Cometh, usine de méthanisation avec valorisation du digestat en compost normé
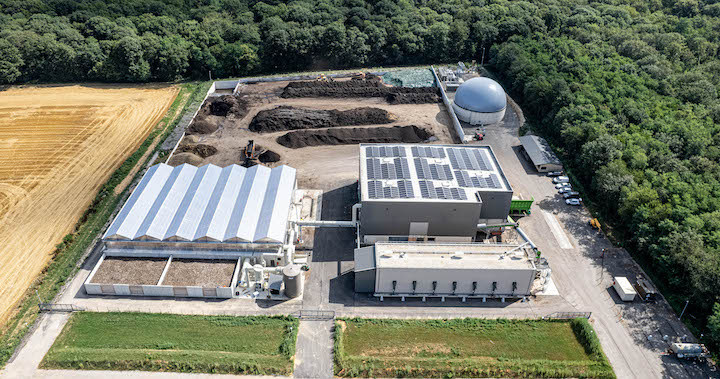
Le site Cometh à Allériot près de Chalons-sur-Saône, photo Jean Marc Baudet
Située sur la commune d’Allériot près de Chalon-sur-Saône, la société Cometh a inauguré le 8 septembre 2023 une unité de méthanisation particulière en ce sens qu’elle produit du compost normé. Ce projet a été initié par Edouard Leledy, agriculteur céréalier reconverti en 2002 dans la production de compost. Vingt ans plus tard, Edouard Leledy met en service une nouvelle usine de compost, à côté de la première, mais différente, car elle produit également du biométhane. Son principe est de digérer les matières puis d’en composter le digestat pour obtenir, non pas un déchet à épandre sur autorisation, mais un produit à vendre, un concept qui pourrait faire des émules alors que les surfaces d’épandage se réduisent dans certaines régions françaises au fur et à mesure que les projets de méthanisation voient le jour.
Un projet mené avec un large partenariat
Le projet de la méthanisation a germé dans l’esprit d’Edouard Leledy dès 2012, au lendemain de la publication des premiers tarifs de rachat du biométhane en injection réseau. Mais il a fallu attendre 2018 pour qu’il prenne corps, notamment suite à sa rencontre avec Aloïs Klein, agriculteur porteur du projet Méthamoly dans la Loire et co-développeur de trois autres projets de méthanisation. Puis le cercle des futurs actionnaires s’est élargi à Bourgogne Recyclage, apporteur de matières, à Prodeval apporteur de technologie, et à la Coopérative Bourgogne du Sud qui commercialisait déjà le premier compost Leledy.
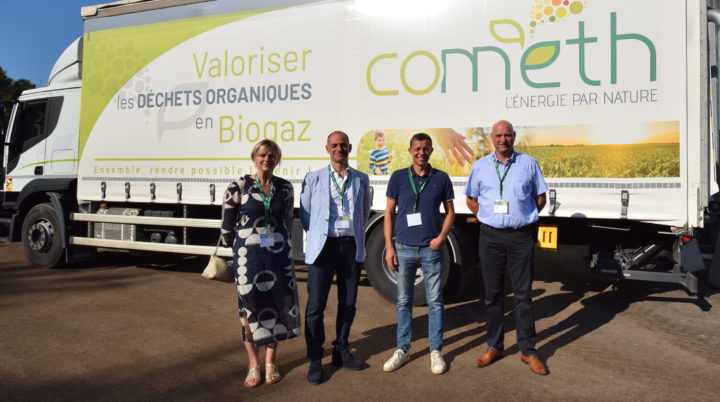
Depuis la gauche le jour de l’inauguration, Armelle Goyard et Eric Passetti de GRDF, Aloïs Klein et Edouard Leledy de Cometh, photo Frédéric Douard
Après les études et les démarches administratives, la construction a commencé en 2021 et la mise en exploitation complète s’est faite le 12 janvier 2023 avec la première injection dans le réseau géré par GRDF. Notons que la fusée Cometh comporte plusieurs étages et que les cartons du projet contiennent aussi une station bioGNV, une unité de purification et de liquéfaction de CO2 ou encore une centrale de cogénération pour maîtriser à l’avenir les augmentations attendues des prix de l’électricité consommée sur le site.
Un projet à 14 millions €
Le procédé mis en œuvre par Cometh est une méthanisation en voie sèche continue, utilisant la technologie dite du digesteur piston, suivi d’un traitement du digestat par compostage. Le choix d’une voie sèche s’est faite au regard de l’étude des gisements qui a montré que les ressources identifiées affichaient un taux moyen de matière sèche élevé de 40 %. Le choix du processus en continu a été dicté par l’échelle du projet. C’est la société allemande Strabag Umwelttechnik GmbH qui a été retenue pour réaliser le processus de digestion. Cette société dispose en effet d’une longue expérience de méthanisation en voie sèche continue, un procédé qui permet notamment une hygiénisation naturelle du digestat, ce qui est reconnu par les autorités sanitaires de nombreux pays européens mais pas encore en France. Chez Cometh, c’est le compostage du digestat qui garantit l’hygiénisation. La réalisation du processus de compostage et le traitement d’air vicié ont quant à eux été confiés à une entreprise qu’Edouard Leledy connaît bien, Biovalis, et qui a déjà équipé sa première entreprise, Leledy Compost.
Un bâtiment de stockage de 5000 m³ de capacité accueille les intrants solides dans cinq travées séparées par des murs en béton de 5 m de haut et où sont entreposés séparément les différents produits. De là, un grappin vient automatiquement se servir selon un programme prédéfini pour alimenter la trémie d’incorporation située à l’intérieur du bâtiment, et ce 24 h/24 sans intervention humaine. Une seconde trémie de chargement à remplissage par chargeuse a été placée en secours à l’extérieur du bâtiment. Une sixième travée est disponible pour les déchets ponctuels, avec alimentation du digesteur par chargeuse depuis une trémie extérieure, trémie qui fait également office de système de remplissage de secours. Le déchargement des solides se fait portes fermées dans le bâtiment en dépression.
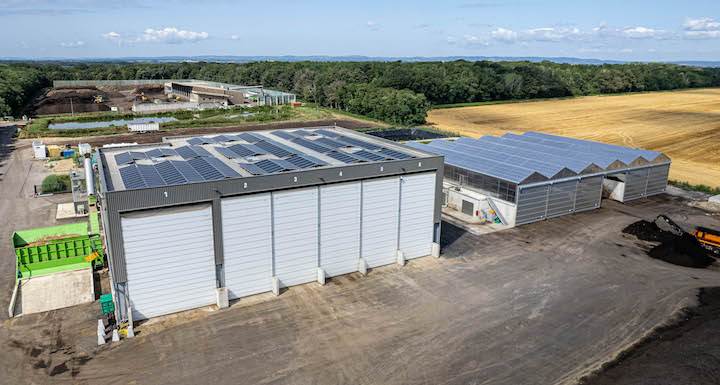
Le bâtiment des solides et celui des compodômes, photo Jean Marc Baudet
Après passage au broyeur, les produits liquides sont quant à eux stockés dans trois fosses en béton de 210 m³ situées à l’intérieur d’un second bâtiment, celui du compostage. Celui-ci est composé de six travées couvertes d’une toiture en polycarbonate. Ce bâtiment présente deux parties : l’une accueille les cuves d’intrants liquides, les presses et le stockage des jus ; l’autre accueille la zone de mélange du digestat avec le structurant, et les casiers de compostage avec ventilation forcée, les compodômes.
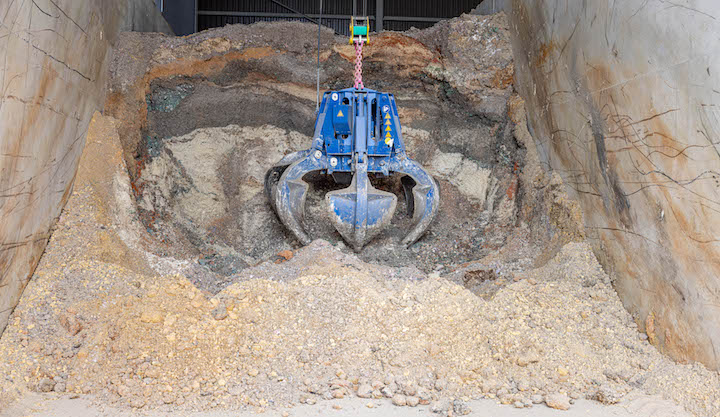
Le grappin dans une cellule de stockage, photo Jean Marc Baudet
L’air des deux bâtiments est aspiré à raison de 74 000 m³/h. L’air du stockage des intrants liquides, celui de la séparation de phase et du digestat solide, celui de l’aire de mélange et du compostage, passent dans une tour de lavage acide puis dans deux biofiltres remplis de matière filtrante capable de neutraliser les éléments soufrés. L’air du stockage des solides passe quant à lui uniquement dans les bioflitres.
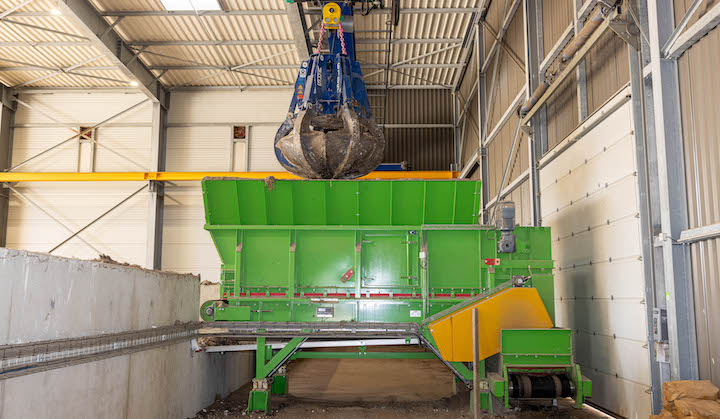
Le grappin chargeant la trémie du digesteur, photo Jean Marc Baudet
Un digesteur piston d’un volume de 2 100 m³ permet de produire 540 Nm³ de biogaz par heure, un biogaz à 64 % de CH4, un taux particulièrement élevé dû à la forte contribution des biodéchets facilement et rapidement dégradables ! Le biogaz est stocké dans un gazomètre de 4 000 m³ situé au-dessus de la cuve de digestat liquide de 2 000 m³.
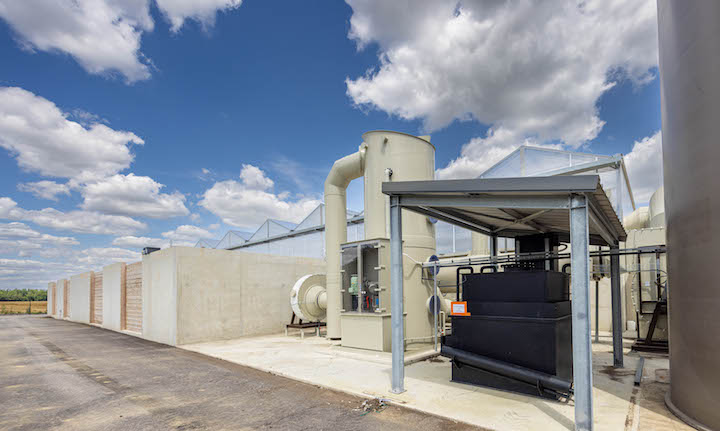
La tour de lavage acide de l’air vicié et les biofiltres, photo Jean Marc Baudet
Ensuite, le digestat brut va emprunter deux circuits possibles. Une partie est compostée directement. L’autre partie passe successivement deux fois au séparateur de phase pour en extraire un digestat liquide qui est utilisé en recirculation dans le digesteur pour dilution et ensemencement.
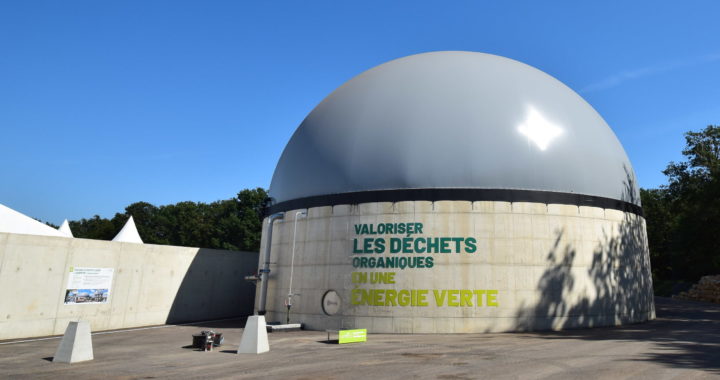
La cuve de digestat liquide et le gazomètre, photo Frédéric Douard
Le biogaz est épuré par filtration membranaire avant de rejoindre le poste d’injection GRDF qui a été raccordé au réseau de Chalon-sur-Saône par une conduite de 5,5 km dont le coût a été pris en charge à 60 % par GRDF. Pour finir, le digestat est transformé en compost normé et l’installation ne nécessite aucun plan d’épandage, car le produit est commercialisé.
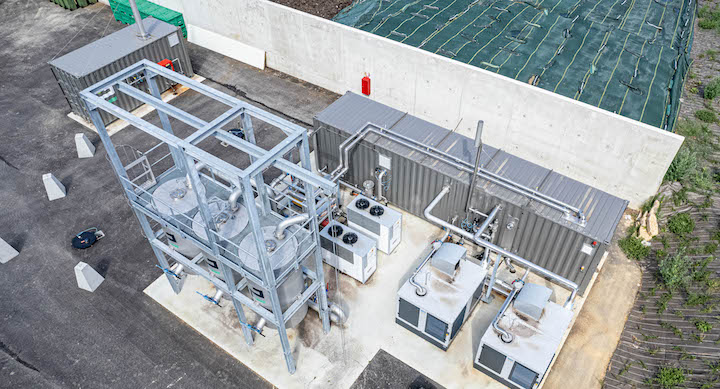
Le module de purification du gaz, Jean Marc Baudet
Le site fonctionne avec six salariés qui assurent la réception des matières, les maintenances quotidiennes, mais aussi la collecte des biodéchets solides dans des caisses en plastique avec un camion dédié. La raison de cette activité est qu’aucun prestataire local n’a pu être identifié pour réaliser cette tâche qui mobilise deux personnes.
Les flux de matières
L’unité valorise à ce stade 24 000 tonnes de matières organiques par an. La ration annuelle est actuellement composée de 2 000 t de fumier, 1 000 t de CIVE, 1 500 t de déchets de céréales, et 19 500 t de biodéchets dont 30 % liquides (déchets agro-industriels, soupes de déconditionnement et restes alimentaires collectés dans la région). Avec les 30 tonnes de digestat liquide recirculées quotidiennement, le digesteur incorpore près de 100 tonnes par jour.
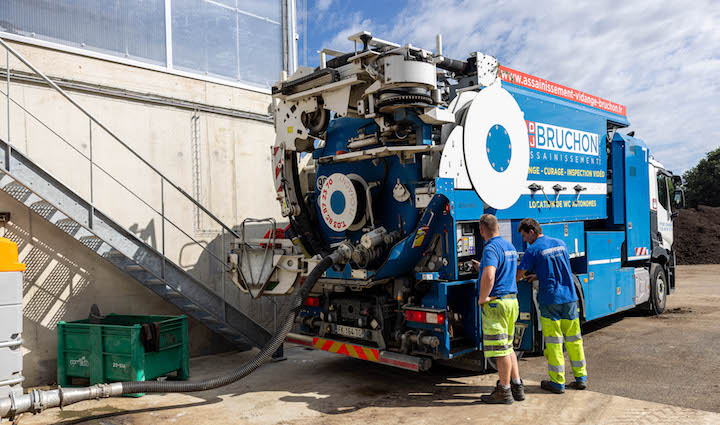
Livraison d’intrant liquide, photo Jean Marc Baudet
La digestion génère 20 000 tonnes de digestat brut par an, ce qui donne 15 000 tonnes de compost par an avec les 3000 tonnes de déchets verts incorporés comme structurant. La tour de lavage acide produit également un fertilisant, car elle transforme le gaz ammoniac – NH3 – présent dans l’air vicié en sulfate d’ammonium – (NH4)2SO4 – , un engrais normé NFU 42-001 et commercialisé (200 m³/an).
La production annuelle de biogaz est de 4 250 000 Nm³, ce qui permet d’injecter 2 720 000 Nm³ de biométhane par an, soit une capacité d’injection de plus de 300 Nm³/h.
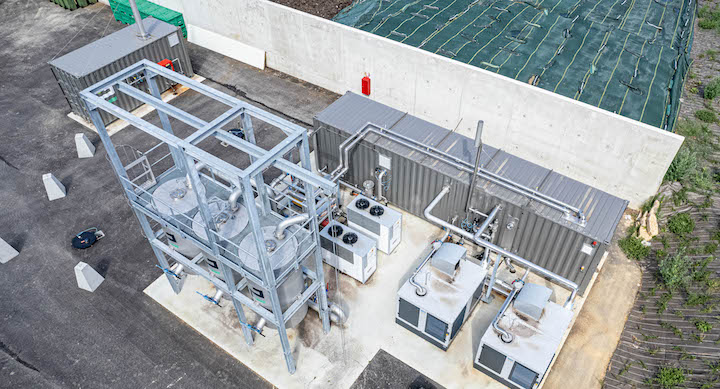
Le module de purification du gaz, Jean Marc Baudet
Cette production annuelle de méthane (27,2 GWh PCI) correspond à la consommation annuelle moyenne de 4500 logements neufs.
La technologie de digestion en voie pâteuse
Le digesteur est un Strabag LARAN® TF 2100. Il fonctionne en voie pâteuse sur le principe d’un flux séquentiel dans une cuve horizontale en béton coulée sur place. Il est équipé de sept arbres brasseurs transversaux massifs à rotation lente de 8,5 m de long. Ils sont là pour empêcher la formation de couches flottantes et sédimentaires, et permettent le dégazage de la matière vers un ciel gazeux.
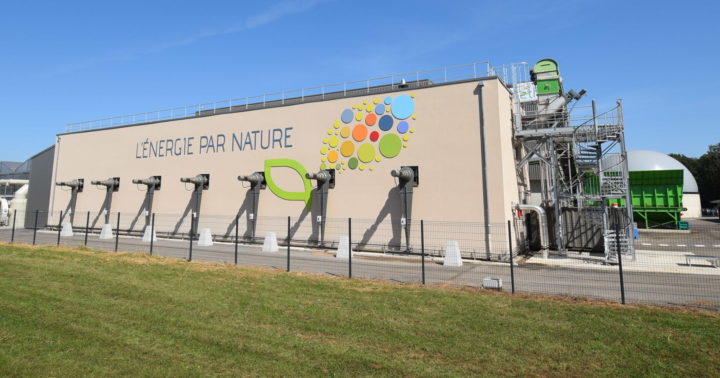
Le digesteur à flux piston de Cometh, photo Frédéric Douard
L’alimentation et l’extraction du digesteur sont situées respectivement à ses deux extrémités. L’introduction des solides est réalisée par une vis inclinée qui est alimentée par des convoyeurs à bande depuis la trémie d’incorporation. Des prises directes dans le digesteur apportent les liquides sans pré-mélange.
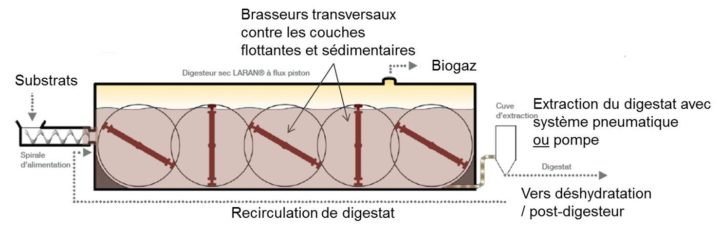
Principe du digesteur sec LARAN® à flux piston
Les brasseurs mélangent la matière à intervalles réguliers avec des rotations lentes d’environ un tour/minute. Ils sont actionnés automatiquement de manière successive. Une rotation alternative de chaque brasseur vers l’avant puis vers l’arrière prévient d’éventuelles perturbations de l’effet piston. Ainsi, ce ne sont pas les brasseurs qui font avancer la matière mais l’alimentation et l’extraction. La matière traverse le digesteur dans sa longueur en 21 jours. Le taux de matière sèche dans le digesteur Cometh se situe entre 27 et 30 %.
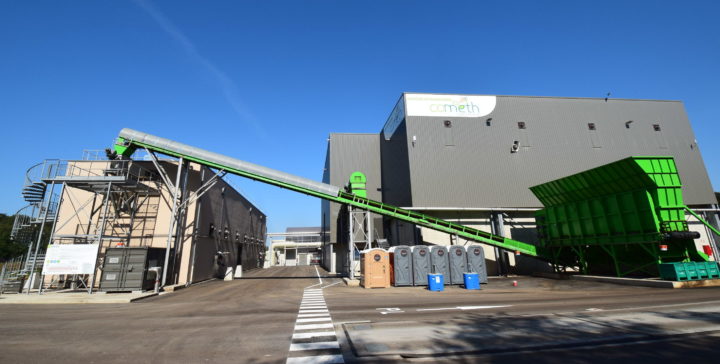
Alimentation du digesteur par la trémie extérieure, photo Frédéric Douard
Le digesteur LARAN® est chauffé par un réseau de chauffage intégré dans les parois et le sol en béton, et alimenté par une chaudière à biogaz de 270 kW. Chez Cometh, un régime mésophile à 42 °C a été choisi afin d’assurer une bonne stabilité de la microflore bactérienne.
Le vidage du digesteur s’effectue à son extrémité par quatre prises d’extraction de grandes dimensions, prévenant tout colmatage éventuel, et reliées à un système d’extraction pneumatique. Les prises sont situées en partie basse et permettent d’extraire la matière en évacuant simultanément les sédiments lourds. Le système d’extraction fonctionne selon le principe de l’aspiration et du refoulement via une cuve : une pompe à vide crée le vide dans la cuve, l’ouverture des vannes d’extraction permet l’aspiration du digestat vers la cuve. Celui-ci est ensuite évacué vers l’étape de post-traitement par une surpression mise en œuvre par un compresseur. Ce système d’extraction et de transport permet un haut niveau de disponibilité et une faible usure : le compresseur ou la pompe à vide sont des équipements à maintenance simple et aisément remplaçables ; en aucun cas la matière n’entre en contact avec des éléments électromécaniques ; et le principe d’alimentation prévient tout risque de bouchage des conduites à cause de matériaux de trop grande taille.
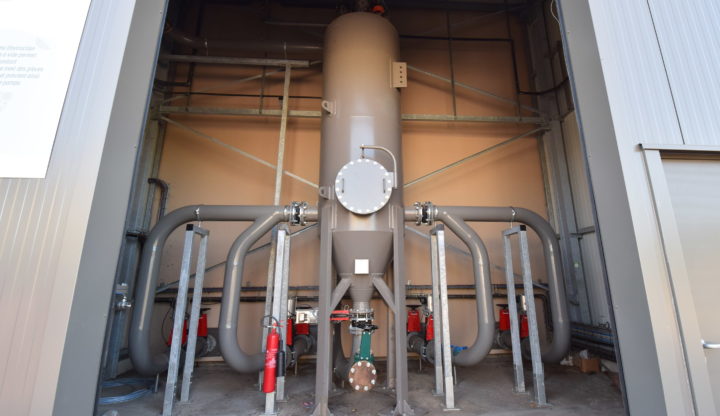
Le dispositif d’extraction par pompe à vide du digesteur, photo Frédéric Douard
Cometh est le septième digesteur Strabag en France, et parmi les dernières références, on peut citer Biogaz d’Arcis à Ormes dans l’Aube et chez Cap Vert Bioenergie de Breuilh à Saint-Antoine-de-Breuilh en Dordogne.
Le compostage
Les digestats brut et solide sont mélangés à du déchet vert broyé qui fait office de structurant. Il est composté en andains dans les compodômes et au bout de quatre semaines, le compost est criblé pour en ôter le structurant résiduel qui repart dans le circuit. Le produit obtenu (15 000 t /an) est normé NFU 44-051 sous la marque Organic et est commercialisé par la Coopérative Bourgogne du Sud après vérification de conformité à la norme. Ce volume permet d’amender 3 000 ha de cultures par an.
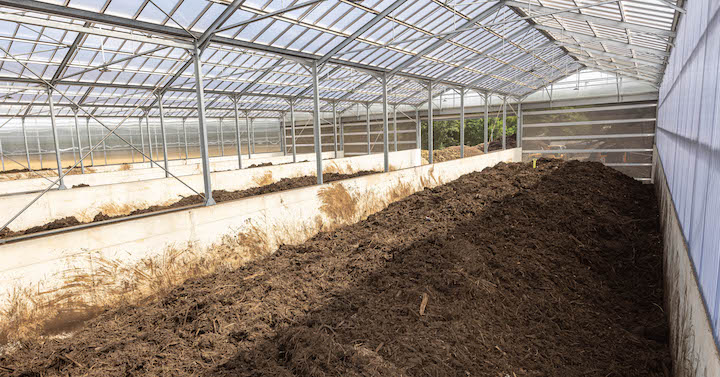
Les compodômes, photo Jean Marc Baudet
L’avantage de ce post-traitement du digestat par compostage est qu’il assure l’hygiénisation des matières d’un point de vue sanitaire. Dans un procédé classique en voie liquide, les sous-produits animaux doivent être hygiénisés en amont de la méthanisation. Les matières doivent donc être préalablement préparées pour être pompables et être transférées dans une cuve d’hygiénisation avant méthanisation. Cette opération nécessite d’avoir un mélange avec un taux de matière sèche relativement bas. Le procédé Cometh permet de valoriser des sous-produits animaux avec un taux de matières sèches élevé, sans avoir à ajouter de liquide.
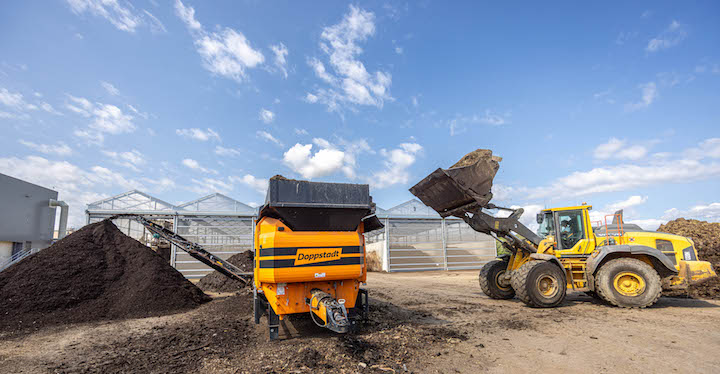
Le criblage du compost, photo Jean Marc Baudet
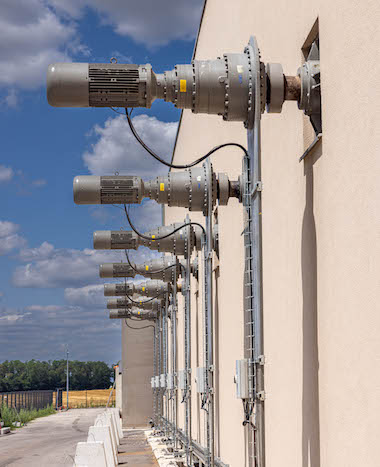
Les moteurs des agitateurs du digesteur à flux piston de Cometh, photo Jean Marc Baudet
Contacts :
- Cometh : Edouard Lelédy – 06 75 29 55 91 – contact@cometh-biomethane.fr – www.cometh-biomethane.fr
- Méthanisation : Line Speckin – 06 70 67 22 28 – line.specklin@strabag.com et Benjamin Douzouer – 07 66 72 66 22 – benjamin.douzouer@strabag.com – www.strabag-umwelttechnik.com
- Distribution du gaz Bourgogne Franche-Comté : Eric Passetti – 03 80 54 26 41 – eric.passetti@grdf.fr – www.grdf.fr
- Compostage et traitement d’air : 03 85 75 75 90 – www.biovalis.fr
- Épuration : www.prodeval.com
- Analyse du biogaz : www.sewerin.com
- Gazomètre : www.biogasmembrane.com
Frédéric Douard, en reportage à Allériot
Voir également une vidéo de la construction en accéléré :
ℹ️ Le magazine Bioénergie International est disponible :
- Au détail
- Dans le cadre d'un abonnement