Analyse du fonctionnement de 33 unités de méthanisation à la ferme
Article paru dans le Bioénergie International n°51 de septembre-octobre 2017
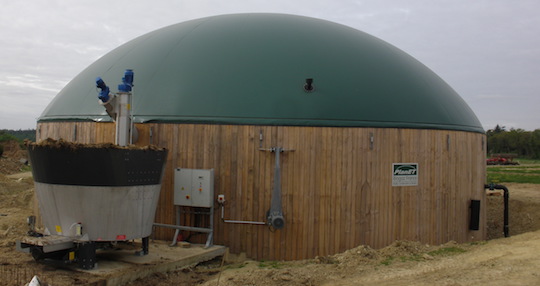
Digesteur de la Sarl Louelec à Locarn dans les Côtes dArmor, photo AILE
La méthode de travail
L’échantillon contient des unités relativement récentes (60 % ont 3 ans et moins) et de puissance inférieure à 160 kWé pour 45 % d’entre elles. 24 unités se situent en Bretagne et 9 en Pays de la Loire.
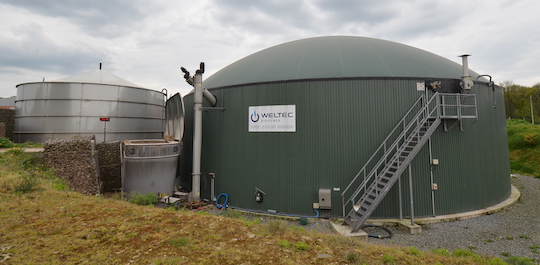
Les installations de méthanisation de Sensiénergies à Saint-Nicolas-du-Tertre, photo Frédéric Douard
Les données collectées étaient les suivantes :
- La ration détaillée
- La quantité de biogaz produit
- Le pourcentage de méthane
- La production électrique mensuelle
- La quantité d’électricité vendue
- La consommation d’électricité
- La production de chaleur
- La consommation de chaleur dans le processus
- La quantité de chaleur valorisée par poste d’utilisation
- Le taux de valorisation énergétique déclarée
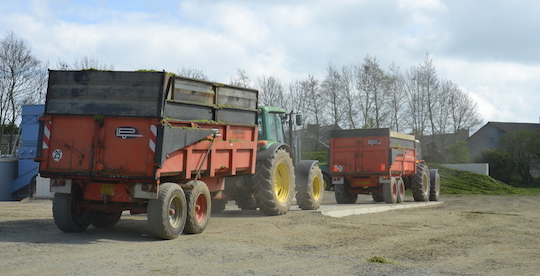
Livraison d’ensilage sur une installation de méthanisation agricole, photo Aile
Cette analyse distingue les données issues des unités en première année de fonctionnement, mise en service en 2014 ou début 2015), de celles issues d’années de « routine » soit deux ans et plus de fonctionnement.
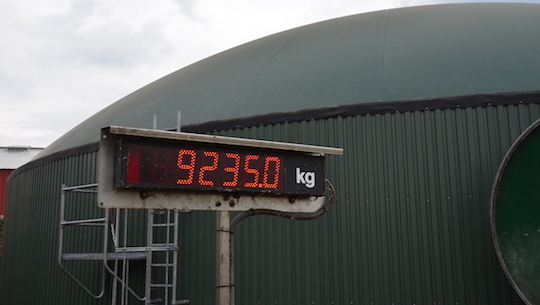
L’indicateur de pesée de l’incorporateur de Sensiénergies, photo Frédéric Douard
Concernant les indicateurs, les valeurs de calcul ont été mesurées et non pas estimées. Ceci a permis de fournir des résultats au plus près de la réalité mais a limité la quantité d’informations disponibles car tous les sites ne sont pas équipés des appareils qui permettent d’obtenir ces informations.
De plus, il a été fait le choix de ne pas faire de moyenne par unité qui fonctionne en routine mais de travailler avec des indicateurs annuels. Ainsi une même unité peut avoir plusieurs valeurs pour un même indicateur, ce qui correspond à plusieurs années. Chaque unité possède un numéro auquel peuvent se rattacher plusieurs années pour un indicateur.
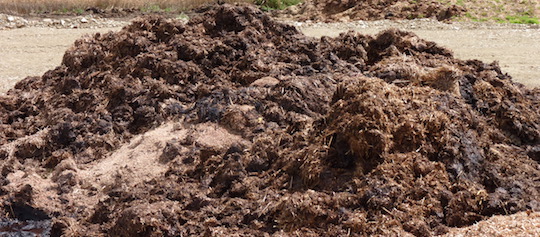
Les intrants utilisés par les unités en première année sont à près à 90 d’origine agricole, photo AILE
Pour les intrants, il a été décidé de faire la moyenne des intrants utilisés sur plusieurs années de fonctionnement. Ceci a facilité l’analyse mais a aussi gommé les variations qui ne sont pas dues directement au fonctionnement de l’unité, et ce en partant du principe qu’une unité de méthanisation se construit sur un plan d’approvisionnement le plus constant possible sauf cas d’augmentation de puissance. Pour les unités qui ont augmenté leur puissance entre 2013 et 2016, seules les données après augmentation ont été utilisées.
Les résultats sur les intrants
En moyenne 345 000 tonnes d’intrants par an alimentent ces 33 unités. Les ensilages sont constitués à 20 % par du maïs. Ceci équivaut à une surface cultivée de moins de 200 hectares pour l’ensemble avec un rendement de 12 tonnes MS/ha ou 40 tonnes MB/ha et un taux de MS de 30 %.
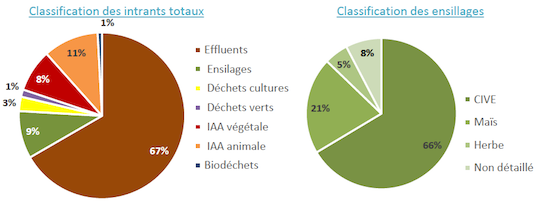
Répartition des intrants au global
Les intrants utilisés par les unités en première année sont à près de 90 % d’origine agricole et seulement à 70 % pour les unités en routine.
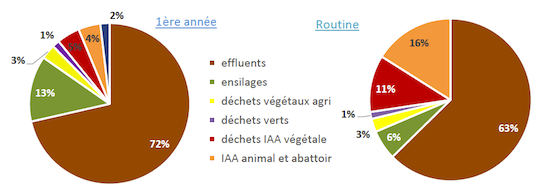
Répartition des intrants en première année de fonctionnement et routine
Les unités mises en service en 2011 ou avant utilisent moins de substrats agricoles que celles mises en fonctionnement après 2011. Les premières unités à la ferme ont été conçues dans un modèle de codigestion avec des déchets agro-alimentaires. De plus, le tarif BG11 mis en place en 2011 a instauré la prime effluents, une prime croissante à partir de 20 % d’effluents dans la ration jusqu’à 60 % où elle est maximale.
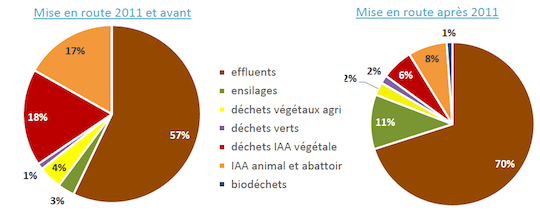
Répartition des intrants en fonction de l’année de mise en route
L’approvisionnement journalier est en moyenne de 25 tonnes par jour pour les unités en première année et de 28 tonnes pour celles en routine. Cette différence provient de la puissance des installations : 210 kWé de moyenne pour les unités en première année et 224 kWé pour celles en routine. Logiquement les installations plus puissantes incorporent plus de substrats.
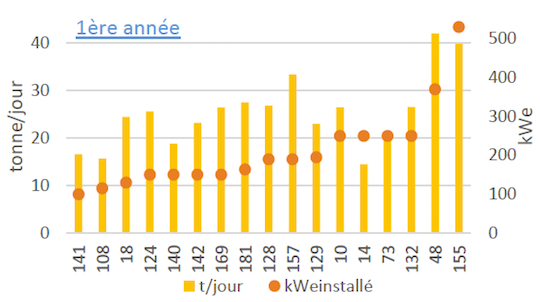
Approvisionnement journalier des unités la première année
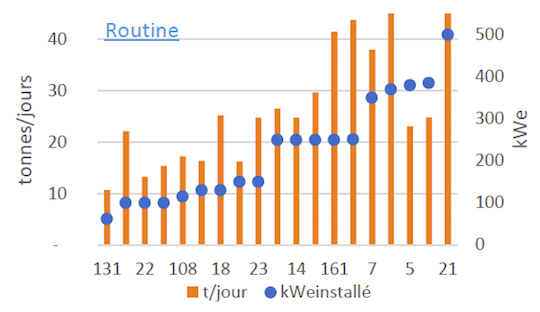
Approvisionnement journalier des unités en routine
Ramené au kWé installé, les unités en première année incorporent en moyenne 50 tonnes de substrat par an et par kWé installé et les unités en routine 49 tonnes. Il apparaît que les unités en première année avec une puissance plus élevée semblent incorporer moins de matière ramené au kWé que les unités avec une plus faible puissance. Même observation pour les unités en routine. Ceci pourrait venir du type d’intrants utilisés.
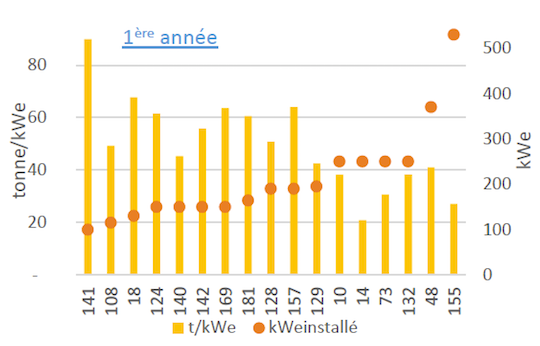
Tonnage d’intrants au kWe installé la première année
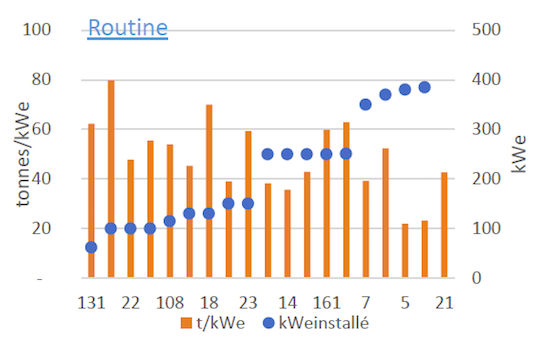
Tonnage d’intrants au kWe installé en routine
Les graphiques ci-dessous confirment l’hypothèse précédente. La ration moyenne annuelle des unités en première année de puissance inférieure à 220 kWé contient plus de 90 % de substrats agricoles contre moins de 80 % pour les unités supérieures à 220 kWé. Les substrats agricoles peuvent être moins méthanogènes que les substrats industriels, ce qui peut expliquer le plus faible tonnage au kWé installé pour les unités de puissance supérieure à 220 kWé. Même constat pour les unités en routine, presque 80 % de substrats d’origine agricole pour les moins de 220 kWé contre moins de 70 % pour les plus de 220 kWé.
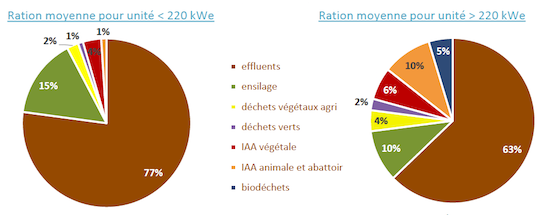
Ration annuelle moyenne en fonction de la puissance pour les unités en première année
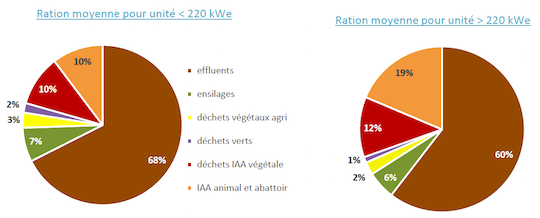
Ration annuelle moyenne en fonction de la puissance pour les unités en routine
La comparaison des intrants prévisionnels et des intrants réellement utilisés montre une plus faible quantité d’intrants réellement utilisés pour les unités en première année. Pour les unités en routine, la quantité réellement utilisée est supérieure au prévisionnel ; ce qui peut s’expliquer par l’évolution des unités et notamment par une augmentation de puissance.
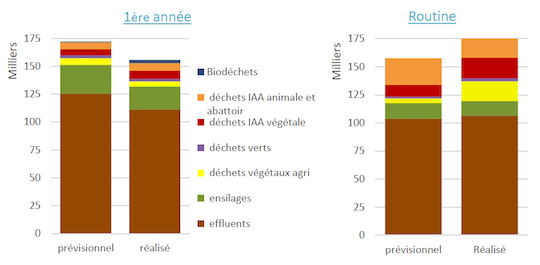
Intrants prévisionnels et intrants réellement utilisés en tonnes
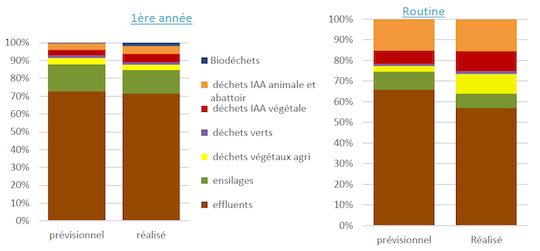
Intrants prévisionnels et intrants réellement utilisés en pourcentage
Une différence entre le prévisionnel et le réalisé en termes de pourcentage apparaît aussi. Moins marquée pour les unités en première année, les unités en routine semblent utiliser moins d’effluents qu’au prévisionnel et plus de déchets végétaux d’origine agricole.
Les résultats sur l’énergie
Le temps de fonctionnement à puissance maximale est de 7500 heures en moyenne aussi bien pour les unités en première année qui intègrent la montée en puissance que pour les unités en routine. On peut penser que les unités récemment mises en service atteignent plus facilement le régime de croisière que les premières mises en services (apprentissage de la filière).
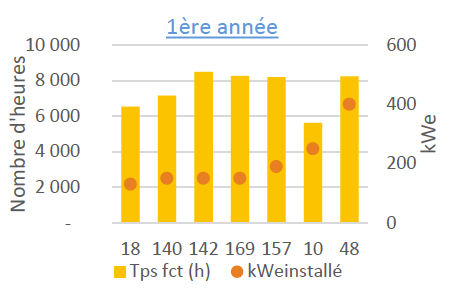
Temps de fonctionnement des moteurs de cogénération à puissance maximale la première année
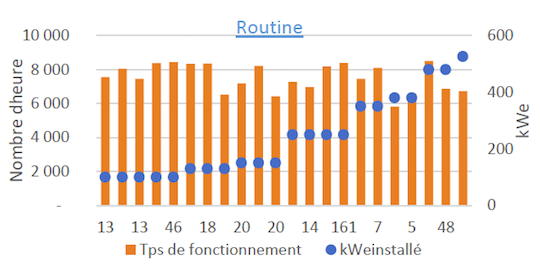
Temps de fonctionnement des moteurs de cogénération à puissance maximale en routine
Lors de la conception des projets, une valeur de 8000 h de fonctionnement est souvent prévue. Pour les unités en routine qui n’atteignent pas ces 8000 h, leur production d’électricité réalisée montre que la puissance maximale du moteur installé est surdimensionnée de 14 % en moyenne que ce qui serait nécessaire pour avoir un fonctionnement à puissance maximale de 8000 h. Autrement dit, en diminuant de 14 % la puissance maximale des moteurs installés, ces unités parviendraient à un temps de fonctionnement de 8000 h.
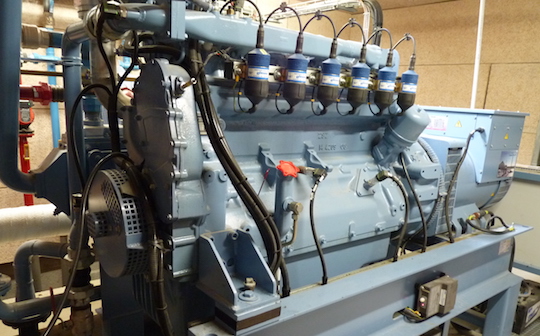
Le temps de fonctionnement à puissance maximale est de 7500 heures en moyenne , photo AILE
Le rendement moteur est en moyenne de 37 % pour les unités en première année (4 unités) et de 39 % pour les unités en routine (7 unités).
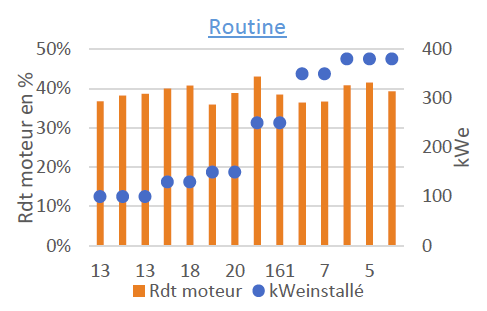
Rendement moteur
Le rendement moteur est un indicateur complexe à calculer et présente une précision modérée. Pour le calculer, il faut utiliser l’énergie primaire qui est obtenue notamment par le pourcentage de méthane dans le biogaz. Or, cette valeur est une moyenne qui peut varier de façon significative. Une valeur haute ou basse influencera donc le rendement moteur. Pour une même unité le rendement moteur varie d’une année sur l’autre.
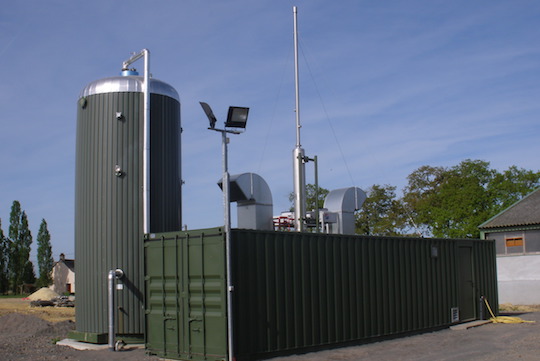
Conteneur de cogénération de la SCEA Bois Brillant à Saint-Sigismond (49), photo AILE
La consommation des auxiliaires représente 4 % de la production d’électricité en moyenne pour les unités en première année et 5 % pour les unités en routine. Ce pourcentage est dépendant de la production d’électricité mais aussi des éléments auxiliaires pris en compte sur l’unité.
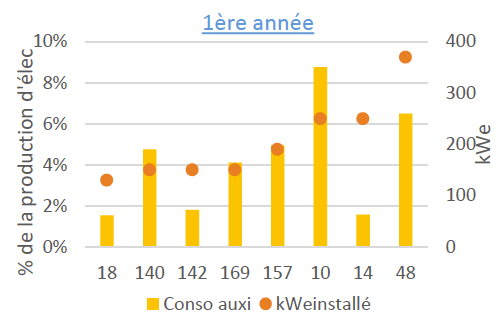
Consommation des auxiliaires en première année
La consommation électrique des auxiliaires ramenée au kWé installé est de 310 kWh en moyenne pour les unités en première année et de 340 kWh pour les unités en routine. Une différence apparaît en fonction de la puissance des unités en première année, moins marquée pour les unités en routine.
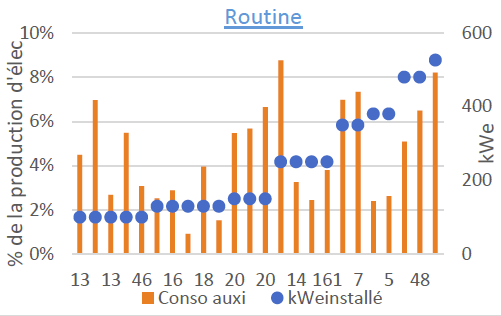
Consommation des auxiliaires en routine
La consommation des auxiliaires impacte de façon importante les recettes de l’unité de méthanisation et il semble important de bien la connaître pendant le fonctionnement de l’unité. Une unité exploitant un moteur de cogénération de 200 kWé et le faisant fonctionner 8000 h peut gagner 10000 €/an (selon le tarif 2016 avec la prime effluents) en réduisant de trois points (passage de 7 à 4 % de la production d’électricité par exemple) la consommation des auxiliaires.
La consommation électrique des unités est de 6 % de leur production en moyenne pour les unités en première année et de 11 % pour celles en routine. Ce ratio est aussi influencé par la production d’électricité.
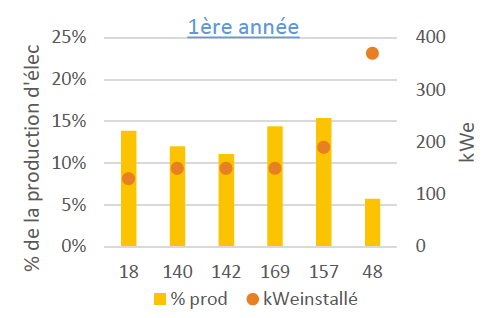
Consommation électrique exprimée en % de la production électrique en première année
Ramenée à la puissance installée, la consommation électrique équivaut à 900 kWh/kW pour les unités en première année et 760 kWh/kW pour les routines. Il n’y a pas de grande différence entre puissances pour les unités en routine et cela reste à confirmer pour les unités en première année.
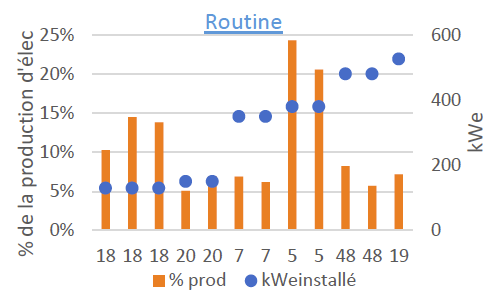
Consommation électrique exprimée en % de la production électrique en routine
La valorisation de l’énergie thermique est compliquée à étudier avec des valeurs mesurées. En effet, peu d’unités sont équipées de compteur de chaleur. Ainsi il n’est pas possible de faire ressortir des résultats précis.

Le rendement global passe une valorisation maximale de la chaleur, par exemple avec un séchoir, photo Frédéric Douard
Le taux d’efficacité énergétique calculé, en prenant en compte l’énergie thermique utilisée en substitution d’énergie électrique, est en moyenne de 54 % pour les unités en première année et de 64 % pour les unités en routine. Ces valeurs ont été obtenues sur un échantillon faible (3 unités en première année et 5 en routine). Il n’y a pas de différence notable entre le prévisionnel et le réalisé.
Conclusion
Cette analyse montre qu’il est possible de calculer un certain nombre d’indicateurs pour appréhender le fonctionnement des unités avec un ensemble de données basiques. Toutefois, ces données ne sont pas forcément disponibles sur toutes les unités par absence d’équipements ou de saisie des informations. Lors des enquêtes, il est en effet ressorti que la plupart des exploitants suivent effectivement les paramètres utiles pour conduire leur installation mais ne saisissent pas ces données.
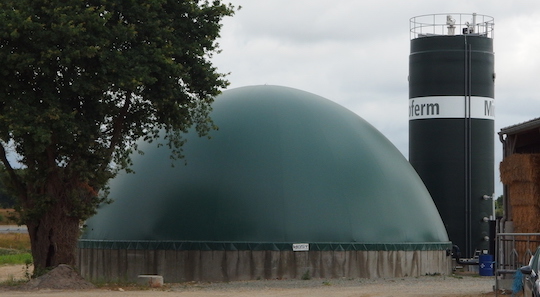
Installation du Gaec des Buissons à Saint-Lambert-la-Potherie, photo Aile
La capitalisation des données de fonctionnement représente cependant un enjeu majeur pour le bon fonctionnement et pour le développement de la filière. De nouveaux bilans de fonctionnement sur un plus grand nombre d’installations permettraient de suivre encore plus pertinemment les unités et leur évolution, pour le plus grand bénéfice des exploitants.
Contacts : AILE à Rennes (02 99 54 63 23) et à Nantes (02 40 16 37 81) – info@aile.asso.fr – www.aile.asso.fr
Frédéric Douard, d’après le bilan du Plan Biogaz 2007-2017 Bretagne et Pays de la Loire, réalisé par AILE et disponible in extenso à cette adresse : www.aile.asso.fr