Près d’Angers, HoSt démontre la viabilité de la microméthanisation avec Microferm
Article paru dans le Bioénergie International n°38 de août-septembre 2015
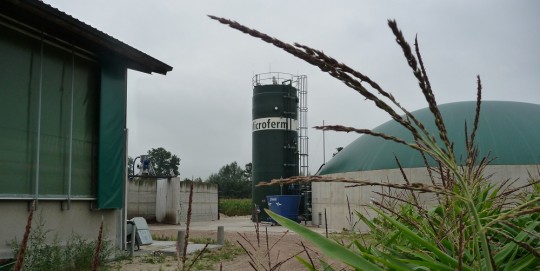
Installation Microferm à Ochtrup en Allemagne
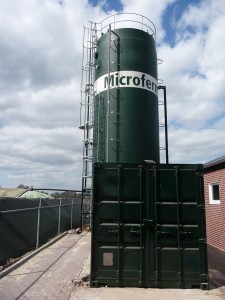
Digesteur Microferm à Langeveen aux Pays-Bas, photo HoSt
La société néerlandaise HoSt réalise depuis presque 20 ans des unités de méthanisation de toutes tailles et traitant des substrats extrêmement variés comme les lisiers, fumiers, pailles, effluents agro-alimentaires, boues, sang. L’entreprise étant présente dans plus de 15 pays européens, elle cherche toujours à s’adapter au contexte local et à ses particularités. Quand en 2008-2009, HoSt décide de réaliser aux Pays-Bas la première unité de petite méthanisation, qui deviendra Microferm, la société ne se doute pas qu’elle va ouvrir une voie pour le développement d’un certain type de micro-méthanisation fort attendu en France, un pays qui compte encore une majorité d’élevages agricoles de taille familiale.
Une crédibilité qu’il a fallu démontrer
En France la microméthanisation attire mais suscite aussi parfois des craintes. Dans le contexte de méfiance envers les gros projets qui exigent des mises de fonds et des quantités de matières importantes, qui cristallisent parfois aussi les foudres d’opposants de tous poils, les petits projets font figures de projets raisonnables, à taille humaine et ne nécessitant pas des transports importants de matières. Et d’un autre côté, comment peut-on croire en de petites unités rentables alors que certains gros projets rencontrent des difficultés à trouver l’équilibre ?
En janvier 2010, HoSt a mis en service donc sa première unité Microferm à Laangueveen aux Pays-Bas. Sur une ferme d’engraissement de bovins sur lisier, une tour de méthanisation de 12 mètres de hauteur y traite le lisier collecté quotidiennement et le transforme en biogaz, lui-même converti en électricité (54 kWé) et chaleur. Depuis cette date, le modèle a essaimé dans le pays, puis en Allemagne avec plusieurs variantes, avant d’arriver en France en 2013. Immédiatement le concept d’une unité automatisée fonctionnant avec 100% d’effluents a séduit.
Cependant, dans le contexte d’interrogation entourant la méthanisation en général et la petite méthanisation en particulier, l’Ademe a décidé de s’emparer du dossier en demandant le suivi précis d’un projet durant un an. Retenu parmi sept projets portés par sept constructeurs, le couple GAEC des Buissons (à Saint-Lambert-La-Potherie près d’Angers) & HoSt France (la filiale française créée entre temps) a commencé la construction de son projet. Si le chantier n’a été qu’une formalité, les tribulations du raccordement électrique ont définitivement effacé l’espoir d’un délai de moins de sept mois entre la signature du marché et la mise en service… Mais qu’à cela ne tienne, l’unité dont la construction a débuté en juin 2013 a été mise en service en février 2014.
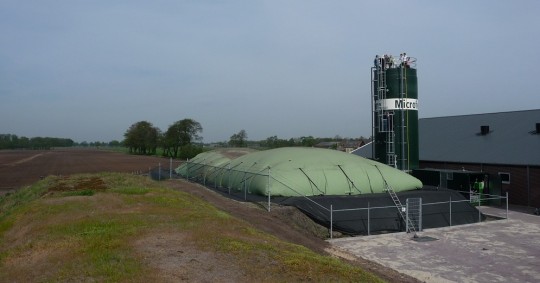
Intsallation Microferm à Langeveen aux Pays-Bas, photo HoSt
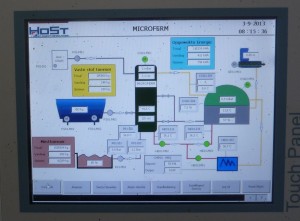
Ecran de commande HoSt à Ochtrup, photo HoSt
Le suivi Ademe a été délégué au bureau d’étude S3D, qui avec l’exploitant et le constructeur, a tout enregistré, noté, mesuré, analysé pendant un an :
- Les intrants (lisier pailleux + eaux de salle de traite) ont été échantillonnés pour comparer les résultats en matière de production méthanogène entre la théorie et la réalité,
- Les productions de biogaz (quantité, qualité) suivies,
- La production d’électricité et de chaleur brutes et nettes comptabilisées,
- Le temps de travail de l’exploitant chronométré,
- Les investissement et les coûts de fonctionnement comparés au plan d’affaires.
Au vu des résultats S3D a remis ses conclusions à l’Ademe qui a pris la décision de valider le système Microferm.
Production de biogaz en dix jours avec une charge organique de 10 kg/m³/jour
Avant cette première réalisation en France, l’idée de produire du biogaz avec uniquement du lisier avec un temps de séjour de 8-12 jours et une charge organique supérieure à 10 kg/m³/jour ne paraissait pas crédible et frôlait même l’escroquerie dans les esprits. Malgré cela, le constructeur, fort de son expérience, et le GAEC, convaincu par ses visites, sont restés confiants. HoSt a ainsi réussi à démontrer qu’il était possible de faire fonctionner une unité de méthanisation dans ces conditions, n’en déplaise aux incrédules !
Le digesteur de 125 m³ utiles y reçoit quotidiennement 15 tonnes de lisier bovin avec menue paille (11% MS et MO/MS de 80%). Avec un chargement de 10,56 kg MO/m³/jour et un temps de séjour dans le digesteur de 8,33 jours, le pari a été gagné et montre qu’il est donc tout à fait possible de digérer le lisier de bovin sans entrer en acidose-alcalose à condition de garantir l’excellence du brassage. Signalons tout de même qu’une fosse existante de 500 m³ transformée en post-digesteur permet de sécuriser le système.
Une production méthanogène à hauteur de 97% de la valeur théorique
Il était aussi capital de vérifier que le système non seulement fonctionnait bien d’un point de vue biologique mais aussi que la production de biogaz était à la hauteur des attentes du client. Ainsi avec 97 % du potentiel méthanogène mesuré en laboratoire. Le taux de dégradation de la matière organique se situe entre 54 et 56 % et la production de biogaz entre 445 et 450 Nm³ de biogaz / tonne de matière organique entrante.
Si la production de méthane est satisfaisante, on pouvait craindre que la biologie soit fragile en raison d’un processus très intensif au sein du digesteur. Après plus d’un an de fonctionnement, le GAEC n’a connu qu’une d’une seule « sortie de route » que l’on pourrait qualifier d’excès de confiance avec une incorporation rapide et importante de déchets de pommes. Le phénomène d’acidose s’est déclaré après 15 jours et a été jugulé par une recirculation de digestat en 3 semaines.
De la préparation de la matière à la post-digestion, un processus optimisé
Les intrants, constitués à 67% de lisier pur et frais (11,5% MS) et à 26% d’eaux de lavage de robots (0,5% MS), de menues pailles et de refus d’aliments du cheptel, sont traités frais dans une préfosse où ils sont mélangés et broyés. Précisons que la menue paille est introduite dès le paillage du bâtiment afin de permettre un bon mélange avec le lisier le plus en amont possible.
Ce n’est qu’après cette phase préalable que l’alimentation dans le digesteur s’opère par cycles toutes les 20 minutes tout au long de la journée. Arrivée dans le digesteur au point haut la matière organique est maintenue dans le digesteur par un système de brassage axial (issu de l’expérience en méthanisation industrielle de HoSt) par une alternance de cycles horaires et anti-horaires jusqu’à sa dégradation. Ce système à faible consommation d’électricité (le brasseur est entrainé par un moteur de moins de 3 kWé) permet de garantir le temps de séjour dans le digesteur, de prévenir la sédimentation de la matière et la formation d’une éventuelle couche de flottation. Deux niveaux de sortie de la matière (point intermédiaire et point bas) permettent d’optimiser les temps de séjour en fonction de la matière incorporée.
Signalons que le système est équipé d’un système de détection et destruction de mousse en cas de dérive de la biologie.
Le post digesteur viendra parfaire l’extraction du biogaz (selon les estimations entre 5 et 7 % du biogaz total), stocker, homogénéiser le biogaz dans le gazomètre. Ce post digesteur chauffé permet en outre une élimination à moindre coût des excédents de chaleur en complément des aéroréfrigérants.
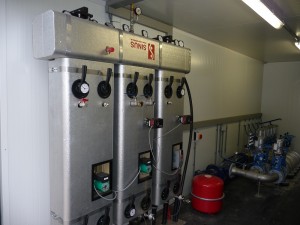
Local hydraulique à Ochtrup en Allemagne, photo HoSt
Un traitement du biogaz digne des plus grandes installations
La régularité du fonctionnement d’une installation dépend de la qualité du pré-traitement du biogaz avant combustion en moteur. Sur le système Microferm, un double système de désulfurisation (un biologique et un par filtre à charbon actif) permet d’obtenir des teneurs en H2S inférieures à 5ppm/Nm³. La déshumidification passive assure une prévention complète de l’arrivée d’eau liquide dans le bloc moteur : simple et efficace.
HoSt travaille depuis de nombreuses années avec le motoriste MAN. Sur des petites puissances, comme ici à 65 kWé, ces moteurs assurent une excellente valorisation du biogaz avec un rendement électrique (mesuré) de 35,1% et thermique de 47,3 %. Au GAEC des Buissons, la maintenance est assurée par le groupe Fauché.
Une valorisation de la chaleur qui peut encore être optimisée
La chaleur non utilisée par le processus est envoyée pour chauffer les 400 m² des 3 habitations du site avec 9 personnes et leur production d’eau chaude sanitaire, plus celle de l’atelier lait (eau de buvée des vaches, eau de lavage tank et robot de traite). Le coefficient d’efficacité énergétique n’est que de 56 mais le GAEC envisage prochainement soit un système de séchage de fourrage et/ou graine (le GAEC est producteur de semences fourragères) ou de réfléchir à la trigénération pour produire le froid du groupe lait. Dans ces deux cas le GAEC devra faire une croix sur le surplus de prime énergétique puisque hors délai au regard de la mise en service de l’unité. La souplesse dans la tarification de l’électricité reste encore à trouver !
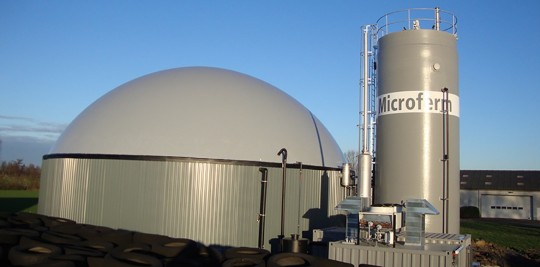
Installation Microferm de Well aux Pays-Bas, photo HoSt
Une économie qui repose sur des bases simples
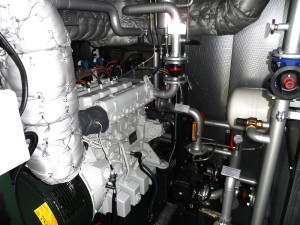
Le moteur de cogénération MAN de 65 kWé au GAEC des Buissons, photo HoSt
La question se pose toujours de savoir comment une unité de 65 kWé, payée à 608 000€ (projet complet hors subvention), peut arriver à un équilibre économique. Cette réalité repose sur divers facteurs évidents :
- Des intrants gratuits : la totalité des intrants sont à coût zéro : lisier, paille servant de litières, eaux de lavage etc…
- Un coût de main d’œuvre nul : pas de surplus de travail (et même moins comparativement à la situation anté-méthanisation). L’unité est entièrement automatisée.
- Pas de surcout de transport/épandage : les matières sont sur l’exploitation quoi qu’il en soit.
- Des coûts opérationnels limités grâce à des pompes brasseurs solides et économes.
- Une maintenance simple.
Malgré tous ces points forts qui permettent au GAEC d’envisager un retour sur investissement à 7,5 ans avec un prix de vente du KWhé de 0,18€ (l’Ademe et la Région Pays de la Loire ont apporté 37% de subvention sur les investissements), HoSt réfléchit encore pour optimiser sa solution.
Renforcer la standardisation des unités et surtout le taux de remplissage des unités. Avec 120 vaches laitières et pas de lisier de génisses car sur un autre site, le GAEC se situe dans la zone plancher du système. Les prochains projets sur des exploitations de 140 à 200 VL avec un investissement quasi identique à celui du GAEC (seul le moteur de cogénération sera un peu plus gros) vont optimiser cet investissement, ce qui permet d’envisager à terme un arrêt des subventions.
Pour HoSt qui souhaite transformer cet essai, l’enjeu est aussi de renforcer le partenariat avec des entreprises françaises afin d’offrir dans les années futures une solution made in France avec brevet néerlandais. Il paraîtrait ainsi que la prochaine tour de digestion Microferm sera fabriquée en France…
Première installation Microferm en France, l’exploitation du GAEC des Buissons est également démonstrateur de l’intérêt de la méthanisation dans le cadre des sentinelles de la terre© (développement des techniques pour une agriculture écologiquement Intensive®).
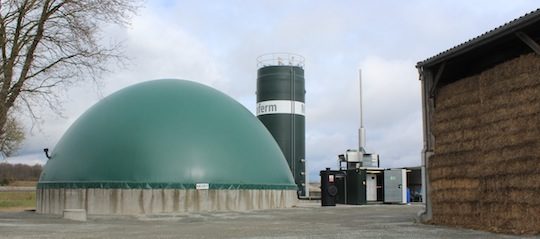
L’installation de méthanisation du GAEC des Buissons à Saint-Lambert-La-Potherie-49, photo HoSt
Contact : Jean Sébastien Tronc, HoSt France à 44110 Châteaubriant – Tel +33 244 05 53 90 – info@hostfrance.fr – www.hostfrance.fr
Télécharger la documentation MICROFERM
ℹ️ Le magazine Bioénergie International est disponible :
- Au détail
- Dans le cadre d'un abonnement