarbonate de sodium, au niveau des manches du filtre. Les obligations impliquent également de contrôler les résultats de ces traitements par une mesure en continu des émissions atmosphériques en sortie de cheminée.
Enfin, comme nous avons ici affaire à la combustion d’un déchet et selon la réglementation européenne sur la combustion des déchets non dangereux, les gaz de fumées doivent être maintenus à plus de 850 °C durant au moins deux secondes pendant tout le fonctionnement de l’installation. Ceci est garanti par un brûleur à gaz, qui sert principalement pendant les phases de démarrage et d’arrêt de l’installation, et qui permet également de venir en soutien pour pallier aux aléas sur le combustible.
Contacts :
- Bouyer-Leroux : Sébastien Elissalde, directeur Énergies Environnement – 02 41 63 76 16 – selissalde@bouyer-leroux.fr – www.bouyer-leroux.com
- La chaudière à bois : Jérôme Béarelle – 06 19 88 33 53 – jbe@vyncke.com – www.vyncke.com
- Pont roulant du silo à combustible : 02 40 98 81 05 – www.amio.fr
- Mesure en continu des gaz de combustion : www.fr.envea.global
- Cheminée : www.unionthermique.fr
- Mesure humidité du bois en continu : www.moisttech.com
- Convoyeurs chaudière : www.trasmec.com
Frédéric Douard, en reportage à la Séguinière
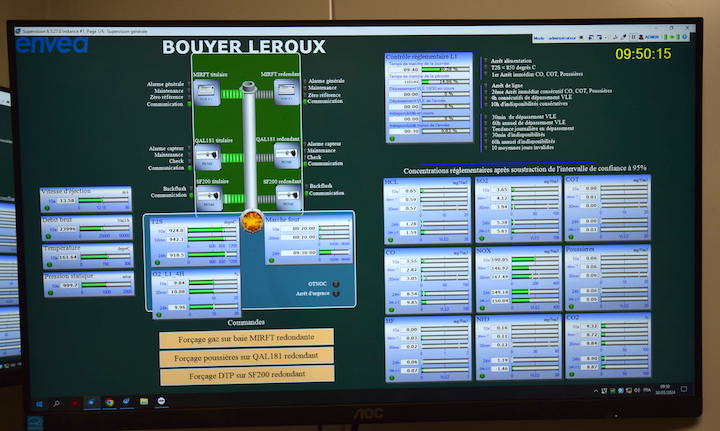
Ecran de lecture des mesures en continu des émissions atmosphériques de la chaudière Vyncke, photo Frédéric Douard
ℹ️ Le magazine Bioénergie International est disponible :
- Au détail
- Dans le cadre d'un abonnement