La fromagerie des Bergers du Larzac valorise ses rejets par la production de chaleur au biogaz
Article paru dans le Bioénergie International n°32 de juillet-août 2014
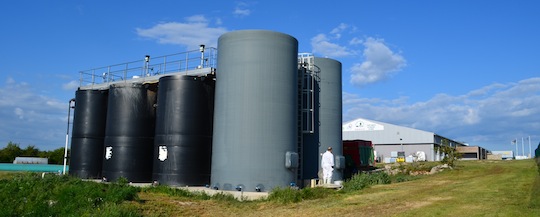
Les installations de méthanisation des Bergers du Larzac réalisées par Valbio, photo Frédéric Douard
Les besoins
Avant la mise en service de la méthanisation le 11 janvier 2010, les eaux blanches étaient rejetées dans le réseau communal des eaux usées et le lactosérum était épandu sur les terres des adhérents proches de la coopérative : ces deux pratiques se sont progressivement heurtées à des interdictions. Remarquons en passant que le lactosérum est une matière première qui peut être revendue pour déshydratation. Le problème est que sur le Larzac l’éloignement, mais aussi la saisonnalité du lait de brebis n’intéresse pas forcément les acheteurs. Pour ces deux effluents donc, des solutions locales étaient à trouver.
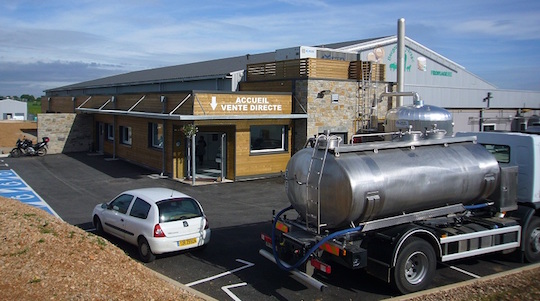
La fromagerie, photo Alliance 2 C, Maîtres d’oeuvre en bâtiment
Parallèlement à cela, la fromagerie a de forts besoins en énergie thermique pour le chauffage du lait, les bains marie des cuves à fromages, les solutions de lavage et la production d’eau chaude sanitaire. Et alors qu’une filière bois-énergie se mettait en place sur le causse du Larzac, une étude de faisabilité a été réalisée avec du bois-déchiqueté produit localement.
En 2009, les nécessités d’un agrandissement de la fromagerie et de la mise aux normes pour le rejet des eaux dans le milieu naturel, ont conduit à croiser l’ensemble des données : agrandissement et déménagement sur un site hors de l’agglomération, épuration des eaux blanches, valorisation du lactosérum et production de chaleur.

L’atelier de production construit en 2009, photo Frédéric Douard
La faisabilité économique de la production de chaleur a été comparée entre le bois et le gaz (gaz naturel disponible sur la commune + biogaz). La faisabilité de différentes valorisations du sérum a aussi été comparée avec son épuration aérobie ou anaérobie avec production de biogaz. Et c’est la solution méthanisation + gaz naturel (profitant des offres plus avantageuses dues à l’ouverture du marché) qui s’est avéré la plus pertinente économiquement car elle apportait une réponse à la fois au traitement des liquides et à la fourniture d’énergie par la production de biogaz. La solution bois a été écartée car elle obligeait à doubler les équipements : une chaufferie et une station d’épuration sans valorisation.
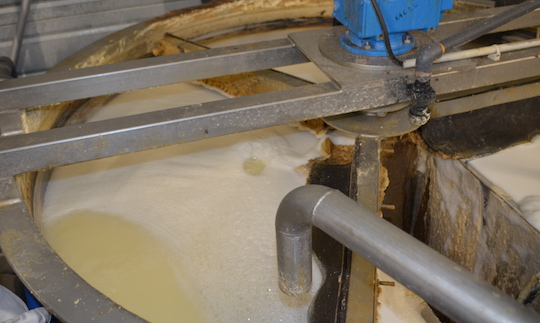
Bassin d’arrivée des rejets à traiter, photo Frédéric Douard
Notons dans la comparaison station d’épuration et méthanisation, que la solution anaérobie permet de diviser par 15 la quantité de boue produite à l’épuration par rapport à une station aérobie. Et en voie aérobie, l’évacuation de ces boues aurait représenté une charge non négligeable dans cette zone de quartz particulièrement sensible à la pollution des eaux. De plus, les procédés de traitement aérobie sont très largement plus énergivores en électricité.
Les équipements
Les effluents, 1,3 M litres de sérum et 5,5 M litres d’eaux blanches par an, sont collectés dans une cuve enterrée de 45 m3. De là, ils rejoignent une cuve d’aéroflottation qui permet de sortir les boues grasses et de les acheminer vers un le méthaniseur spécial. Le reste du liquide part ensuite dans deux digesteurs mésophiles de 55 m3 chacun, alimentés en continu.
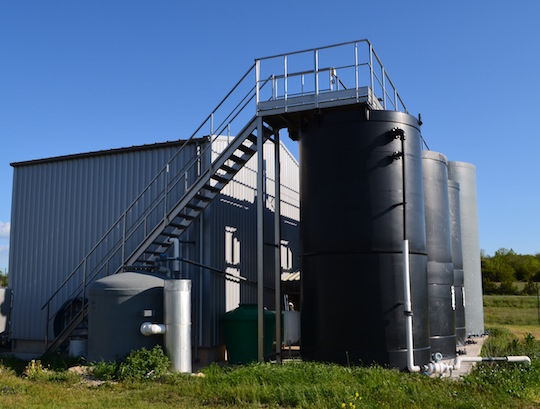
A gauche le petit réacteur de graisses, puis le clarificateur, deux bassins aérobie et le premier méthaniseur au fond, photo Frédéric Douard
Un gazomètre souple permet un stockage tampon du biogaz entre les digesteurs et la chaudière, qui déclenche dès que la pression de consigne minimum de la bâche est atteinte.
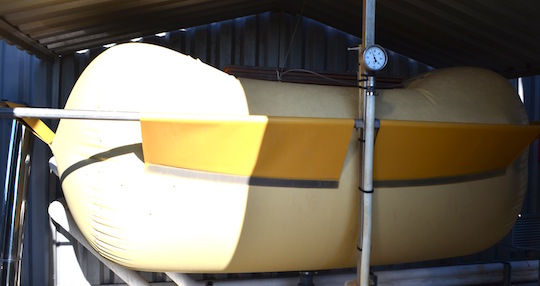
Le gazomètre souple, photo Frédéric Douard
Le biogaz est brûlé dans une chaudière Viessmann équipée d’un brûleur Weishaupt ; elle développe 95 kW. Cette chaleur est utilisée pour le chauffage des digesteurs et alimente en base un ballon tampon de 22 000 litres portés à 92°C. C’est ce ballon qui alimente le circuit primaire de chauffer le lait et qui assure la production d’’eau chaude sanitaire. En pratique, la chaudière à biogaz fonctionne tout au long de la journée dès que le gazomètre est suffisamment rempli. Cette production de chaleur est complétée par un brûleur à gaz naturel de 1 MW qui intervient ponctuellement notamment pendant les périodes de fort tirage.
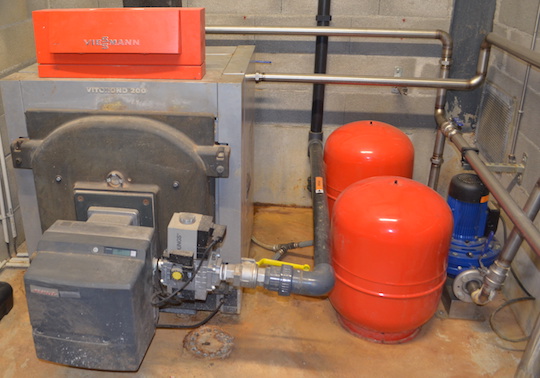
La chaudière à biogaz, photo Frédéric Douard
Les résultats
En ce début 2014, la chaudière à biogaz a tourné 1470 heures en 4 mois à pleine puissance (12 heures par jour), produisant 140 MWh utiles, soit 35 MWh de chaleur par mois. Sur les 35 MWh produit par mois, 28 servent au chauffage des digesteurs. Les 7 MWh supplémentaires sont disponibles pour la fromagerie et représentent 16% des besoins thermiques de celle-ci. Ceci est à comparer aux 35 autres MWh de chaleur produit par la gaz naturel chaque mois. Le % moyen de méthane constaté dans le biogaz est de l’ordre de 56%.
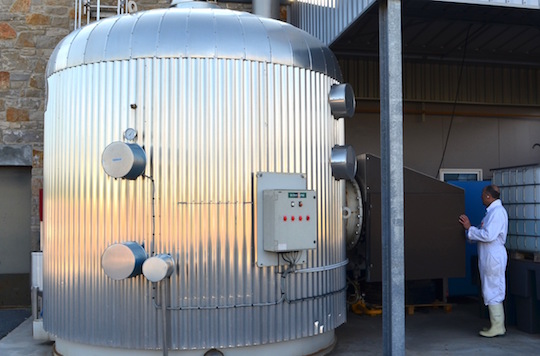
Le ballon d’eau chaude de 22000 litres, photo Frédéric Douard
La production de boue à épandre (digestat) est réduite à 8 m3 par mois et est stockée en benne agricole avant transfert sur fumière. Elle est épandue après mélange au fumier et compostage avec ce dernier.
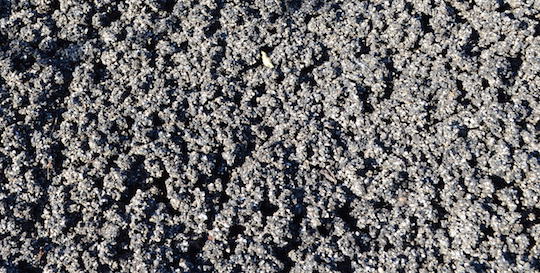
Le digestat, photo Frédéric Douard
Côté épuration de l’eau, le rejet moyen brut en entrée du digesteur est de 35 kg/m3 en DCO et de 0,9 kg/m3 en sortie. Ce chiffre est très constant ! C’est moins le cas en sortie du clarificateur où la DCO oscille entre 0,8 kg et 0,2 kg/m3.
Les investissements
En 2009, l’investissement méthanisation s’est monté à 720 000 €, la conception et l’installation ayant été réalisées par la société Valbio. En 2015, une nouvelle série d’investissements va être faite pour améliorer encore les performances de l’installation, pour un montant de 300 000 €. Un bassin supplémentaire de 150 m3 pour la réception des liquides est prévu pour absorber l’augmentation de volume due à la croissance de l’activité. Un grand gazomètre de 200 m3 permettra de stocker plus de biogaz, de le brûler la nuit pour préparer le ballon d’eau chaude de 22 m3 à la matinée de travail, et donc d’en valoriser plus qu’aujourd’hui avec le petit gazomètre.
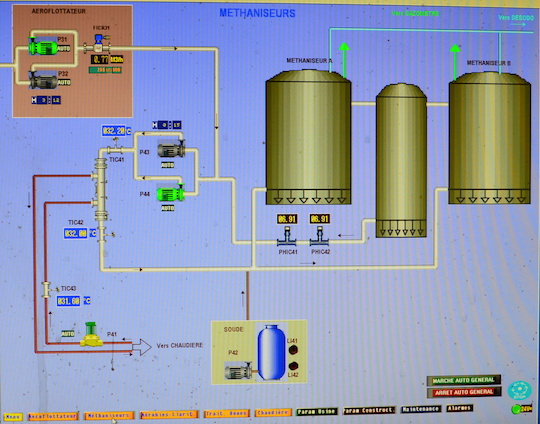
Synoptique de supervision des installation de digestion, photo Frédéric Douard
Derniers investissements prévus pour 2015 : un filtre pour le biogaz et une grande lagune étanche avec des phases de grande aération et de repos, pour obtenir un rejet en milieu naturel en dessous des 0,3 kg/m3 réglementaires.
Le retour d’expérience
A la question « Cinq ans après le début de cette aventure technologique, si c’était à refaire, que feriez-vous ? », André Parenti, le fondateur de la coopérative et directeur du site a répondu sans hésitation « je choisirais à nouveau la même voie, sauf que maintenant, j’ai beaucoup appris et je passerais beaucoup moins de temps à la mise au point du fonctionnement correspondant à notre contexte».
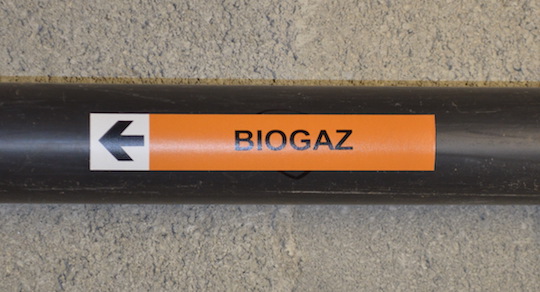
Arrivée du biogaz à la chaudière, photo Frédéric Douard
Car ajoute-t-il « Même si aujourd’hui nous sommes clairement économiquement gagnants, il est deux paramètres que nous avions sous-estimés : d’une part l’investissement personnel dans l’apprentissage de la conduite et de la résolution des aléas, et d’autre part, le temps qu’il faut passer tous les jours pour que tout marche sans encombre.» .
Et d’ajouter « Il faut compter un ¾ temps pour la conduite d’une telle installation, une fois qu’elle est maitrisée, ce qui est la cas aujourd’hui ».
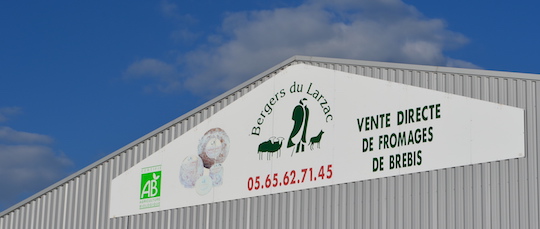
Le fronton de la fromagerie, photo Frédéric Douard
Frédéric Douard, en reportage à La Cavalerie
ℹ️ Le magazine Bioénergie International est disponible :
- Au détail
- Dans le cadre d'un abonnement