La plus ancienne usine française de méthanisation de déchets ménagers a été mise en service à Amiens en 1988
Article paru dans le Bioénergie International n°55 de mai-juin 2018

L’usine de méthanisation d’Amiens, photo Frédéric Douard
Le début de l’histoire du tri et de la valorisation des déchets ménagers en France s’est écrite à la fin des années 80 dans les Hauts-de-France. À cette époque, alors que la surconsommation des biens a déjà fait déjà rage, le pays met alors encore sans scrupule l’ensemble de ses déchets dans les décharges ou les incinérateurs sans les trier et sans aucune récupération d’énergie. Il n’y a alors guère que le verre qui a commencé à être récupéré dès 1974 au bénéfice de la Ligue contre le cancer dans l’Est de la France. C’est à Amiens qu’apparaît la première initiative de taille industrielle, en 1988, avec la mise en service de l’usine de méthanisation d’Amiens. Suivra l’année suivante la mise en place du premier tri sélectif en France par la Communauté Urbaine de Dunkerque, à une période pourtant où les questions d’environnement et d’économie d’énergie voguaient plutôt à contre-courant. Trente ans après, ces deux réalisations ont fait école et sont toujours là pour témoigner de la pertinence de ces choix. D’ailleurs, lorsque le projet d’Amiens est sorti, votre serviteur se souvient fort bien de l’agitation qui avait gagné l’opinion et les médias face à cette « usine à gaz qui ne marcherait jamais » … l’Histoire a donné raison à ces pionniers de bonne volonté.
L’oeuvre de pionniers
L’usine de méthanisation d’Amiens est construite sur la base d’une technique à l’époque toute nouvelle inventée par un collectif de personnes fortement investies sur le sujet et travaillant respectivement dans le bureau d’étude coopératif C.A.R.E.N.E. et dans le laboratoire de génie chimique de l‘université de Montpellier. La coopérative C.A.R.E.N.E. avait été créée en 1979 par des personnes de formations et d’expériences diverses dans les domaines de l’architecture, de l’énergie et de l’environnement. Les brevets déposés suite aux premiers travaux de recherches entrepris dès 1981 ont permis la mobilisation de partenaires et de moyens qui ont été valorisés au sein de la Sté Valorga pour mettre en oeuvre le procédé au niveau industriel. Ces recherches ont bénéficié de l’aide de l’ANRED (Agence des déchets), de l’ANVAR et de l’AFME (ancêtre de l’ADEME avec l’ANRED), tout en mobilisant les capitaux nécessaires pour tenir sept années en recherche.
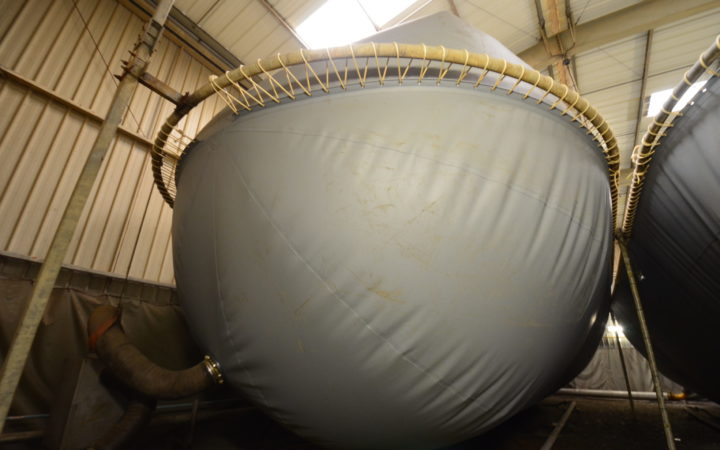
L’un des deux gazomètres tampons à l’usine de méthanisation d’Amiens, photo Frédéric Douard
La première réalisation commerciale qui s’est concrétisée à Amiens en 1988 fut une première mondiale pour une installation en voie sèche en continu sur déchets ménagers. Elle repose sur une injection séquentielle et sectorielle de biogaz sous pression dans le digesteur afin de brasser une matière épaisse qui grâce à l’hydrolyse peut s’écouler dans un couloir. Le projet d’Amiens a permis un saut technologique important car il s’agissait de réaliser une chaîne de tri d’ordures ménagères brutes pour récupérer 60 % de la matière fermentescible pour la digestion dans trois digesteurs de 2 400 m³. A la mise en service, les concepteurs ont rencontré de nombreuses difficultés qui ont duré plus de six mois. Ce fut la panique chez les actionnaires de Valorga et dans les collectivités locales. Le dépôt de bilan suivit et Valorga fut reprise par GDF, IDEX et Spie Batignolles. L’usine d’Amiens fut ensuite progressivement optimisée et aujourd’hui, elle fonctionne très bien.
Amiens, Idex et la méthanisation, une longue histoire d’amour
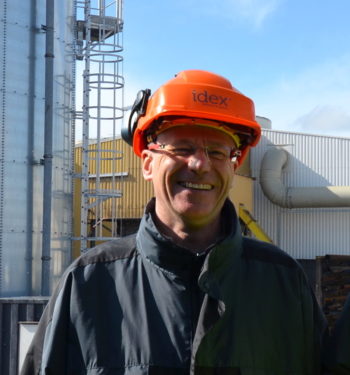
Gontran Delamaere, directeur de l’usine de méthanisation d’Amiens, photo Frédéric Douard
Idex, l’un des groupes spécialisés dans les services à l’énergie et à l’environnement en France, est en charge de l’usine de méthanisation de déchets ménagers, déchets verts et BioDIB d’Amiens depuis 1990 sans interruption, après un peu plus d’un an d’exploitation par la Sotradep-Valorga. Devenu actionnaire de l’usine suite à la faillite de Valorga, Idex a remporté une DSP de 25 ans jusqu’en 2015, et renouvelé pour une nouvelle DSP de cinq ans.
Depuis 1990, le déléguant, aujourd’hui devenu la communauté d’agglomération Amiens Métropole, et Idex Environnement Picardie, n’ont eu de cesse de maintenir, d’améliorer, d’enrichir et d’agrandir cet équipement. L’une des preuves de cette bonne dynamique est l’excellente productivité de biogaz de l’installation avec 130 Nm³ par tonne de biodéchets, un record dans la profession ! En fait, le secret de cette performance par rapport aux autres CVO, et l’exploitant a précieusement continué à le maintenir, c’est la forte proportion de matière organique et de plastiques dans le mélange en digestion. Ces plastiques servent en effet de structurant et de support aux bactéries. Bien sûr, ils sont ensuite écartés de la chaîne de valorisation compost, mais trouveront peut-être un jour un débouché.
L’usine valorise aujourd’hui chaque année 65 000 tonnes d’ordures ménagères résiduelles, 20 000 tonnes de biodéchets IAA et alimentaires, et 15 000 tonnes de déchets verts. Elle produit 12 millions de Nm³ de biogaz par an transformés en 19 GWh d’électricité et en chaleur.
Des installations qui évoluent selon les impératifs environnementaux et de valorisation
Le long processus commence par deux chaînes de tri mécano-biologique : broyage rapide, crible rotatif qui sépare les organiques des matières indésirables pour la digestion, séparateur de ferreux, tables de tri balistique pour ôter les cailloux, céramiques et verres. La matière organique passe ensuite dans un malaxeur où elle est réchauffée et ensemencée avec du digestat avant d’être poussée vers les digesteurs.
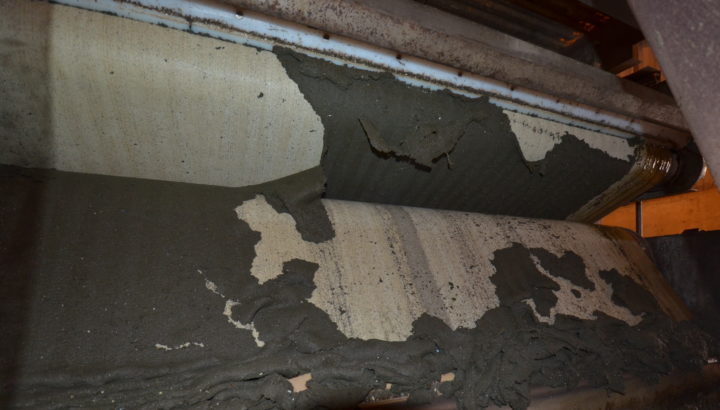
Sortie de presse du gâteau de digestat, photo Frédéric Douard
Après trois semaines de digestion, le digestat est pressé sur un tapis textile qui passe entre des rouleaux. Ce pressât humide, qui contient désormais principalement des plastiques, les fermentescibles ayant été digérés, est dirigé vers un sécheur alimenté par de l’air chauffé à partir de la chaleur de cogénération. Ce pressât part aujourd’hui en ISDND.

Le gâteau de digestat solide de l’usine de méthanisation d’Amiens, photo Frédéric Douard
Le jus de pressage du digestat, qui outre de l’eau contient une petite fraction de matière organique non décomposée dans les digesteurs, passe dans des filtres à bande pour sa déshydratation. De ces filtres sort un gâteau de filtration et un jus clair. Le jus clair va servir à humidifier les matières entrant dans le processus et son surplus sera épandu sur des exploitations agricoles dans le cadre d’un plan d’épandage.
Les 20 000 tonnes de gâteau de filtration produits chaque année sont mélangés avec des déchets verts broyés puis maturés en compost normé sur une plateforme externalisée.
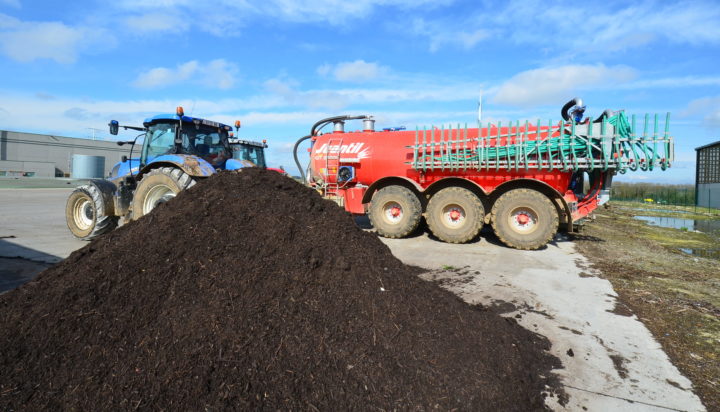
Le compost normé obtenu à partir du gâteau de digestat liquide et de déchets verts, et épandeur de jus clair, photo Frédéric Douard
Concernant le parcours du biogaz, au sortir des digesteurs, il est stocké temporairement dans deux gazomètres de 500 m³ suspendue dans un bâtiment Atex. Ensuite, il est séché et désulfurisé avant d’alimenter les deux moteurs de cogénération GE Jenbacher produisant chacun 1 415 kWé et 1 385 kWth et mis en place en 2009 par Clarke Energy.
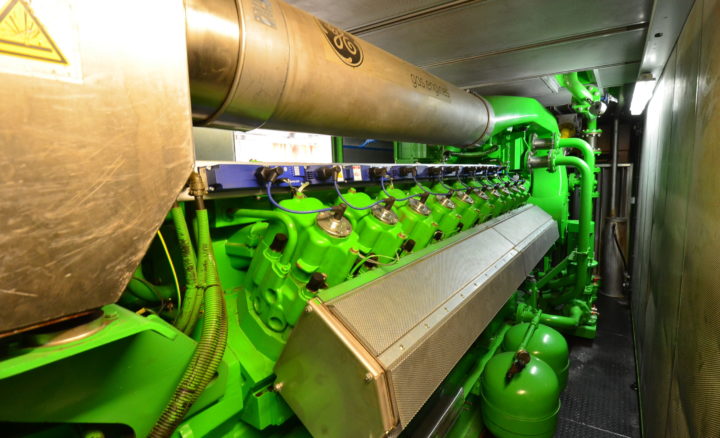
L’un des deux moteurs de cogénération GE Jenbacher de 1415 kWé à l’usine de méthanisation d’Amiens, photo Frédéric Douard
Avant 2009, c’est une chaudière à vapeur de 5,5 MW qui valorisait le biogaz pour le chauffage des processus, pour le maintien des bâtiments de l’usine au-dessus du point de rosée et pour la fourniture de vapeur à un industriel voisin. Cette chaudière existe toujours et peut être appelée en complément des moteurs ou lors de leur maintenance.
Depuis que la cogénération a été installée, l’usine alimente aussi en vapeur la station d’épuration d’Ambonne ainsi que l’industriel voisin via deux réseaux de chaleur, pour une quantité annuelle de 9 GWh.
Les derniers investissements en 2015 : un nouveau sécheur de pressât et deux nouveaux dispositifs de traitement d’air
Un sécheur SCOLARI, qui remplace un équipement antérieur et qui utilise l’énergie thermique provenant des moteurs de cogénération, a été installé en 2015. Il permet de déshydrater les déchets non fermentescibles en sortie de digesteur, à savoir le pressât. L’opération permet d’en réduire la quantité d’eau de 50 à 10 %, et surtout de réduire le tonnage à enfouir et donc les redevances qui s’exercent au poids. Par la suite, cela ouvre la porte à une valorisation énergétique possible de ce produit désormais enrichi en énergie et qui s’apparente à un CSR.
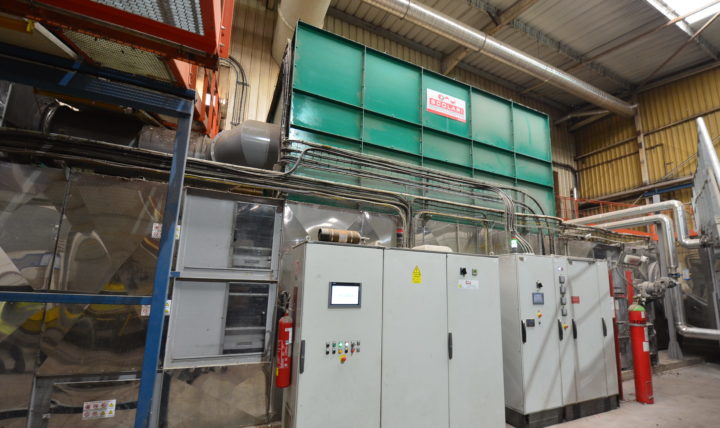
Le sécheur de CSR à l’usine de méthanisation d’Amiens, photo Frédéric Douard
Ce sécheur a été fourni clé en main avec garanties d’assèchement, et avec tous les équipements de sécurité pour un fonctionnement autonome automatisé, dont un dispositif de protection incendie et d’extinction par aspersion des points chauds. Il est ainsi exploité 24 h/24 sans présence humaine. Il utilise l’air vicié capté par le réseau de captation des bâtiments de tri et de séparation mis en dépression. Il dispose de deux plans de séchage métalliques et superposés de 24 par 3 mètres, est entièrement calorifugé, et est équipé des périphériques suivants : un modem de programmation et maintenance à distance, un tapis-trémie tampon d’alimentation, un dispositif de nettoyage automatisé, un échangeur thermique calorifugé avec dispositif de régularisation de la pression de l’air injecté. Compte tenu de la siccité très basse du produit obtenu, il a été fait le choix d’un dépoussiérage cyclonique de l’air de séchage, intégré au sécheur, avec une garantie des rejets inférieure à 20 mg/Nm³ d’air.
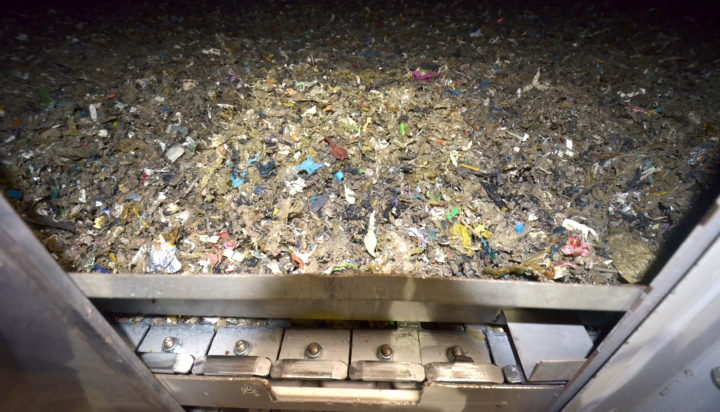
Le tapis de séchage du pressât de CSR dans le sécheur, photo Frédéric Douard
L’air de séchage est ensuite traité successivement dans une tour de lavage acide à média statique pour abattre l’ammoniac, et dans un biofiltre. Ce dispositif de traitement d’air a été conçu et réalisé par la société GALLI ALDO dans le cadre de prescriptions très contraignantes. Le média du biofiltre est constitué par de la bruyère broyée qui développe une activité micro-organique importante tout en offrant un faible degré de dégradation et une longue durée de vie. Ce dispositif, a une capacité de traitement de 60 000 m³/heure, ce qui correspond au débit d’air du sécheur.
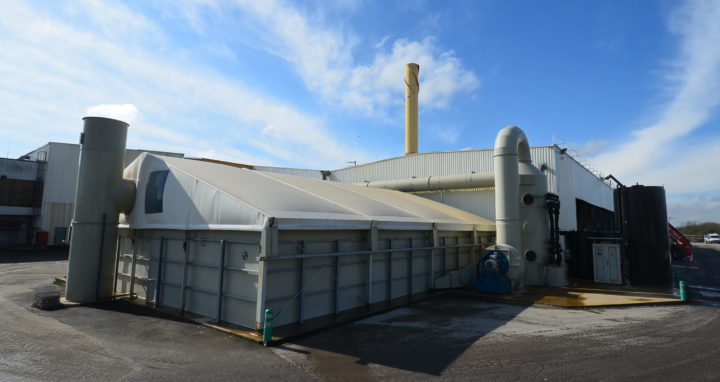
Le bioflitre traite l’air sortant du sécheur de CSR de l’usine de méthanisation d’Amiens, photo Frédéric Douard
En 2015, GALLI ALDO a également réalisé un système de captation et de traitement d’air spécifique pour la zone de dépotage et de broyage primaire des OMR. Ce traitement d’air est constitué d’un laveur à l’hypochlorite pour abattre les odeurs. Le laveur à média flottant est constitué de petites balles en plastique mises en suspension par l’air et est recommandé pour le traitement de l’air chargé en particules. La mise en mouvement du média favorise en effet un nettoyage permanent, les particules sont abattues par l’eau et décantées dans le bac inférieur.
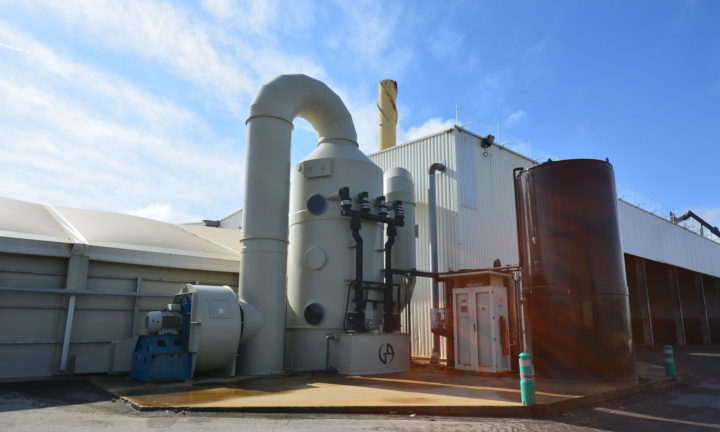
Le laveur acide à média statique en amont du biofiltre, photo Frédéric Douard
30 ans et l’avenir devant elle
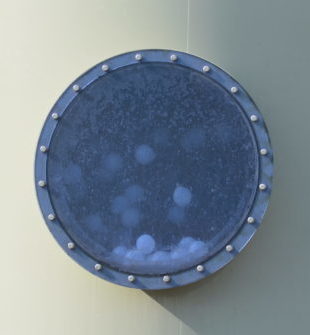
Le média flottant du laveur acide, photo Frédéric Douard
L’usine de méthanisation d’Amiens est la plus vielle du genre en France et même au-delà, mais un suivi attentif depuis 30 ans, motivé par une volonté locale, par des réglementations qui évoluent et par de la recherche permanente d’efficacité promettent à cet équipement modèle, non seulement de rester dans la course, mais de continuer à le faire en tête avec une belle longueur d’avance sur (beaucoup) d’autres collectivités.
Contacts :
- Usine de méthanisation d’Amiens : Idex Environnement Picardie – 03 22 67 34 00 – contact-uve@idex.fr
- Sécheur : www.scolarisrl.com
- Traitement d’air : www.gallialdo.it
- Cogénération : www.clarke-energy.com
- Filtre biogaz à charbon actif : www.desotec.com/fr/
- Pompe à digestat : www.putzmeister.com
Frédéric Douard, en reportage à Amiens
ℹ️ Le magazine Bioénergie International est disponible :
- Au détail
- Dans le cadre d'un abonnement