La Fonderie d’Anor coule des barreaux de grilles de chaudières à biomasse ou à déchets Made in France
Article paru dans le Bioénergie International n°92 de l’été 2024
Avec la croissance de la valorisation énergétique des déchets et de la biomasse solide, de nombreuses chaufferies décarbonées voient le jour en France, en Europe et dans le Monde. Pour répondre à cette demande, Saretco, une entreprise française basée à Marquise près de Boulogne-sur-Mer, muscle progressivement son offre et s’affiche aujourd’hui comme l’un des principaux fournisseurs français de pièces de fonderie pour la combustion. Elle conçoit et fabrique des barreaux et plaques pour grilles mobiles pour l’incinération des déchets et la combustion de biomasse solide. Elle produit également des cônes de filtres multicyclones pour le dépoussiérage des gaz de combustion ou encore des outils de coupe pour broyeurs de pâte à papier.
Une compétence pointue dans une économie mondialisée
Saretco s’appuie à la base sur la longue expérience de son fondateur, André Simper. Car avant de créer Saretco en 1985, André Simper fut directeur et ingénieur en métallurgie dans les fonderies de Manoir Industries en France et de Pleissner en Allemagne. Depuis, le fondateur s’est appuyé sur une jeune génération d’ingénieurs qui devrait prendre sa relève dans quelques années.
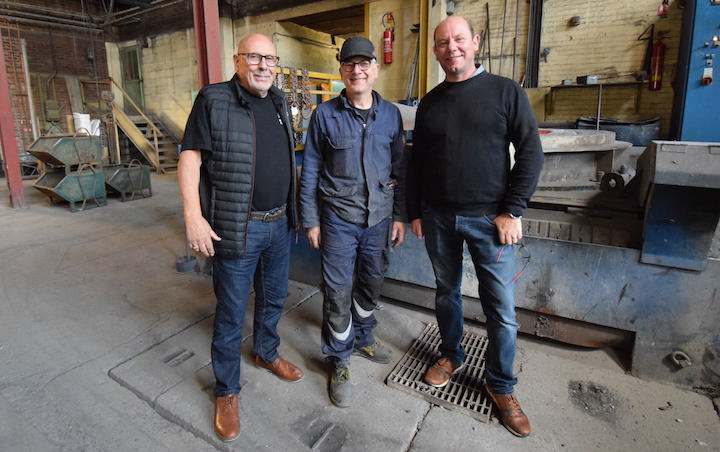
Depuis la gauche Andre Simper, président de Saretco, Pascal Paul-Constant, directeur de la Fonderie et Jimmy Sart, directeur développement chez Saretco, photo Frédéric Douard
L’activité de la société se partage à 60 % dans la production et la vente de pièces de rechange, ainsi que dans la maintenance de grandes installations de combustion, à 30 % dans l’amélioration de foyers et la conception de nouveaux barreaux, et à 10 % dans le renouvellement de grilles de combustion.
Pour la production de pièces, livrées dans plus de 25 pays, Saretco s’appuie principalement sur la production de sa fonderie en Turquie. Pour la France, Saretco dispose à Marquise d’un stock important comprenant plus de 5000 références. Mais ces dernières années, les tensions politiques internationales ont mis les chaines d’approvisionnement à rude épreuve. Aussi, pour garder de la souplesse et de la réactivité vis-à-vis de ses clients européens, André Simper a décidé de relocaliser en France une partie de sa production pour les commandes urgentes ou spéciales. Profitant d’une opportunité dans sa propre région, Les Hauts-de-France, il a repris une fonderie en 2020, créant une nouvelle société, la Fonderie d’Anor, du nom d’une petite ville industrielle située aux confins sud-est du département du Nord.
Une fonderie ressuscitée
La région de l’Avesnois, dont fait partie Anor, est un secteur industriel millénaire. Verre, forges et textile y ont fait vivre des cohortes d’ouvriers jusqu’à la fin du 20ème siècle. À Anor même, secteur riche en bois et en minerais, une forge est attestée dans les archives dès l’année 1100. Plus tard, au début des années 1500, dans un rayon de 20 km autour d’Anor, on ne compte pas moins de 14 haut-fourneaux qui emploient près de 2000 ouvriers. Les archives évoquent à cette époque une consommation de 60 000 stères de bois par an pour le fonctionnement de ces haut-fourneaux, pour une production de 2 à 3000 tonnes de fer (soit 20 stères par tonne de métal extrait), à quoi il faut ajouter de 6 à 9000 stères pour les fonderies.
Plus récemment, en 1902, en droite ligne de cet héritage historique, les Aciéries et Forges d’Anor sont fondées par Victor Poitte. Comptant jusqu’à 200 salariés, elle a fonctionné dans le giron familial durant quatre générations jusqu’en juillet 2019. L’entreprise comportait trois secteurs : la fonderie, l’usinage et le laminage. Les deux premières activités ont été reprises le 24 septembre 2020 par deux entreprises du Pas-de-Calais avec le soutien de la Communauté de communes Sud Avesnois. C’est Saretco qui a repris la partie fonderie avec ses 7 000
m² d’ateliers. Après une année de réorganisation en pleine période de Covid et de mise en place d’une nouvelle équipe d’une douzaine de personnes, la première coulée de la nouvelle société a eu lieu en mars 2021, sous la direction de Pascal Paul-Constant, responsable de fonderies.
Une fonderie à fort potentiel
En plus d’une bibliothèque de moules de plus d’un siècle d’activité, la Fonderie d’Anor bénéficie d’un équipement moderne avec en particulier cinq fours à induction, de différentes tailles (de 100 kg à 2 tonnes) pour la production de lots variés. L’usine comprend également son atelier de modelage pour la fabrication de modèles en bois, mis sur plaques puis utilisés dans des châssis métalliques. Ces châssis, permettent la fabrication des moules en sable à usage unique, sachant que 97 % du sable des moules usagers est recyclé après broyage pour confectionner de nouveaux moules.
Après démoulage, les pièces sont grenaillées, découpées des canaux d’alimentation, rectifiées et usinées, et pour certaines traitées thermiquement. Pour faire vivre cette usine, Saretco a fait le choix, d’une part, de suppléer à la fourniture d’une partie de son marché historique, les pièces pour la combustion, mais aussi de conserver les marchés historiques du site d’Anor comme des couteaux et marteaux de broyeurs ou les pièces d’usure pour triturateurs de bois ou de graines.
Un processus rigoureux pour des alliages précis
Le marché de la combustion nécessite des pièces en alliages spéciaux et superalliages résistants à la corrosion, à l’oxydation et à l’abrasion à hautes températures. Pour résister à de telles conditions durant des années, les alliages doivent s’adapter parfaitement aux produits brûlés et aux conditions d’utilisation de chaque client. Tel un chef cuisinier, à chaque fonte, le chef de production doit ainsi doser et adjuvanter ses matières premières pour obtenir l’alliage demandé.
La Fonderie d’Anor utilise 85 % de matières premières recyclées, issues notamment de la reprise de pièces usagées chez les clients. Et pour obtenir l’alliage voulu, sont ajoutés différents minerais ou métaux comme le chrome, le nickel ou le molybdène.
En pratique, chaque jour, un ou plusieurs fours sont mis en chauffe pour actuellement 3 tonnes de production quotidienne. Les fours sont alimentés en ferrailles choisies, complétées des métaux clés. Une fois la fonte effective, des prélèvements sont réalisés dans le four, au moyen d’un petit moule en céramique placé en bout de perche et qui va permettre de produire un échantillon de la taille d’une pièce de monnaie.
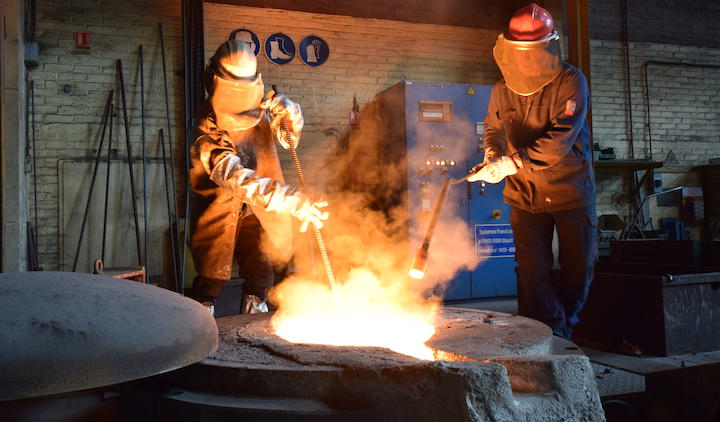
Mélange dans le four et prise d’échantillon avant la coulée à la Fonderie d’Anor, photo Frédéric Douard
L’échantillon est usiné et analysé au spectromètre d’émission optique, ce qui va préciser le pourcentage des différents éléments. Si ce pourcentage n’est pas celui attendu, le contenu en fusion est adjuvanté, de nouveau mesuré, et ce jusqu’à obtention des taux attendus.
Ensuite, la coulée peut être réalisée après vérification d’une température suffisante, comprise entre 1500 et 1600 °C. Les fours inclinables sont alors vidés progressivement dans une poche pour remplissage des moules. Une fois la coulée du jour terminée, la chaleur résiduelle du four, encore intense, est mise à profit pour fondre les matières qui seront utilisées le lendemain ou pour produire des lingots de matière première à partir des ferrailles de récupération.
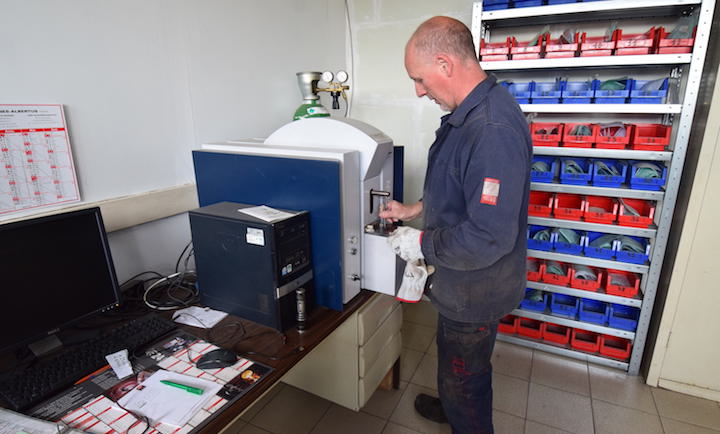
Analyse d’un échantillon au spectromètre d’émission optique avant un coulée à la Fonderie d’Anor, photo Frédéric Douard
Contact : 03 21 87 28 88 – contact@fonderie-anor.com – www.fonderie-anor.com – www.saretco.com/fr
Frédéric Douard, en reportage à Anor
Encore quelques images :
–
–
–
ℹ️ Le magazine Bioénergie International est disponible :
- Au détail
- Dans le cadre d'un abonnement